Diffusion pump oil should typically be changed every six months, as indicated by the maintenance guidelines. However, the frequency can vary depending on usage, operating conditions, and signs of contamination. Regular monitoring of oil quality, oil level, and pump performance is essential to determine if more frequent changes are necessary. Proper maintenance, including checking water flow, heater alignment, and cooling system functionality, also plays a critical role in ensuring the longevity and efficiency of the diffusion pump.
Key Points Explained:
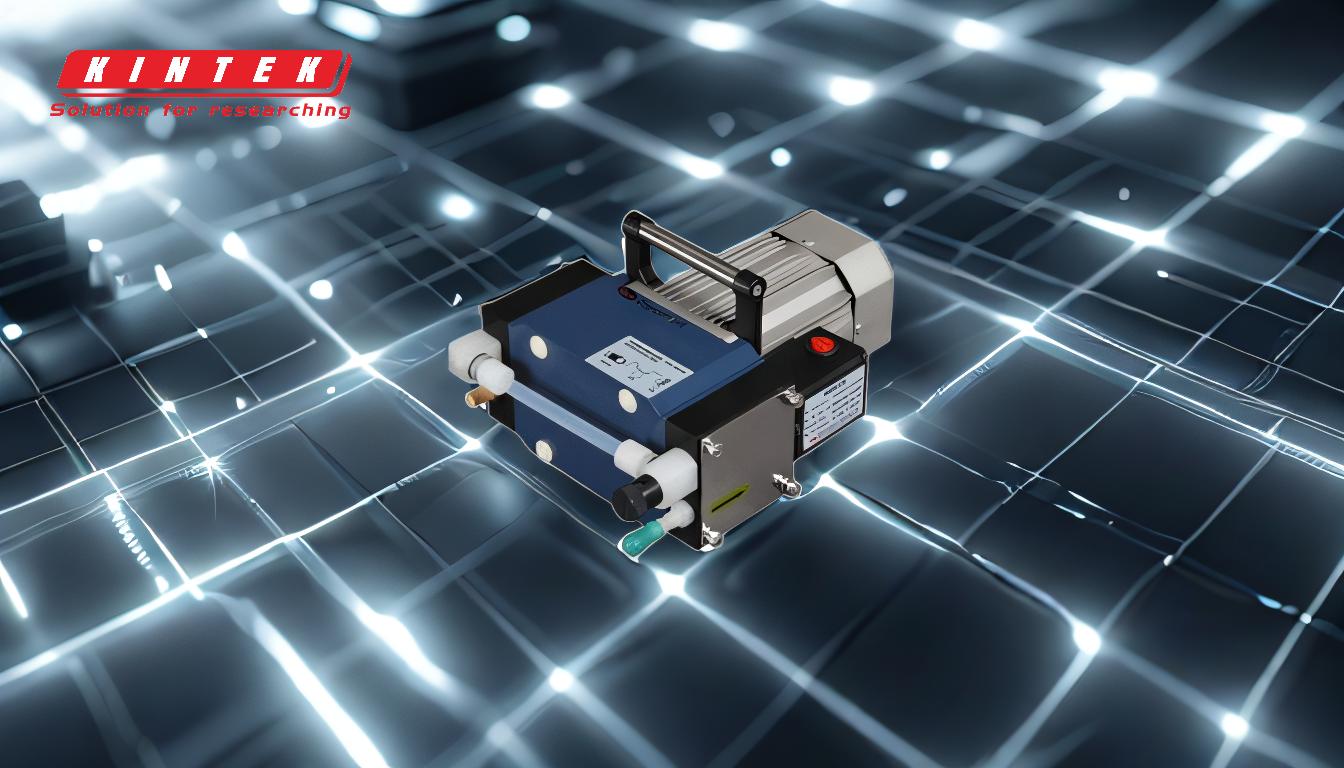
-
Standard Replacement Interval:
- The general recommendation is to change the diffusion pump oil every six months. This interval is based on typical operating conditions and helps prevent oil degradation, contamination, and reduced pump performance.
- Reasoning: Over time, the oil can accumulate contaminants, lose its viscosity, or break down due to exposure to high temperatures and vacuum conditions. Regular replacement ensures optimal pumping efficiency and reduces the risk of pump failure.
-
Monitoring Oil Quality and Level:
- Regularly check the oil level in the pump's oil window and inspect for signs of contamination, such as discoloration or the presence of particles.
- Reasoning: Contaminated or degraded oil can compromise the pump's ability to maintain a high vacuum, leading to inefficiency or damage to the pump components. Monitoring ensures timely intervention before issues escalate.
-
Operating Conditions and Usage:
- The frequency of oil changes may vary depending on the pump's operating environment, such as temperature, humidity, and the type of materials being processed.
- Reasoning: Harsher operating conditions, such as high temperatures or exposure to reactive gases, can accelerate oil degradation, necessitating more frequent changes.
-
Cooling System Maintenance:
- Ensure the cooling water system is functioning correctly, as overheating can degrade the oil faster. Check water flow, inlet and outlet temperatures, and cooling line integrity.
- Reasoning: Proper cooling prevents excessive heat buildup, which can cause the oil to break down prematurely and affect the pump's performance.
-
Heater Alignment and Functionality:
- Verify that the heating elements are properly aligned and functioning within the specified electrical parameters. Misaligned or malfunctioning heaters can lead to uneven heating and oil degradation.
- Reasoning: Correct heater operation ensures consistent oil temperature, which is critical for maintaining the pump's efficiency and preventing localized overheating.
-
Signs Indicating Immediate Oil Change:
- If the oil appears dark, cloudy, or contains particulates, or if the pump's performance declines (e.g., slower pumping speed), an immediate oil change is recommended.
- Reasoning: These signs indicate that the oil is no longer effective and may be causing harm to the pump or reducing its efficiency.
-
Procedure for Oil Change:
- Drain and replace the oil only when the pump is cold to avoid safety hazards and ensure thorough cleaning. Clean the pump internals, including the jet assembly, before refilling with new oil.
- Reasoning: Cleaning removes residual contaminants, and cold oil draining prevents accidental burns or spills, ensuring a safe and effective maintenance process.
-
Comparison with Other Pump Types:
- Unlike oil-free pumps like scroll pumps, diffusion pumps rely on oil for operation, making regular oil changes a critical maintenance task.
- Reasoning: Oil-dependent pumps require more frequent maintenance to ensure optimal performance, whereas oil-free pumps have fewer maintenance requirements but may need frequent seal replacements.
By adhering to these guidelines, users can maintain their diffusion pumps effectively, ensuring long-term reliability and performance. Regular monitoring and timely oil changes are key to preventing costly repairs and downtime.
Summary Table:
Aspect | Details |
---|---|
Standard Replacement Interval | Change oil every 6 months to prevent degradation and contamination. |
Monitoring Oil Quality | Check oil level and look for discoloration or particles regularly. |
Operating Conditions | Adjust frequency based on temperature, humidity, and material exposure. |
Cooling System Maintenance | Ensure proper water flow and cooling to prevent overheating. |
Heater Alignment | Verify heater alignment and functionality for consistent oil temperature. |
Signs for Immediate Change | Dark, cloudy oil or reduced pump performance indicates an urgent oil change. |
Oil Change Procedure | Drain and replace oil when cold, and clean internals thoroughly. |
Comparison with Oil-Free Pumps | Oil-dependent pumps require more frequent maintenance than oil-free pumps. |
Ensure your diffusion pump runs smoothly—contact us today for expert maintenance advice!