Plastic can be converted into fuel through advanced chemical and catalytic processes, offering a sustainable solution to plastic waste management. Two prominent methods include catalytic conversion using ruthenium and carbon catalysts, and photo-reforming using light-absorbing photocatalysts. The catalytic method efficiently converts 90% of plastic waste into fuel at lower temperatures, making it faster and more economical. Photo-reforming, on the other hand, uses sunlight and an alkaline solution to break down plastic into hydrogen gas. Despite these advancements, challenges such as pollutant emissions, health risks, and economic impacts on existing waste-to-fuel processes remain. These methods, however, represent significant progress in addressing plastic pollution and energy recovery.
Key Points Explained:
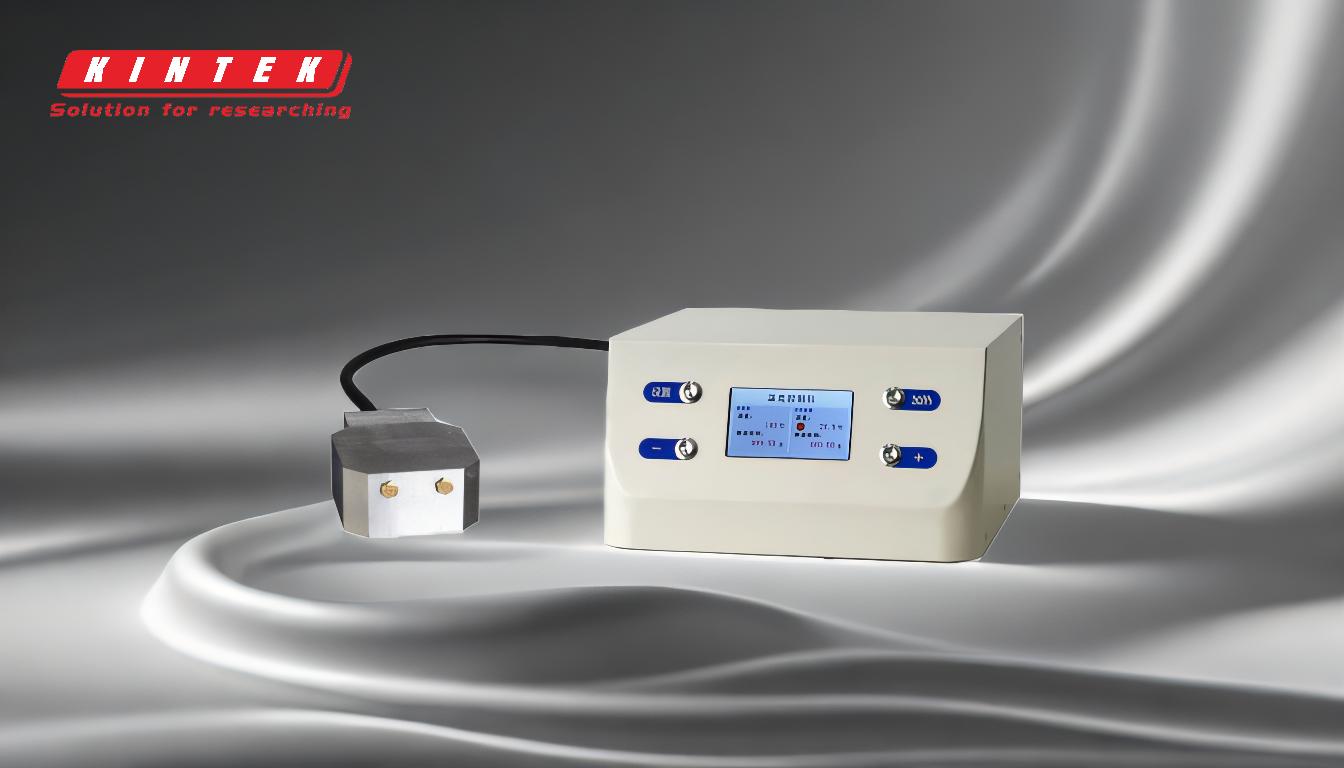
-
Catalytic Conversion of Plastic to Fuel
- A combination of ruthenium metal and carbon acts as a catalyst to convert plastic waste into fuel.
- This process achieves a 90% conversion rate, making it highly efficient.
- It operates at lower temperatures compared to traditional chemical recycling methods, reducing energy consumption and costs.
- The method is faster and more economical, making it suitable for widespread adoption.
-
Photo-Reforming: Converting Plastic to Hydrogen Fuel
- Researchers at Swansea University developed a method called photo-reforming.
- A light-absorbing photocatalyst is added to plastic products.
- The plastic-photocatalyst mixture is exposed to sunlight in an alkaline solution, causing the plastic to break down.
- This process produces hydrogen gas bubbles, which can be captured and used as a clean fuel source.
-
Steps Involved in Plastic Pyrolysis
- Plastic waste is shredded and dried to prepare it for processing.
- Non-plastic materials are separated during preprocessing.
- The plastic undergoes pyrolysis, a thermal decomposition process in the absence of oxygen.
- The resulting pyrolysis oil is distilled and purified to remove impurities.
- The purified oil is stored and dispatched for use as fuel.
-
Challenges in Plastic-to-Fuel Conversion
- Health risks associated with energy recovery processes, such as exposure to harmful chemicals.
- Emission of pollutants like nitrous oxides and sulfur dioxides during combustion.
- Economic concerns for countries like Sweden, which rely on importing garbage for waste-to-fuel processes.
- Potential competition with other waste-to-fuel technologies, such as solid waste-to-fuel, which could impact their economic viability.
-
Environmental and Economic Implications
- These methods offer a dual benefit: reducing plastic waste and generating usable fuel.
- They contribute to a circular economy by turning waste into a valuable resource.
- However, careful management is required to mitigate environmental and health risks.
- Policymakers and industries must balance the economic benefits with sustainability goals.
-
Future Prospects
- Continued research and development can improve the efficiency and scalability of these methods.
- Addressing the challenges of pollutant emissions and health risks will be critical for widespread adoption.
- Integrating these technologies with existing waste management systems could enhance their impact.
- Public awareness and policy support are essential to drive the adoption of plastic-to-fuel technologies.
By leveraging these innovative methods, plastic waste can be transformed into a valuable energy resource, contributing to both environmental sustainability and energy security.
Summary Table:
Method | Key Features | Efficiency | Challenges |
---|---|---|---|
Catalytic Conversion | Uses ruthenium and carbon catalysts; operates at lower temperatures. | 90% conversion | Pollutant emissions, health risks, economic impacts on waste-to-fuel processes. |
Photo-Reforming | Uses sunlight and alkaline solution; produces hydrogen gas as a clean fuel. | High | Scalability, integration with existing waste systems, public awareness needed. |
Plastic Pyrolysis | Involves shredding, drying, and thermal decomposition of plastic into oil. | Moderate | Energy-intensive process, requires purification and storage of pyrolysis oil. |
Transform plastic waste into sustainable fuel—contact us today to learn more!