CVD (Chemical Vapor Deposition) coatings are widely used in various industries due to their ability to provide dense, pure, and uniform coatings. The thickness of CVD coatings typically ranges between 5-20 microns, depending on the application and material. This thickness is significantly higher than PVD (Physical Vapor Deposition) coatings, which are usually 2-5 microns thick. CVD coatings are known for their excellent adhesion and ability to coat complex geometries, including deep holes and internal walls. However, the high processing temperatures (800-1000 °C) and the resulting tensile stress during cooling can lead to fine cracks, making CVD less suitable for interrupted cutting processes. Despite these limitations, CVD coatings are highly resistant to abrasion and wear, making them ideal for applications involving irregularly shaped tools and semiconductor coatings.
Key Points Explained:
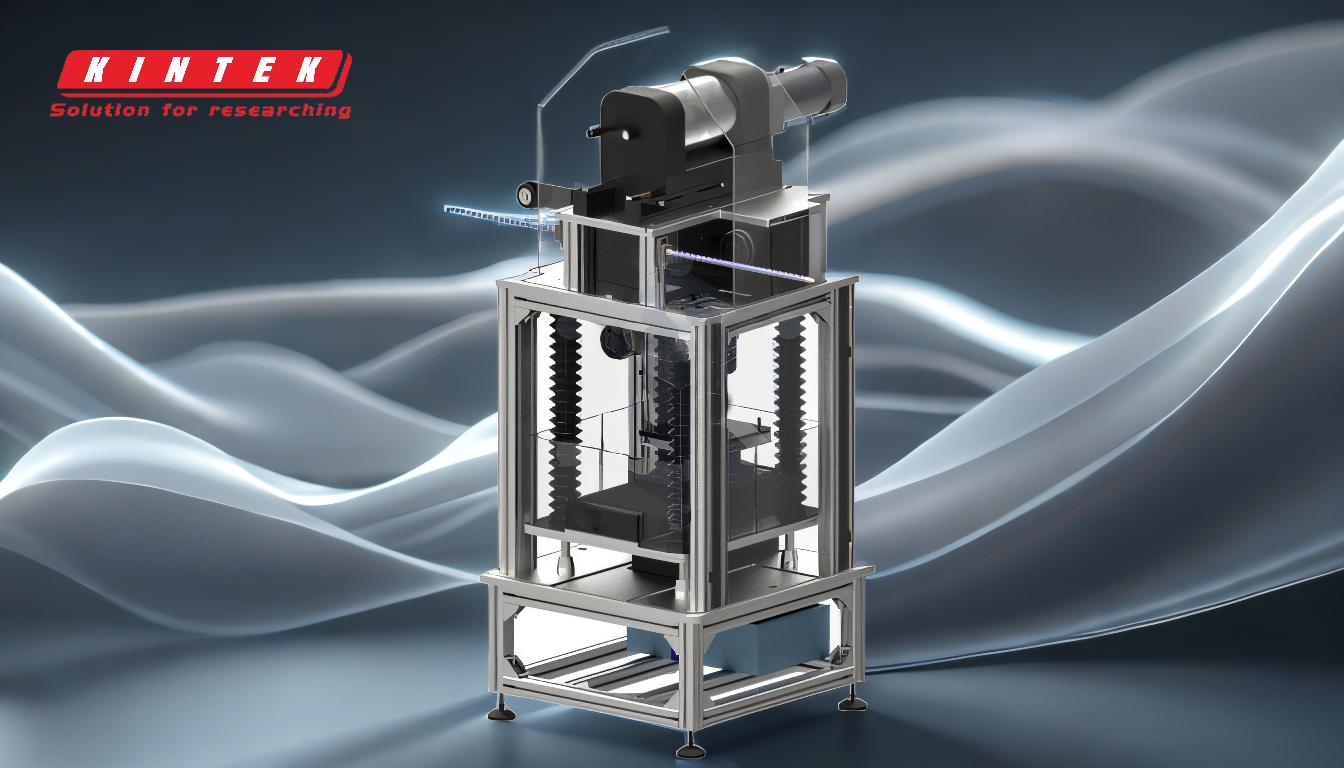
-
Typical Thickness of CVD Coatings:
- CVD coatings are generally thicker than PVD coatings, with a typical thickness range of 5-10 microns. However, in some cases, the thickness can extend up to 10-20 microns, especially for applications requiring higher durability and wear resistance.
- This increased thickness is due to the nature of the CVD process, which allows for the deposition of dense and uniform layers over the substrate.
-
Comparison with PVD Coatings:
- PVD coatings are usually thinner, ranging from 2-5 microns, and are applied at lower temperatures compared to CVD.
- While PVD coatings are suitable for applications requiring fine finishes and lower thicknesses, CVD coatings are preferred for their ability to provide thicker, more durable layers, especially in high-temperature and high-wear environments.
-
Impact of High Processing Temperatures:
- CVD processes operate at very high temperatures, often between 800-1000 °C, which can exceed the tempering temperature of some materials like high-speed steel.
- These high temperatures can lead to tensile stress during cooling, causing fine cracks in the coating. This makes CVD less suitable for interrupted cutting processes, such as milling, where the cutting force is not uniform and continuous.
-
Adhesion and Coating Uniformity:
- CVD coatings are known for their superior adhesion to the substrate, as the coating bonds to the surface during the chemical reaction.
- The process is not limited to line-of-sight application, allowing the coating gas to reach all areas of a part, including deep holes and internal walls. This makes CVD ideal for coating complex geometries.
-
Applications and Limitations:
- CVD coatings are highly resistant to abrasion and wear, making them suitable for applications involving irregularly shaped tools like drill bits and end mills.
- They are also used in creating semiconductor coatings for electrical equipment.
- However, the high processing temperatures and potential for cracking limit the base materials that can be coated, requiring materials with high temperature resistance, such as cemented carbide.
-
Surface Finish and Stress Considerations:
- CVD coatings tend to have a slightly rougher surface compared to the substrate, which can be a consideration for applications requiring a fine finish.
- The tensile stress generated during cooling can lead to fine cracks, which may spread under external impact, causing the coating to peel off. This is a critical factor to consider in applications involving high mechanical stress.
In summary, CVD coatings offer a versatile and effective solution for applications requiring thick, durable, and uniform coatings. However, the high processing temperatures and potential for stress-related cracking must be carefully managed, especially in applications involving interrupted cutting or high mechanical stress.
Summary Table:
Aspect | CVD Coating Details |
---|---|
Typical Thickness | 5-10 microns (can extend to 10-20 microns for high durability) |
Comparison with PVD | PVD: 2-5 microns; CVD is thicker and more durable |
Processing Temperature | 800-1000 °C (high temperatures can cause tensile stress and fine cracks) |
Adhesion & Uniformity | Superior adhesion; can coat complex geometries, including deep holes and internal walls |
Applications | Irregularly shaped tools, semiconductor coatings, high-wear environments |
Limitations | High temperatures may cause cracking; less suitable for interrupted cutting processes |
Need durable coatings for your tools or equipment? Contact our experts today to learn more about CVD coatings!