PVD (Physical Vapor Deposition) coatings are generally considered hypoallergenic due to their strong adhesion to substrates, chemical inertness, and resistance to corrosion and oxidation. These properties make PVD coatings safe for use in applications where direct skin contact is likely, such as jewelry, watches, and cutlery. The coatings are firmly bonded to the substrate, preventing particles from becoming airborne or causing irritation. Additionally, PVD coatings are widely used in industries requiring high durability and biocompatibility, further supporting their hypoallergenic nature. However, the specific material of the substrate and the type of PVD coating used can influence its hypoallergenic properties.
Key Points Explained:
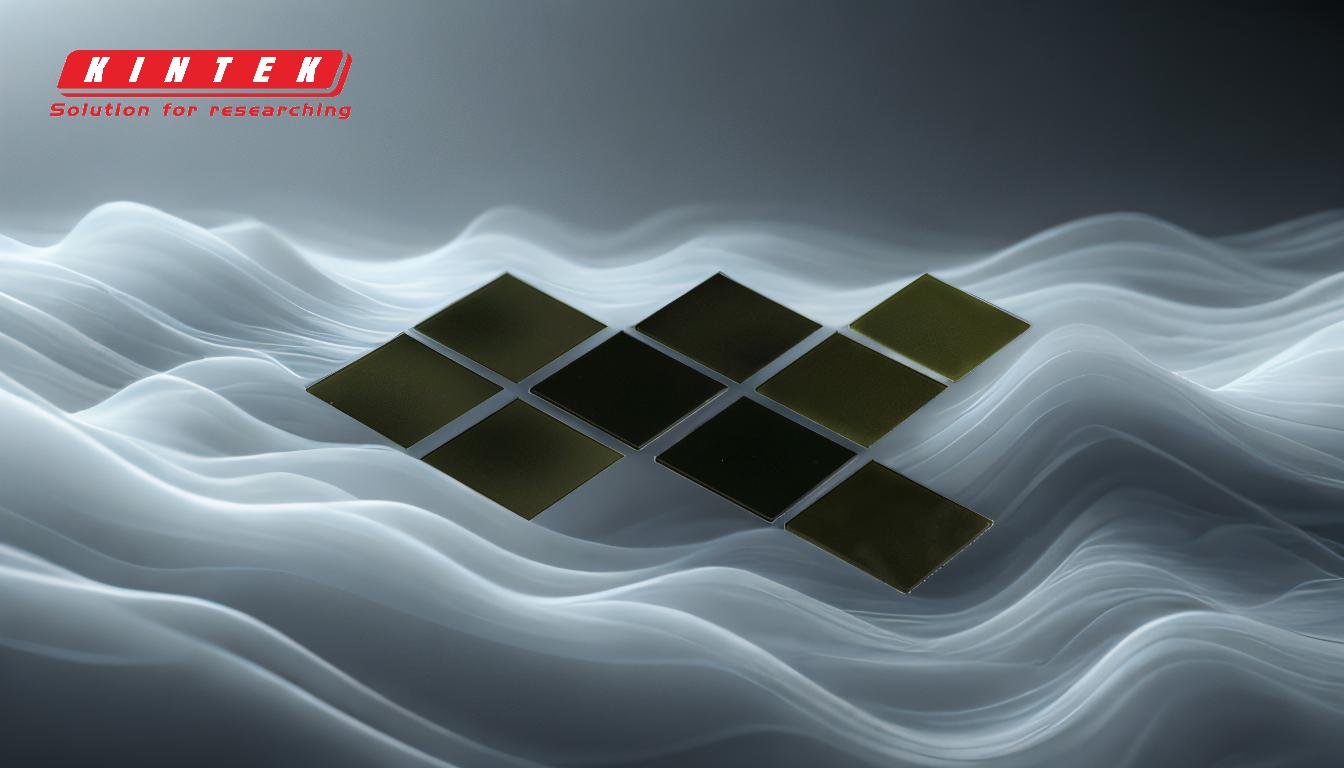
-
Strong Adhesion and Chemical Inertness:
- PVD coatings adhere strongly to their substrate, creating a durable and stable layer.
- The coatings are chemically inert, meaning they do not react with other substances, which reduces the likelihood of causing allergic reactions.
- This makes PVD coatings suitable for applications where they come into direct contact with skin, such as jewelry and watches.
-
Resistance to Corrosion and Oxidation:
- PVD coatings are highly resistant to corrosion and oxidation, ensuring that the coated material remains stable over time.
- This resistance prevents the breakdown of the coating, which could otherwise release particles or substances that might cause irritation or allergic reactions.
-
Biocompatibility:
- Many PVD coatings, such as those made from titanium nitride (TiN), are biocompatible, meaning they are safe for use in medical and food-related applications.
- Biocompatibility is a key factor in determining whether a material is hypoallergenic, as it indicates that the material is unlikely to cause adverse reactions when in contact with human tissue.
-
Thin and Durable Layers:
- PVD coatings are very thin, ranging from 0.5 to 5 microns, and are difficult to remove once applied.
- The thinness and durability of the coating ensure that it remains intact and does not flake or peel, which could otherwise expose the underlying material and potentially cause allergic reactions.
-
Safety After Application:
- Once applied, PVD coatings are safe as the particles are firmly bonded together and will not become airborne.
- This eliminates the risk of inhalation or skin irritation from loose particles, further supporting the hypoallergenic nature of PVD coatings.
-
Consideration of Substrate Material:
- The hypoallergenic properties of PVD coatings can be influenced by the underlying substrate material.
- For example, if the substrate material itself is allergenic (e.g., nickel), the PVD coating may not completely prevent allergic reactions, especially if the coating is damaged or worn.
-
Wide Range of Applications:
- PVD coatings are used in a variety of industries, including jewelry, cutlery, and medical devices, where hypoallergenic properties are essential.
- Their widespread use in these industries is a testament to their safety and hypoallergenic nature.
In summary, PVD coatings are generally considered hypoallergenic due to their strong adhesion, chemical inertness, resistance to corrosion, and biocompatibility. However, the specific properties of the substrate material and the type of PVD coating used should be considered to ensure complete hypoallergenic safety.
Summary Table:
Property | Description |
---|---|
Strong Adhesion | Firmly bonds to substrates, preventing particle release. |
Chemical Inertness | Does not react with other substances, reducing allergic reactions. |
Corrosion & Oxidation Resistance | Ensures long-term stability, preventing breakdown and irritation. |
Biocompatibility | Safe for medical, food, and skin-contact applications. |
Thin & Durable Layers | Ranges from 0.5 to 5 microns, resistant to flaking or peeling. |
Substrate Material Influence | Underlying material (e.g., nickel) may affect hypoallergenic properties. |
Applications | Widely used in jewelry, watches, cutlery, and medical devices. |
Interested in hypoallergenic PVD coatings for your products? Contact us today to learn more!