Sputtering is indeed a form of physical vapor deposition (PVD). It is a process where atoms are ejected from the surface of a material (the target) when it is bombarded by high-energy particles, typically in a vacuum environment. These ejected atoms then condense onto a substrate, forming a thin film. Sputtering is a purely physical process, relying on the transfer of material from the target to the substrate through mechanical means, without involving chemical reactions. This method is widely used in various industries for coating materials, thanks to its ability to produce high-quality, uniform thin films.
Key Points Explained:
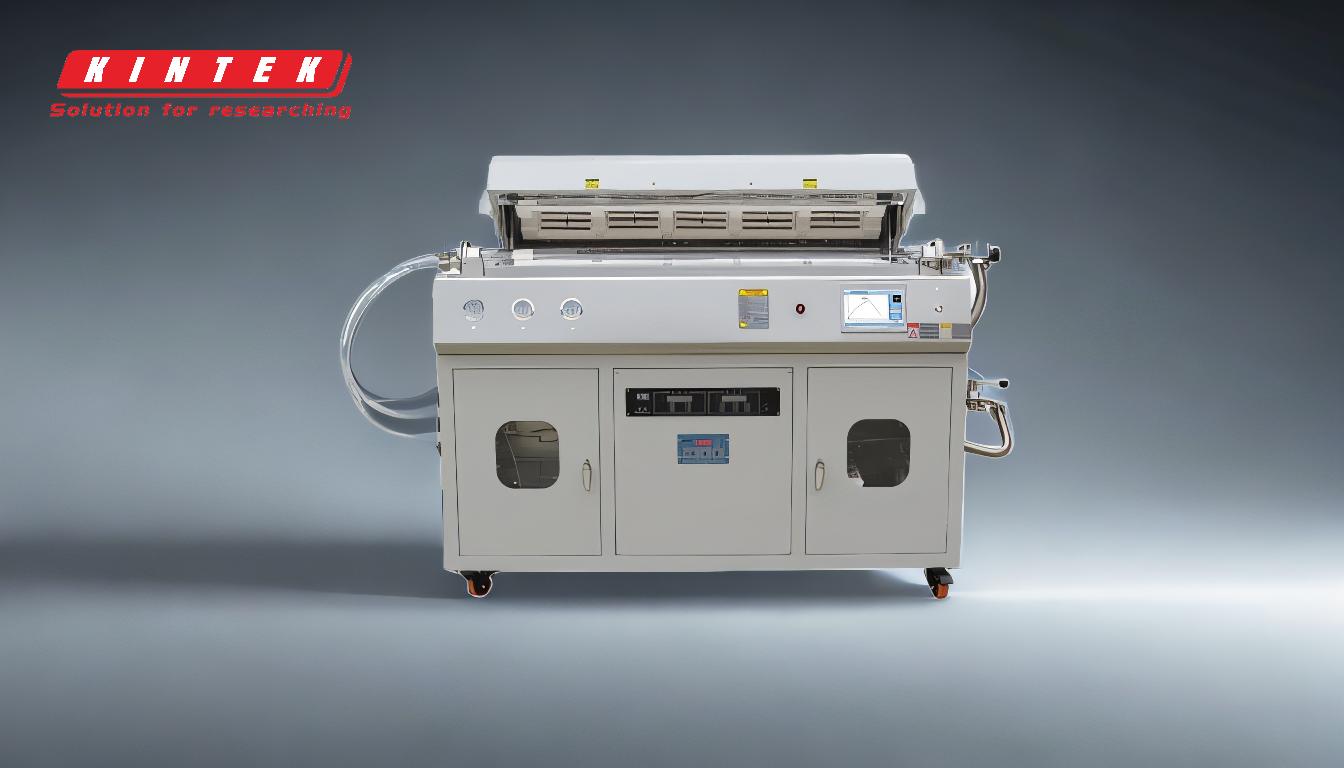
-
Definition of Sputtering:
- Sputtering is a process where atoms are ejected from the surface of a material when it is struck by high-energy particles. This ejection occurs in a vacuum or low-pressure environment, ensuring that the ejected atoms can travel freely and deposit onto a substrate.
-
Physical Vapor Deposition (PVD):
- PVD is a category of thin-film deposition techniques that involve the physical transfer of material from a source (target) to a substrate. Sputtering is one of the primary methods within this category, alongside evaporation and other techniques.
-
Mechanism of Sputtering:
- In sputtering, a target material is bombarded with high-energy particles, usually ions of an inert gas like argon. The impact of these ions causes atoms from the target to be ejected. These atoms then travel through the vacuum and deposit onto the substrate, forming a thin film.
-
Types of Sputtering:
- There are several types of sputtering techniques, including direct current (DC) sputtering and radio frequency (RF) sputtering. Each type has its specific applications and advantages, depending on the materials involved and the desired properties of the thin film.
-
Role of the Sputtering Target:
- The sputtering target is a crucial component in the PVD process. It is the material that is eroded by the high-energy particles, and its composition directly influences the properties of the thin film deposited on the substrate. Targets can be made from a variety of materials, including metals, alloys, and ceramics.
-
Advantages of Sputtering in PVD:
- Sputtering offers several advantages, including the ability to deposit a wide range of materials, excellent film uniformity, and the capability to produce films with precise thickness control. It is also a versatile process that can be used for both conductive and non-conductive materials.
-
Applications of Sputtering:
- Sputtering is widely used in various industries, including semiconductor manufacturing, optical coatings, and decorative coatings. It is also employed in the production of hard coatings for tools and components, as well as in the creation of thin-film solar cells.
In summary, sputtering is a key technique within the broader category of physical vapor deposition. It is a purely physical process that involves the ejection of atoms from a target material and their subsequent deposition onto a substrate to form a thin film. This method is highly versatile and is used in a wide range of applications due to its ability to produce high-quality, uniform coatings.
Summary Table:
Aspect | Details |
---|---|
Definition | Atoms ejected from a target by high-energy particles in a vacuum. |
PVD Category | Physical vapor deposition (PVD) technique. |
Mechanism | Bombardment of target material with ions (e.g., argon) to eject atoms. |
Types | DC sputtering, RF sputtering, and more. |
Target Role | Material eroded to form thin films; made of metals, alloys, or ceramics. |
Advantages | Uniform films, precise thickness control, versatile material compatibility. |
Applications | Semiconductors, optical coatings, solar cells, and hard coatings. |
Interested in learning more about sputtering and PVD? Contact our experts today for tailored solutions!