Sputtering generally offers better purity and film quality compared to evaporation due to its ability to produce denser, more uniform, and higher-adhesion films. While evaporation is simpler, faster, and more cost-effective, sputtering's advantages in film quality, adhesion, and lower-temperature crystalline film formation make it superior for applications requiring high purity and performance. The choice between the two depends on the specific requirements of the project, such as budget, production volume, and desired film properties.
Key Points Explained:
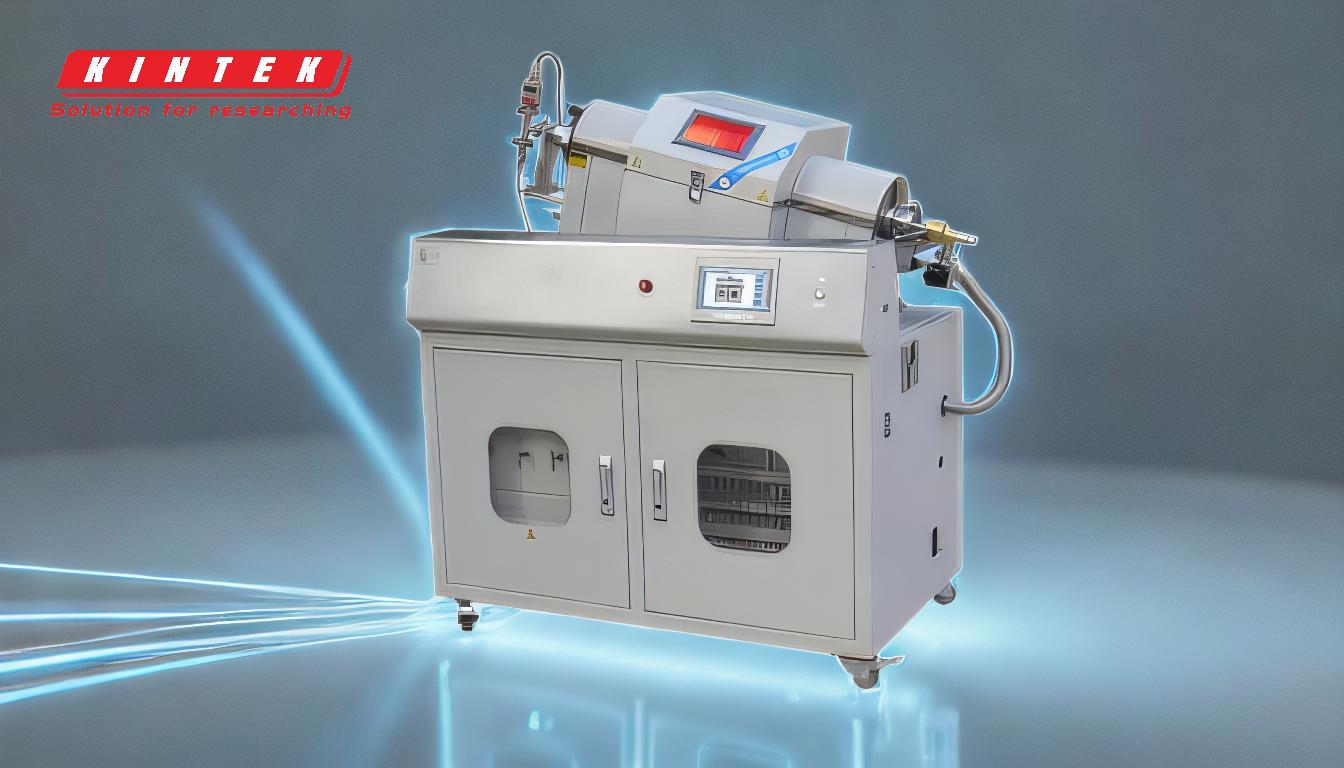
-
Mechanism of Film Formation:
- Sputtering: Involves energetic ions colliding with a target material, dislodging atoms that then deposit onto a substrate. This process results in high-energy particles that form dense, uniform films.
- Evaporation: Relies on heating the source material until it vaporizes, with the vapor condensing onto the substrate. This method is simpler but often results in less dense and less uniform films.
-
Film Purity and Quality:
- Sputtering: Produces films with higher purity due to the controlled environment and high-energy deposition process. The films are denser, more uniform, and have better adhesion to the substrate.
- Evaporation: While it can produce high-purity films, the process is more prone to contamination due to the higher vacuum levels required and the nature of the vaporization process.
-
Adhesion and Film Density:
- Sputtering: Offers significantly better adhesion (10 times or more) compared to evaporation. The high-energy sputtered particles create a hard and dense film surface, which is ideal for applications requiring strong film-substrate bonds.
- Evaporation: Films tend to have lower adhesion and density, which can be a limitation in applications where durability and mechanical properties are critical.
-
Deposition Rate and Complexity:
- Sputtering: Generally has a lower deposition rate compared to evaporation, except for pure metals. The process is more complex and costly, requiring precise control of parameters.
- Evaporation: Offers higher deposition rates, making it suitable for high-volume production. It is less complex and more cost-effective, which can be advantageous for large-scale or less demanding applications.
-
Temperature and Crystalline Structure:
- Sputtering: Allows for the formation of crystalline films at lower substrate temperatures, which is beneficial for temperature-sensitive materials.
- Evaporation: Typically requires higher temperatures to achieve similar crystalline structures, which can be a limitation for certain substrates or materials.
-
Film Homogeneity and Grain Size:
- Sputtering: Produces films with more uniform homogeneity and smaller grain sizes, contributing to better overall film quality and performance.
- Evaporation: Films tend to have less homogeneity and larger grain sizes, which can affect the mechanical and optical properties of the film.
In summary, sputtering is generally superior to evaporation in terms of film purity, quality, adhesion, and density. However, the choice between the two methods depends on the specific requirements of the application, including factors such as production volume, budget, and desired film properties. For applications requiring high purity and performance, sputtering is often the preferred method despite its higher cost and complexity.
Summary Table:
Aspect | Sputtering | Evaporation |
---|---|---|
Mechanism | Energetic ions dislodge target atoms, forming dense, uniform films. | Heating source material to vaporize, condensing onto substrate. |
Film Purity | Higher purity due to controlled environment and high-energy deposition. | Prone to contamination; requires higher vacuum levels. |
Adhesion | 10x better adhesion; creates hard, dense films. | Lower adhesion; less durable films. |
Deposition Rate | Lower rate (except for pure metals); complex process. | Higher rate; simpler and more cost-effective. |
Temperature | Forms crystalline films at lower substrate temperatures. | Requires higher temperatures for crystalline structures. |
Film Homogeneity | More uniform homogeneity; smaller grain sizes. | Less homogeneous; larger grain sizes. |
Need help choosing the right deposition method for your project? Contact our experts today!