Sputtering is a versatile physical vapor deposition (PVD) technique used to deposit thin films of materials onto substrates. It involves the ejection of atoms from a solid target material due to bombardment by energetic ions, typically in a vacuum environment. The process can be categorized into several types based on the method of ion generation, the nature of the power supply, and the specific applications. These types include DC diode sputtering, RF sputtering, magnetron sputtering, ion beam sputtering, reactive sputtering, and more. Each type has unique characteristics, advantages, and disadvantages, making them suitable for different applications in industries such as semiconductors, optics, and coatings.
Key Points Explained:
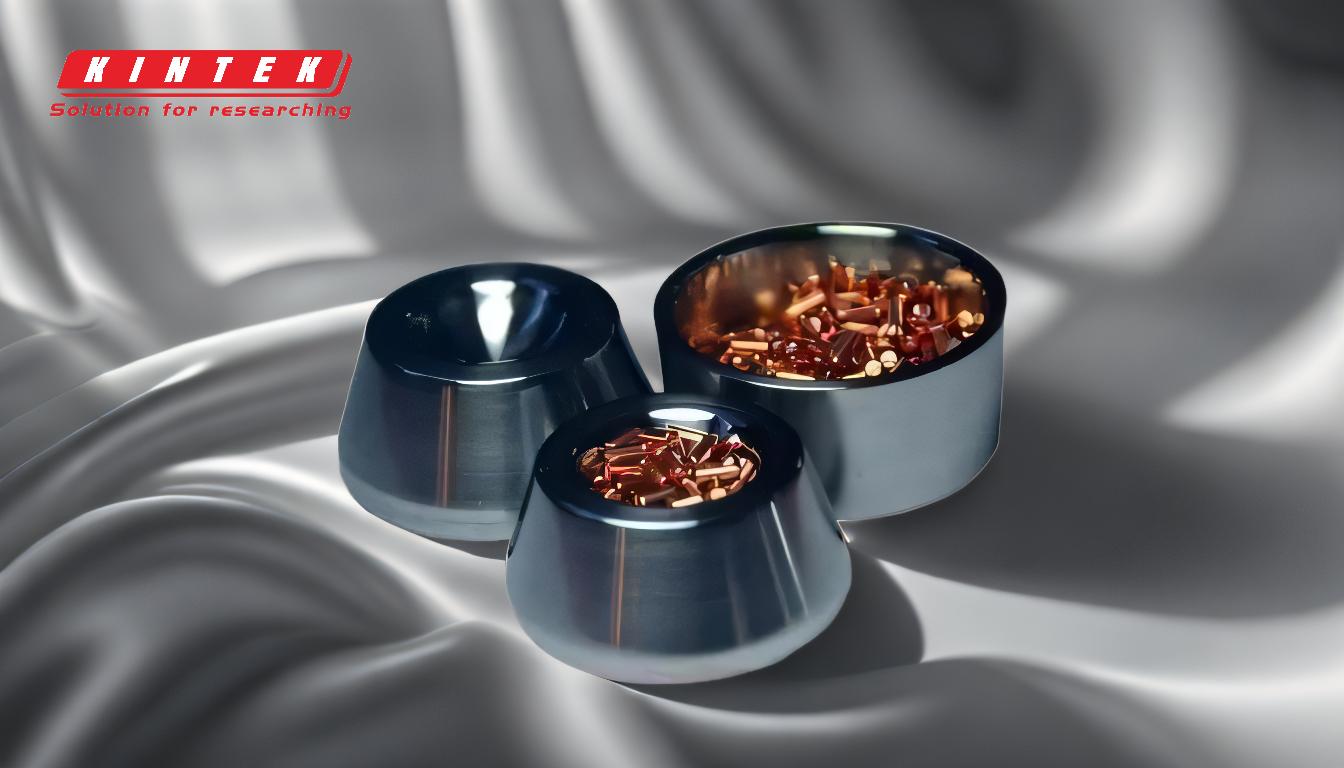
-
DC Diode Sputtering
- DC diode sputtering is one of the simplest and earliest forms of sputtering.
- It uses a direct current (DC) voltage (typically 500-1000 V) to ignite an argon low-pressure plasma between the target (cathode) and the substrate (anode).
- Positive argon ions bombard the target, ejecting atoms that then migrate to the substrate and condense into a thin film.
- Advantages: Simple setup, cost-effective, and suitable for conductive materials.
- Disadvantages: Limited to conductive targets, lower deposition rates, and potential for substrate heating.
-
RF Sputtering
- RF sputtering uses a high-frequency alternating field (typically 13.56 MHz) instead of a DC electric field.
- This method allows for the sputtering of insulating materials (e.g., ceramics and semiconductors) by preventing charge buildup on the target.
