Diamond-like carbon (DLC) is highly resistant to scratches due to its unique properties, such as high hardness, low coefficient of friction, and excellent wear resistance. These characteristics make DLC an ideal material for protective coatings in various applications. However, while DLC is highly scratch-resistant, it is not entirely scratch-proof. Its performance depends on factors such as the deposition method, bonding structure (Sp3 and Sp2 ratios), substrate material, and environmental conditions. DLC's scratch resistance is superior to many other materials, but it can still be damaged under extreme conditions or when exposed to harder materials.
Key Points Explained:
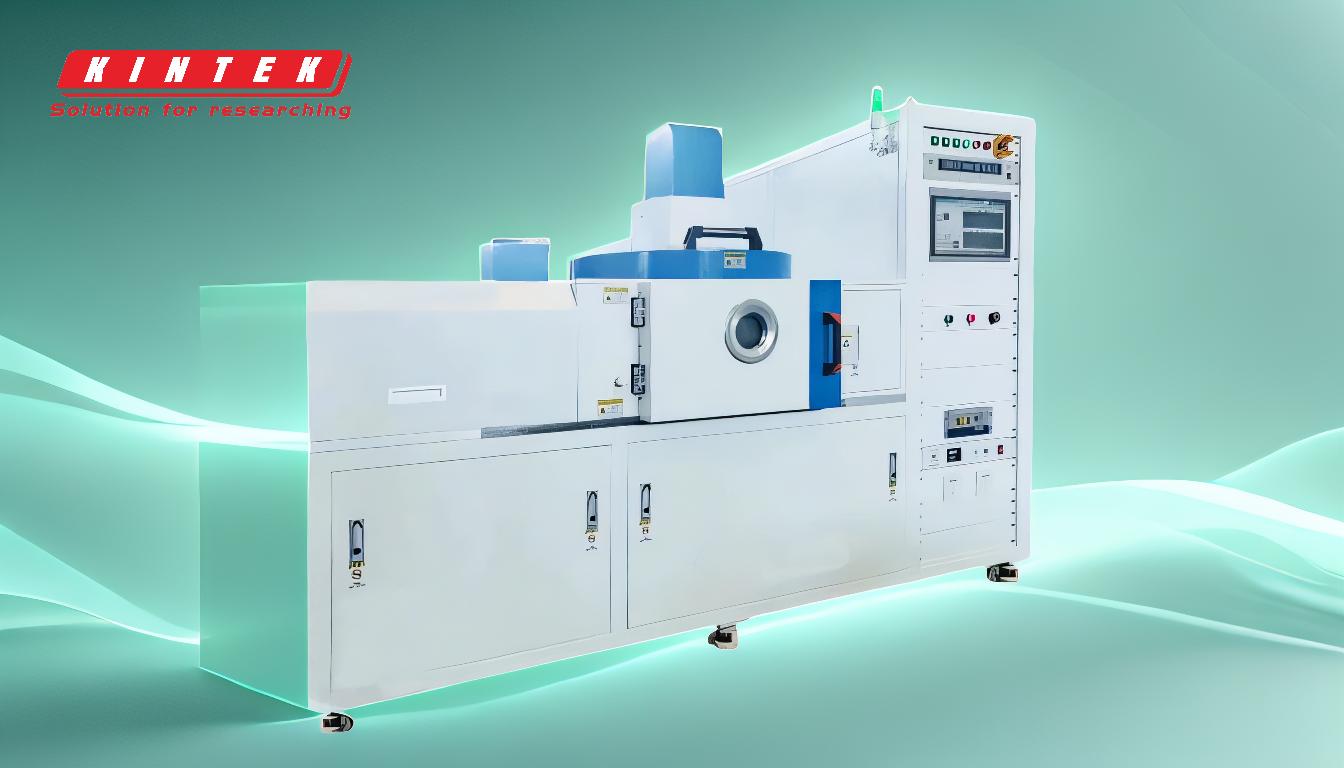
-
High Hardness of DLC:
- DLC coatings are characterized by their high hardness, which is a critical factor in scratch resistance. The hardness of DLC is due to the presence of Sp3 (diamond-like) bonds, which mimic the properties of diamond, one of the hardest known materials.
