Creating an inert atmosphere in a furnace involves removing reactive gases like oxygen and replacing them with inert gases such as argon or nitrogen. This process prevents oxidation and other undesirable chemical reactions during high-temperature treatments. The key steps include creating a vacuum to remove oxygen and other reactive gases, followed by purging the furnace with inert gas to establish a stable, non-reactive environment. This method is essential for applications like metal heat treatment, where maintaining material integrity and surface quality is critical.
Key Points Explained:
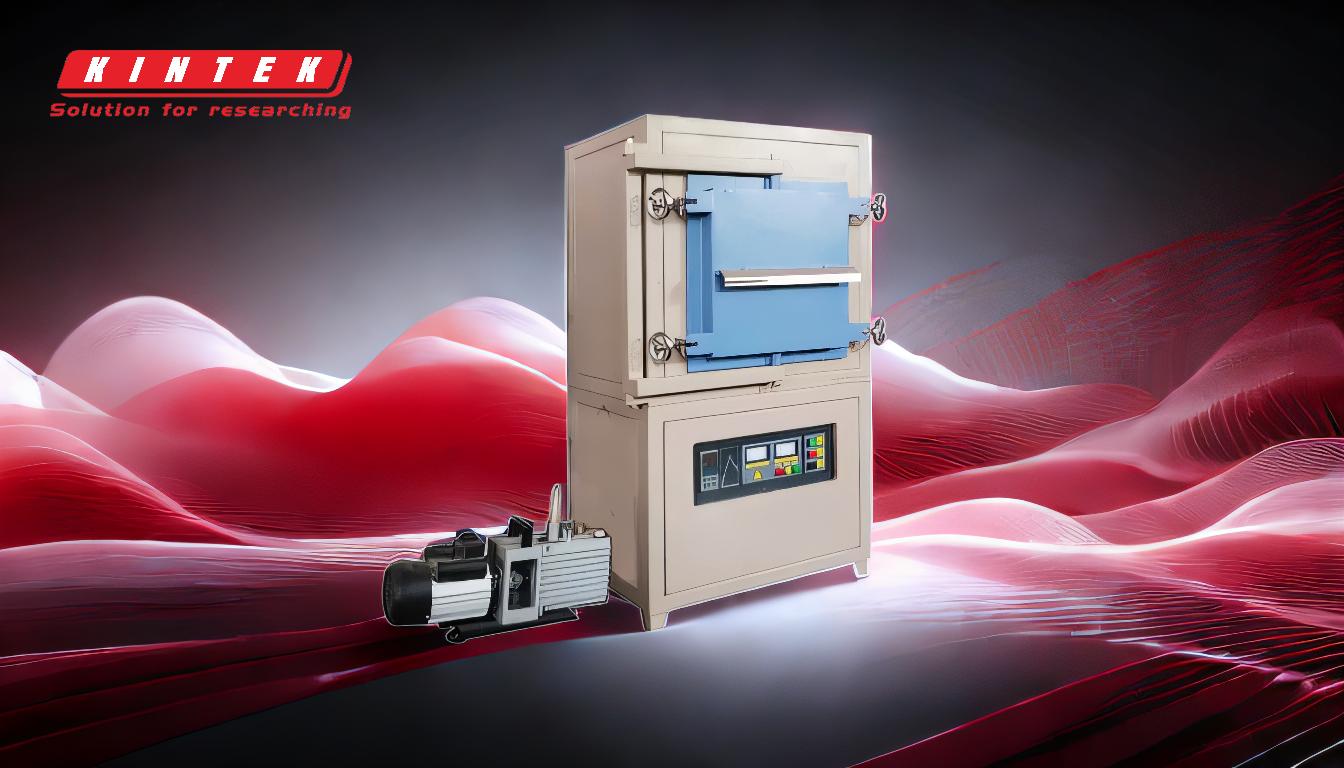
-
Purpose of an Inert Atmosphere:
- An inert atmosphere is used to prevent surface reactions such as oxidation, decarburization, or carburization during high-temperature processes.
- It ensures that materials like metals and ceramics retain their desired properties and surface finish.
-
Steps to Create an Inert Atmosphere:
-
Creating a Vacuum:
- A slight vacuum (up to 0.1MPa) is created inside the furnace using a rotary vane oil-filled vacuum pump.
- This step removes oxygen and other reactive gases, minimizing the risk of unwanted chemical reactions.
-
Purging with Inert Gas:
- After creating the vacuum, inert gases such as argon or nitrogen are introduced into the furnace.
- These gases are chemically inactive and create a protective environment around the material being treated.
-
Creating a Vacuum:
-
Choice of Inert Gases:
- Argon (Ar) and Nitrogen (N2) are the most commonly used inert gases due to their high natural abundance and non-reactive properties.
- For specific applications, hydrogen gas may also be used, but this requires additional safety measures due to its explosive nature.
-
Operational Considerations:
-
Temperature Limitations:
- Operating in an inert atmosphere may require higher-temperature furnace elements or a restriction on the maximum operating temperature to accommodate the limitations of the heating elements.
-
Safety Measures:
- When using gases like hydrogen, explosion-proof safety provisions must be implemented to ensure safe operation.
-
Temperature Limitations:
-
Applications of Inert Atmospheres:
-
Metal Heat Treatment:
- Inert atmospheres are critical for processes like hardening high-carbon steel, where maintaining a neutral surface is essential to prevent decarburization or carburization.
-
Ceramic Processing:
- Inert atmospheres prevent oxidation and other chemical reactions that could degrade the quality of ceramic materials during firing.
-
Metal Heat Treatment:
-
Maintenance of the Inert Atmosphere:
- The inert atmosphere is maintained by continuously monitoring and controlling the gas flow to ensure a stable environment.
- Regular checks for leaks and proper sealing of the furnace are necessary to prevent the ingress of reactive gases.
By following these steps and considerations, an inert atmosphere can be effectively created and maintained in a furnace, ensuring optimal results for high-temperature processes.
Summary Table:
Key Aspect | Details |
---|---|
Purpose | Prevent oxidation, decarburization, and carburization during heat treatment. |
Steps | 1. Create a vacuum to remove reactive gases. 2. Purge with inert gas (argon/nitrogen). |
Common Inert Gases | Argon (Ar), Nitrogen (N2), or Hydrogen (H2) with safety measures. |
Applications | Metal heat treatment, ceramic processing, and more. |
Maintenance | Monitor gas flow, check for leaks, and ensure proper sealing. |
Need help creating an inert atmosphere for your furnace? Contact our experts today for tailored solutions!