Brazing is a widely used joining process that involves melting a filler metal to bond two or more base metals without melting the base materials themselves. The choice of brazing filler metal is critical, as it determines the strength, durability, and compatibility of the joint. Commonly used brazing metals include silver-copper, copper-zinc, copper-phosphorous, palladium, and nickel. These materials are selected based on their melting points, mechanical properties, and compatibility with the base metals being joined. Brazing is utilized in various industries, including aerospace, medical devices, HVAC, and structural engineering, due to its ability to create strong, leak-proof, and corrosion-resistant joints.
Key Points Explained:
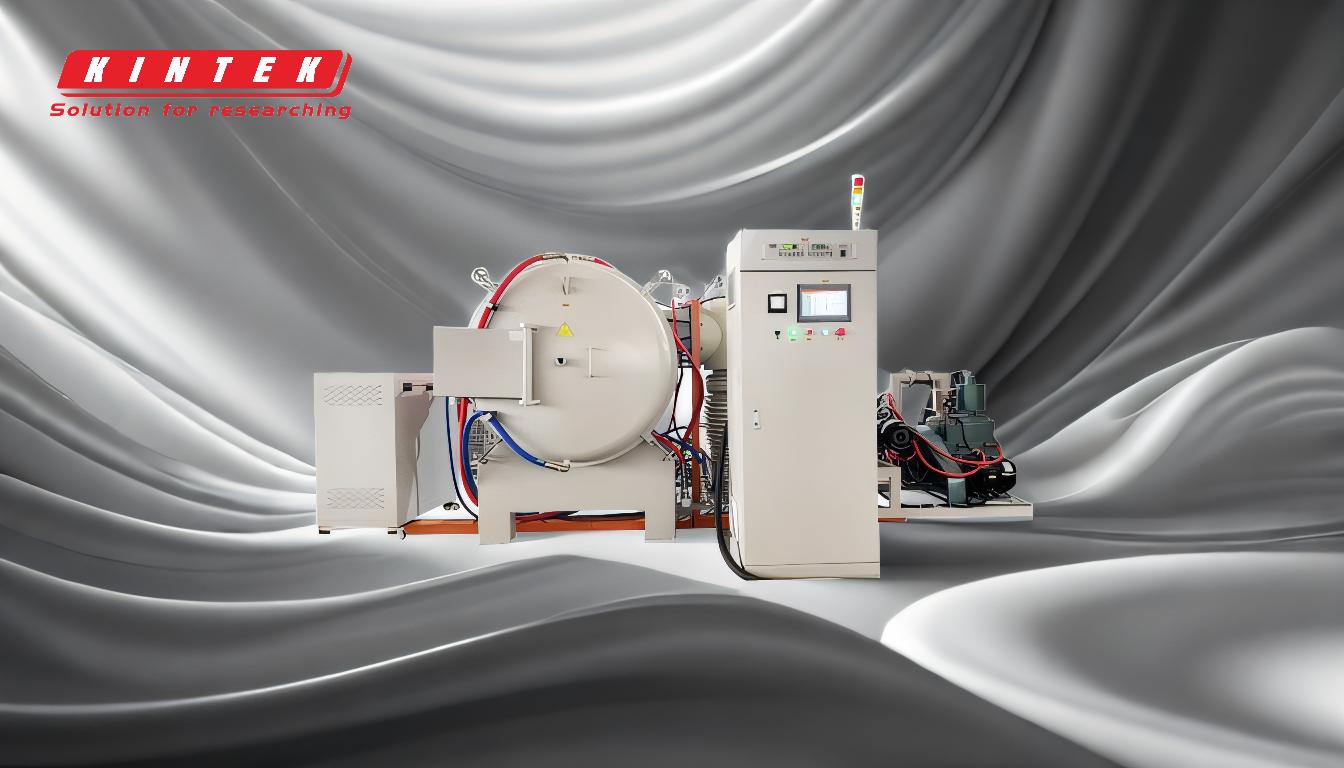
-
Common Brazing Filler Metals:
- Silver-Copper: This alloy is widely used due to its excellent flow characteristics, high strength, and compatibility with a variety of base metals, including stainless steel, copper, and nickel alloys. It is often used in applications requiring high joint integrity, such as in HVAC systems and medical devices.
- Copper-Zinc: Known for its affordability and good strength, copper-zinc alloys are commonly used for brazing steel and cast iron. They are suitable for applications where cost is a significant factor, such as in structural components.
- Copper-Phosphorous: This self-fluxing alloy is ideal for brazing copper and copper alloys. It eliminates the need for additional flux, making it cost-effective and efficient for plumbing and electrical applications.
- Palladium: Palladium-based alloys are used in high-temperature and high-strength applications, such as aerospace components. They offer excellent corrosion resistance and are compatible with a wide range of base metals.
- Nickel: Nickel-based filler metals are used in high-temperature and corrosive environments, such as in gas turbines and chemical processing equipment. They provide exceptional strength and resistance to oxidation and thermal cycling.
-
Selection Criteria for Brazing Filler Metals:
- Melting Point: The filler metal must have a melting point lower than the base metals but high enough to ensure a strong joint. For example, silver-copper alloys melt at around 600–800°C, making them suitable for many industrial applications.
- Compatibility: The filler metal must wet and bond effectively with the base metals. For instance, copper-phosphorous alloys are specifically designed for copper-to-copper joints.
- Mechanical Properties: The joint must withstand the mechanical stresses of the application. Nickel-based alloys are chosen for their high strength in demanding environments.
- Corrosion Resistance: In applications like medical devices or marine environments, corrosion-resistant alloys like palladium or nickel are preferred.
-
Applications of Brazing:
- Heating and Cooling Assemblies: Brazing is used to join components in HVAC systems, such as heat exchangers and refrigeration units, due to its ability to create leak-proof joints.
- Aircraft Components: The aerospace industry relies on brazing for joining lightweight, high-strength materials like titanium and aluminum alloys.
- Medical Devices: Brazing is used to assemble surgical instruments and implants, where precision and biocompatibility are critical.
- Structural Components: In construction and automotive industries, brazing is used to join steel and cast iron components, providing strong and durable connections.
-
Advantages of Brazing:
- Strong Joints: Brazed joints are typically stronger than the filler metal itself, ensuring long-term reliability.
- Leak-Proof Seals: The capillary action of brazing creates tight, leak-proof seals, making it ideal for fluid and gas systems.
- Versatility: Brazing can join dissimilar metals, such as copper to stainless steel, which is challenging with other joining methods.
- Minimal Distortion: Since the base metals do not melt, brazing minimizes distortion and preserves the integrity of the components.
By understanding the properties and applications of commonly used brazing metals, purchasers can make informed decisions to ensure the success of their projects.
Summary Table:
Brazing Metal | Key Properties | Applications |
---|---|---|
Silver-Copper | High strength, excellent flow, compatible with stainless steel, copper, and nickel alloys | HVAC systems, medical devices |
Copper-Zinc | Affordable, good strength, suitable for steel and cast iron | Structural components |
Copper-Phosphorous | Self-fluxing, cost-effective, ideal for copper-to-copper joints | Plumbing, electrical applications |
Palladium | High-temperature resistance, corrosion-resistant, compatible with various base metals | Aerospace components |
Nickel | Exceptional strength, oxidation and thermal cycling resistance | Gas turbines, chemical processing equipment |
Need help selecting the right brazing metal for your project? Contact our experts today!