- Advantages: Capable of depositing insulating materials, reduced substrate heating, and higher sputtering rates at lower pressures.
- Disadvantages: More complex equipment and higher costs compared to DC sputtering.
-
Magnetron Sputtering
- Magnetron sputtering incorporates magnetic fields to enhance the ionization of the sputtering gas and increase the deposition rate.
- Types include:
- DC Magnetron Sputtering: Uses a DC power supply and is suitable for conductive materials.
- Pulsed DC Dual Magnetron Sputtering: Alternates the polarity of the target to prevent arcing, ideal for reactive sputtering.
- Rotating Magnet or Rotating Target DC Magnetron Sputtering: Improves target utilization and deposition uniformity.
- Advantages: High deposition rates, improved material utilization, and better film uniformity.
- Disadvantages: Requires precise control of magnetic fields and can be more expensive.
-
Ion Beam Sputtering (IBS)
- Ion beam sputtering uses a focused ion beam to sputter material from the target.
- The process is highly directional and allows for precise control over film thickness and composition.
- Advantages: High precision, excellent film quality, and minimal substrate damage.
- Disadvantages: Lower deposition rates and higher equipment costs.
-
Reactive Sputtering
- Reactive sputtering involves introducing a reactive gas (e.g., oxygen or nitrogen) into the sputtering chamber to form compound films (e.g., oxides or nitrides) on the substrate.
- Commonly used in conjunction with DC or RF sputtering.
- Advantages: Enables the deposition of compound materials with tailored properties.
- Disadvantages: Requires precise control of gas flow rates and can be prone to target poisoning.
-
Mid-Frequency (MF) and Pulsed DC Sputtering
- MF sputtering operates at frequencies between 10-100 kHz, while pulsed DC sputtering alternates the polarity of the target to prevent arcing.
- These methods are particularly useful for reactive sputtering and depositing insulating materials.
- Advantages: Reduced arcing, improved film quality, and compatibility with insulating targets.
- Disadvantages: More complex power supplies and higher costs.
-
High Power Impulse Magnetron Sputtering (HiPIMS)
- HiPIMS uses short, high-power pulses to achieve high ionization of the sputtered material.
- This results in dense, high-quality films with excellent adhesion.
- Advantages: Superior film quality, high ionization rates, and improved adhesion.
- Disadvantages: Lower deposition rates and higher equipment complexity.
-
Planar Diode RF Sputtering
- A variation of RF sputtering where the target and substrate are arranged in a planar configuration.
- Advantages: Uniform deposition and compatibility with insulating materials.
- Disadvantages: Limited to small-scale applications and lower deposition rates compared to magnetron sputtering.
-
Gas Flow Sputtering
- Gas flow sputtering uses a flowing gas to transport sputtered material to the substrate.
- Advantages: Suitable for depositing materials with low melting points and achieving uniform coatings on complex geometries.
- Disadvantages: Requires precise control of gas flow and can be less efficient for high-melting-point materials.
-
Ion-Assisted Sputtering
- Combines sputtering with ion bombardment of the substrate to improve film density and adhesion.
- Advantages: Enhanced film properties and better adhesion.
- Disadvantages: Increased complexity and higher costs.
In summary, sputtering techniques can be broadly classified based on the power supply (DC, RF, MF, pulsed DC, HiPIMS), the method of ion generation (magnetron, ion beam), and the presence of reactive gases (reactive sputtering). Each type has specific applications and trade-offs, making it essential to choose the right sputtering method based on the desired film properties, target material, and substrate requirements.
Summary Table:
Type of Sputtering | Key Features | Advantages | Disadvantages |
---|---|---|---|
DC Diode Sputtering | Simple setup, uses DC voltage (500-1000 V) | Cost-effective, suitable for conductive materials | Limited to conductive targets, lower deposition rates, substrate heating |
RF Sputtering | High-frequency alternating field (13.56 MHz) | Deposits insulating materials, reduced heating, higher rates at low pressure | Complex equipment, higher costs |
Magnetron Sputtering | Magnetic fields enhance ionization and deposition rates | High deposition rates, better film uniformity | Requires precise magnetic field control, higher costs |
Ion Beam Sputtering (IBS) | Focused ion beam for precise control | High precision, excellent film quality, minimal substrate damage | Lower deposition rates, higher equipment costs |
Reactive Sputtering | Introduces reactive gases (e.g., oxygen, nitrogen) | Deposits compound materials with tailored properties | Requires precise gas control, prone to target poisoning |
HiPIMS | Short, high-power pulses for high ionization | Superior film quality, high adhesion, dense films | Lower deposition rates, complex equipment |
Need help selecting the right sputtering technique for your application? Contact our experts today!