PVD (Physical Vapor Deposition) coatings on cutlery are generally considered safe for use once applied. The process involves depositing thin layers of material onto the surface of the cutlery, which are firmly bonded and do not pose a risk of becoming airborne or contaminating food. Most PVD coatings are chemically and biologically inert, making them suitable for food contact applications. However, during the application process, precautions must be taken to avoid inhaling particles, as they can be harmful. Overall, PVD coatings are widely used in the cutlery industry for their durability, wear resistance, and safety.
Key Points Explained:
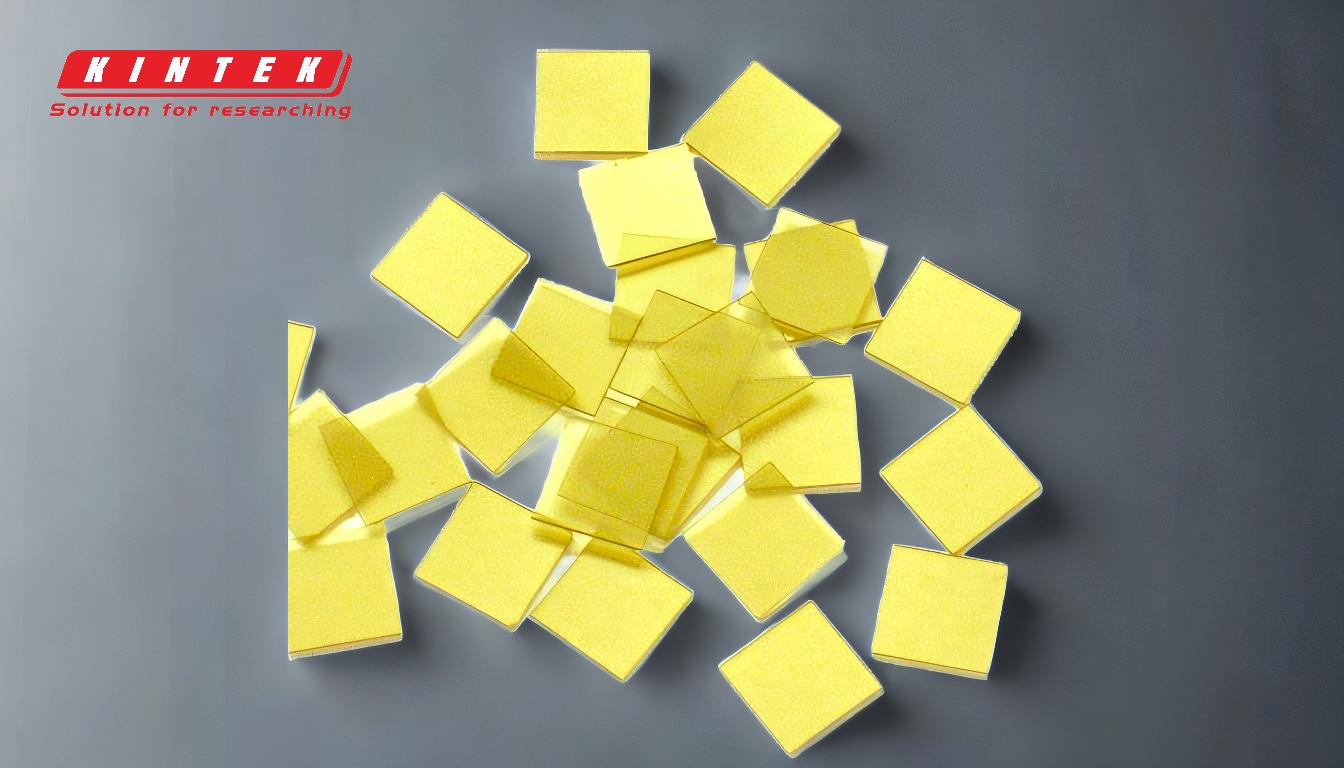
-
Safety of PVD Coatings Once Applied
- Once PVD coatings are applied to cutlery, they are firmly bonded to the substrate and do not pose a risk of becoming airborne or contaminating food.
- The thin layers of PVD coatings are chemically and biologically inert, making them safe for food contact.
- This inert nature ensures that the coatings do not react with food or release harmful substances during use.
-
Safety During the Application Process
- During the PVD coating process, particles can become airborne, which may be harmful if inhaled.
- Proper safety measures, such as ventilation and protective equipment, are essential to prevent exposure to these particles.
- Once the coating is applied and cured, the risk of inhalation or exposure is eliminated.
-
Comparison to Traditional Coating Processes
- PVD coatings are safer and more environmentally friendly compared to traditional metal coating processes like electroplating and electroless plating.
- Traditional processes often produce harmful waste products, whereas PVD uses only the substrate and target material, reducing environmental impact.
- This makes PVD a preferred choice for industries requiring safe and sustainable coating solutions.
-
Food Safety and Applications in Cutlery
- Most PVD coatings are certified as food-safe, adhering to strict industry standards.
- They are widely used in the cutlery industry for both decorative and functional purposes, such as enhancing wear resistance and durability.
- Commercial kitchen equipment and utensils often utilize PVD coatings due to their ability to withstand frequent use and cleaning.
-
Factors Affecting PVD Coating Quality
- Line-of-sight transfer: PVD coatings require direct line-of-sight application, meaning complex shapes or holes may not be uniformly coated.
- Surface pretreatment: Proper cleaning and preparation of the cutlery surface are crucial to ensure strong adhesion and uniform coating.
- Surface cleanliness: Even small particles or contaminants can affect the quality of the coating, emphasizing the need for meticulous surface preparation.
- Trapped air: Tightly sealed tapped holes should be avoided to prevent air from affecting the coating process.
-
Durability and Functional Benefits
- PVD coatings are highly wear-resistant, making them ideal for cutlery that undergoes frequent use and cleaning.
- They enhance the longevity of cutlery by providing a protective layer that resists scratches, corrosion, and tarnishing.
- These functional benefits, combined with their safety, make PVD coatings a popular choice for both household and commercial cutlery.
In conclusion, PVD coatings on cutlery are safe for use once applied, provided proper precautions are taken during the application process. Their inert nature, durability, and compliance with food safety standards make them a reliable choice for enhancing the performance and longevity of cutlery.
Summary Table:
Key Aspect | Details |
---|---|
Safety Once Applied | Firmly bonded, inert, and safe for food contact. No risk of contamination. |
Application Safety | Requires precautions during application to avoid inhaling harmful particles. |
Eco-Friendliness | Safer and more sustainable than traditional coating processes like plating. |
Food Safety Certification | Most PVD coatings are certified as food-safe and meet industry standards. |
Durability | Highly wear-resistant, scratch-resistant, and long-lasting. |
Functional Benefits | Enhances cutlery longevity and performance in both household and commercial use. |
Upgrade your cutlery with safe and durable PVD coatings—contact us today to learn more!