Sieve analysis is a fundamental method for determining the particle size distribution of granular materials. It involves separating particles into different size fractions using a stack of sieves with progressively smaller mesh sizes. The process can be carried out in several ways, depending on the equipment, methodology, and specific requirements of the analysis. The key variations include manual sieving, mechanical sieving, wet sieving, and dry sieving, each suited to different materials and objectives. The choice of method depends on factors such as the nature of the sample, the desired accuracy, and the available equipment.
Key Points Explained:
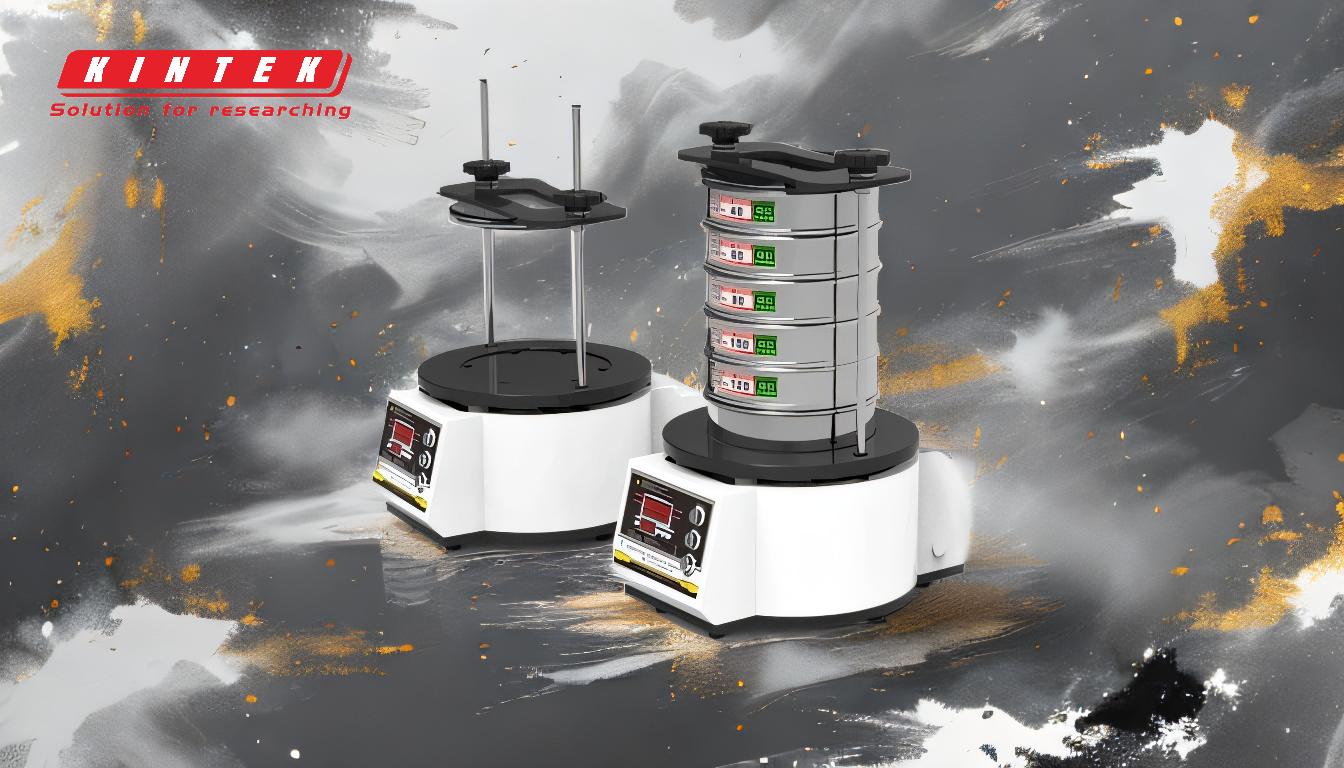
-
Manual Sieving
- Process: Involves manually shaking the sieve stack to separate particles.
- Use Case: Suitable for small-scale or preliminary analysis where precision is less critical.
- Advantages: Low cost, simple setup, and no need for specialized equipment.
- Limitations: Labor-intensive, less consistent results due to human variability, and not suitable for large sample sizes.
-
Mechanical Sieving
- Process: Uses a sieve shaker to automate the shaking process, ensuring consistent and repeatable results.