- This hardness makes DLC highly resistant to abrasion and wear, reducing the likelihood of scratches under normal conditions.
-
Low Coefficient of Friction:
- DLC coatings have a low coefficient of friction, which minimizes the risk of surface damage caused by sliding or rubbing against other materials.
- This property is particularly beneficial in applications where surfaces are subject to frequent contact, such as in automotive components or cutting tools.
-
Wear and Chemical Resistance:
- DLC films exhibit excellent wear resistance, making them suitable for use in harsh environments where mechanical wear is a concern.
- Additionally, DLC's chemical inertness ensures that it remains unaffected by many corrosive substances, further enhancing its durability and scratch resistance.
-
Adhesion and Deposition Techniques:
- The adhesion of DLC coatings to substrates is crucial for their performance. Techniques such as PACVD (Plasma-Assisted Chemical Vapor Deposition) are used to ensure strong bonding, which enhances the coating's scratch resistance.
- The use of bonding layers, such as silicon-based films, further improves adhesion, particularly on steel and hard metal substrates.
-
Amorphous Structure and Bonding:
- DLC is an amorphous material, meaning it lacks a crystalline structure. This amorphous nature, combined with the presence of both Sp3 (diamond-like) and Sp2 (graphite-like) bonds, contributes to its unique properties.
- The ratio of Sp3 to Sp2 bonds can be adjusted during deposition to tailor the coating's hardness, elasticity, and scratch resistance for specific applications.
-
Limitations of Scratch Resistance:
- While DLC is highly scratch-resistant, it is not entirely scratch-proof. Its performance can be compromised under extreme conditions, such as exposure to materials harder than diamond or under excessive mechanical stress.
- The scratch resistance of DLC also depends on the substrate material and the quality of the deposition process. Poor adhesion or improper deposition can reduce the coating's effectiveness.
-
Applications of DLC Coatings:
- DLC coatings are widely used in industries where scratch resistance and durability are critical. Common applications include:
- Automotive components (e.g., pistons, gears, and bearings)
- Cutting tools and machining equipment
- Medical devices and implants (due to biocompatibility)
- Optical and electronic components (for antireflective and protective properties)
- DLC coatings are widely used in industries where scratch resistance and durability are critical. Common applications include:
-
Environmental and Operational Factors:
- The scratch resistance of DLC coatings can be influenced by environmental factors such as temperature, humidity, and exposure to chemicals.
- Operational factors, including the load, speed, and type of contact (sliding, rolling, or impact), also play a role in determining the coating's performance.
-
Comparison with Other Materials:
- Compared to other protective coatings, such as titanium nitride (TiN) or chromium nitride (CrN), DLC offers superior scratch resistance due to its higher hardness and lower friction.
- However, DLC may not be suitable for all applications, particularly those requiring extreme toughness or resistance to high-temperature degradation.
In summary, while DLC is not entirely scratch-proof, its high hardness, low friction, and excellent wear resistance make it one of the most scratch-resistant materials available. Its performance can be optimized through proper deposition techniques and substrate preparation, making it a valuable choice for a wide range of protective applications.
Summary Table:
Property | Description |
---|---|
High Hardness | Sp3 bonds mimic diamond, providing exceptional abrasion and wear resistance. |
Low Friction | Minimizes surface damage from sliding or rubbing, ideal for frequent contact. |
Wear & Chemical Resistance | Resists mechanical wear and corrosive substances, enhancing durability. |
Adhesion & Deposition | Techniques like PACVD ensure strong bonding, improving scratch resistance. |
Amorphous Structure | Adjustable Sp3/Sp2 bond ratios tailor hardness and elasticity for specific uses. |
Limitations | Not entirely scratch-proof; performance varies with substrate and conditions. |
Applications | Automotive, cutting tools, medical devices, and optical components. |
Discover how DLC coatings can protect your applications—contact us today for expert advice!