Sputter coating is a critical step in preparing non-conductive or poorly conductive samples for scanning electron microscopy (SEM). The process involves depositing a thin layer of conductive material, such as gold, platinum, or carbon, onto the specimen. The thickness of this coating typically ranges from a few angstroms to several nanometers, depending on the application and the material used. This thin layer enhances conductivity, reduces charging effects, and improves the quality of SEM imaging. The choice of coating material depends on the specific requirements of the analysis, such as high-resolution imaging or elemental analysis using energy-dispersive X-ray spectroscopy (EDX).
Key Points Explained:
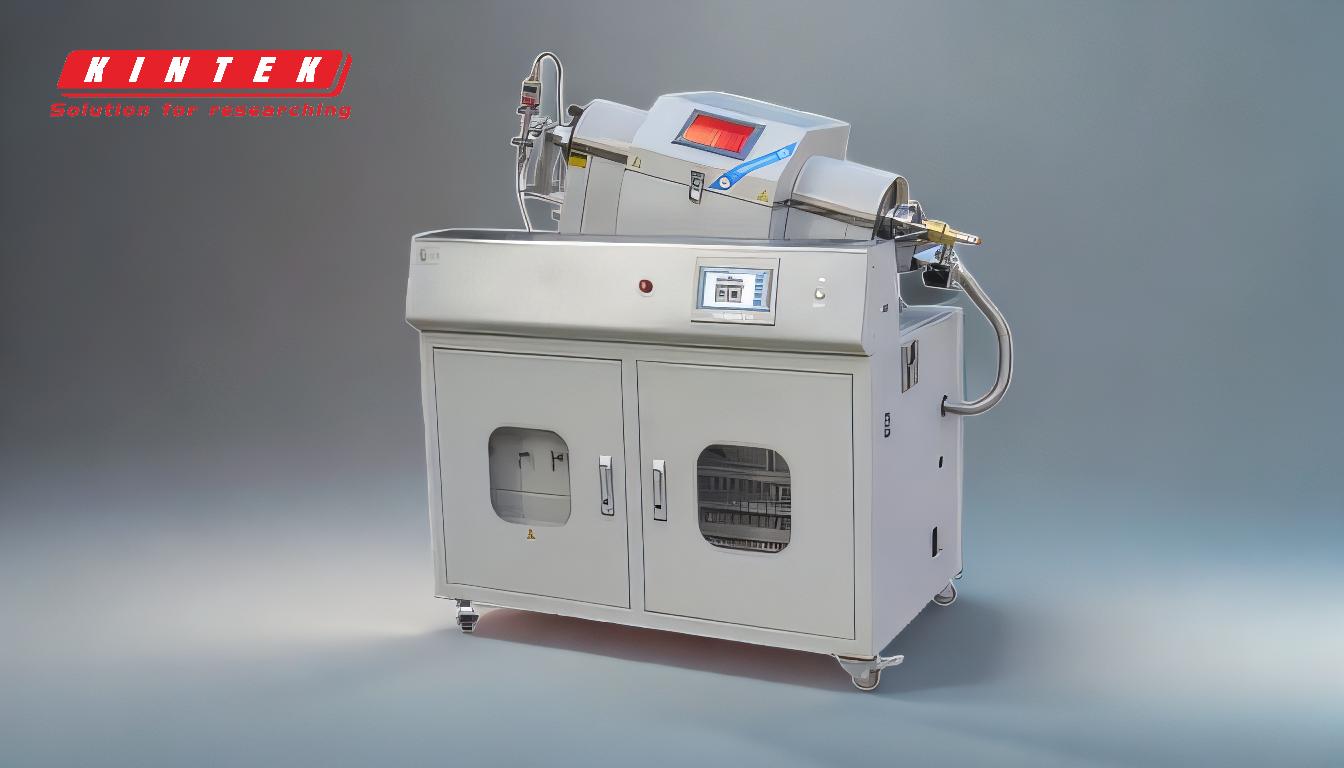
-
Purpose of Sputter Coating in SEM:
- Sputter coating is used to apply a thin conductive layer to non-conductive or poorly conductive samples. This layer prevents charging when the sample is exposed to the electron beam in SEM, ensuring clear and accurate imaging.