- Use Case: Ideal for routine analysis, large sample sizes, and when high precision is required.
- Advantages: Reduces human error, improves consistency, and saves time.
- Limitations: Requires investment in equipment and may not be suitable for fragile or sticky materials.
-
Wet Sieving
- Process: Involves adding water or another liquid to the sample to aid in the separation of fine particles that might otherwise clump together.
- Use Case: Suitable for materials that are difficult to sieve dry, such as clays or soils with high moisture content.
- Advantages: Prevents clogging of sieve openings and improves the accuracy of fine particle separation.
- Limitations: Requires additional steps for drying and weighing, and may introduce errors if not properly controlled.
-
Dry Sieving
- Process: Conducted without the use of liquids, relying solely on mechanical agitation to separate particles.
- Use Case: Suitable for free-flowing, dry materials like sand, gravel, or powders.
- Advantages: Simpler and faster than wet sieving, with no need for drying steps.
- Limitations: May not be effective for materials that tend to clump or have high moisture content.
-
Air Jet Sieving
- Process: Uses a stream of air to assist in the separation of fine particles, often combined with a vacuum to pull particles through the sieve.
- Use Case: Ideal for very fine powders or materials that are difficult to sieve using traditional methods.
- Advantages: Highly effective for fine particle separation, reduces clogging, and improves accuracy.
- Limitations: Requires specialized equipment and may not be suitable for all materials.
-
Nested Sieve Stack Analysis
- Process: Involves stacking multiple sieves in descending order of mesh size, allowing for the simultaneous separation of particles into multiple size fractions.
- Use Case: Commonly used for comprehensive particle size distribution analysis.
- Advantages: Efficient and provides a complete size distribution in a single run.
- Limitations: Requires careful handling to avoid cross-contamination between sieves.
-
Single Sieve Analysis
- Process: Focuses on separating particles using a single sieve to determine the proportion of material above or below a specific size threshold.
- Use Case: Useful for quality control or when only a specific size fraction is of interest.
- Advantages: Simple and quick, with minimal equipment requirements.
- Limitations: Provides limited information compared to nested sieve analysis.
-
Automated Sieve Analysis Systems
- Process: Utilizes advanced equipment with integrated weighing, shaking, and data analysis capabilities.
- Use Case: Suitable for high-throughput laboratories or industries requiring precise and repeatable results.
- Advantages: Reduces manual labor, improves accuracy, and provides detailed data analysis.
- Limitations: High initial cost and requires technical expertise to operate.
By understanding these methods, you can choose the most appropriate sieve analysis technique based on your specific needs, ensuring accurate and reliable results. Each method has its own strengths and limitations, making it essential to consider factors such as sample characteristics, desired precision, and available resources when selecting a sieving approach.
Summary Table:
Method | Process | Use Case | Advantages | Limitations |
---|---|---|---|---|
Manual Sieving | Manually shaking the sieve stack. | Small-scale or preliminary analysis. | Low cost, simple setup. | Labor-intensive, less consistent results. |
Mechanical Sieving | Uses a sieve shaker for automation. | Routine analysis, large sample sizes. | Reduces human error, improves consistency. | Requires equipment investment. |
Wet Sieving | Adds water to separate fine particles. | Materials difficult to sieve dry (e.g., clays). | Prevents clogging, improves fine particle separation. | Requires drying steps, may introduce errors. |
Dry Sieving | Relies on mechanical agitation without liquids. | Free-flowing, dry materials (e.g., sand, powders). | Simpler and faster than wet sieving. | Ineffective for clumping or high-moisture materials. |
Air Jet Sieving | Uses air stream and vacuum for fine particle separation. | Very fine powders or challenging materials. | Reduces clogging, improves accuracy. | Requires specialized equipment. |
Nested Sieve Stack | Stacks multiple sieves for simultaneous separation. | Comprehensive particle size distribution. | Efficient, complete size distribution in one run. | Risk of cross-contamination. |
Single Sieve Analysis | Uses one sieve to determine specific size fractions. | Quality control or specific size fraction analysis. | Simple, quick, minimal equipment. | Limited information compared to nested sieving. |
Automated Systems | Uses advanced equipment with integrated weighing and data analysis. | High-throughput labs requiring precision. | Reduces manual labor, improves accuracy and data analysis. | High initial cost, requires technical expertise. |
Need help choosing the right sieve analysis method for your materials? Contact our experts today for personalized guidance!