- It also improves secondary electron emission, reduces beam damage, and enhances thermal conduction, which is particularly important for beam-sensitive specimens.
-
Common Materials Used for Sputter Coating:
- Gold (Au): Widely used due to its high conductivity and small grain size, which ensures high-resolution imaging.
- Carbon (C): Preferred for EDX analysis because its X-ray peak does not interfere with other elements, making it ideal for elemental analysis.
- Platinum (Pt): Offers excellent conductivity and is often used for high-resolution imaging.
- Gold/Palladium (Au/Pd) Alloy: Combines the benefits of gold and palladium, providing a balance between conductivity and grain size.
- Other materials like silver, chromium, tungsten, and iridium are also used based on specific application needs.
-
Thickness of Sputter Coatings:
- The thickness of sputter coatings typically ranges from a few angstroms (Å) to several nanometers (nm). For most SEM applications, a coating thickness of 2–20 nm is common.
- Thicker coatings (e.g., 10–20 nm) are used for samples requiring enhanced conductivity or protection from beam damage, while thinner coatings (e.g., 2–5 nm) are preferred for high-resolution imaging to avoid obscuring fine surface details.
-
Factors Influencing Coating Thickness:
- Imaging Requirements: High-resolution imaging requires thinner coatings to avoid masking fine surface features.
- Sample Conductivity: Poorly conductive samples may require thicker coatings to ensure adequate conductivity and prevent charging.
- Beam Sensitivity: Beam-sensitive samples benefit from thicker coatings to protect against beam damage.
- Analysis Type: For EDX analysis, thinner coatings are preferred to minimize interference with the sample's elemental composition.
-
Benefits of Sputter Coating:
- Reduced Charging: The conductive layer prevents the buildup of static charge on the sample surface.
- Improved Image Quality: Enhanced secondary electron emission results in clearer and more detailed images.
- Protection Against Beam Damage: The coating acts as a protective barrier, reducing the risk of beam-induced damage to sensitive samples.
- Thermal Conduction: The conductive layer helps dissipate heat generated by the electron beam, minimizing thermal damage.
-
Selection of Coating Material:
- The choice of material depends on the specific requirements of the analysis:
- Gold: Ideal for high-resolution imaging due to its small grain size and high conductivity.
- Carbon: Best suited for EDX analysis, as it does not interfere with elemental detection.
- Platinum: Offers excellent conductivity and is often used for high-resolution imaging.
- Gold/Palladium Alloy: Provides a balance between conductivity and grain size, making it suitable for a wide range of applications.
- The choice of material depends on the specific requirements of the analysis:
-
Application-Specific Considerations:
- For high-resolution imaging, thinner coatings (2–5 nm) of materials like gold or platinum are preferred to avoid obscuring fine surface details.
- For EDX analysis, carbon coatings are ideal due to their minimal interference with elemental detection.
- For beam-sensitive samples, thicker coatings (10–20 nm) of materials like gold or platinum are used to provide additional protection against beam damage.
In summary, the thickness of sputter coatings for SEM typically ranges from a few angstroms to several nanometers, with the exact thickness depending on the specific application and material used. The choice of coating material and thickness is crucial for achieving optimal imaging and analytical results in SEM.
Summary Table:
Aspect | Details |
---|---|
Typical Thickness | 2–20 nm (a few angstroms to several nanometers) |
Common Materials | Gold, Carbon, Platinum, Gold/Palladium Alloy |
Thin Coatings (2–5 nm) | Ideal for high-resolution imaging, avoids masking fine surface details |
Thick Coatings (10–20 nm) | Enhances conductivity and protects beam-sensitive samples |
Key Benefits | Reduces charging, improves image quality, protects against beam damage |
Need help selecting the right sputter coating for your SEM analysis? Contact our experts today!