Aluminum alloy castings are widely used in various industries due to their lightweight, strength, and corrosion resistance. The three basic methods of aluminum alloy castings are sand casting, die casting, and permanent mold casting. Each method has its unique advantages, limitations, and applications, making them suitable for different production requirements. Sand casting is versatile and cost-effective for low to medium-volume production, die casting offers high precision and surface finish for mass production, and permanent mold casting provides a balance between quality and production efficiency. Understanding these methods helps in selecting the most appropriate casting process for specific applications.
Key Points Explained:
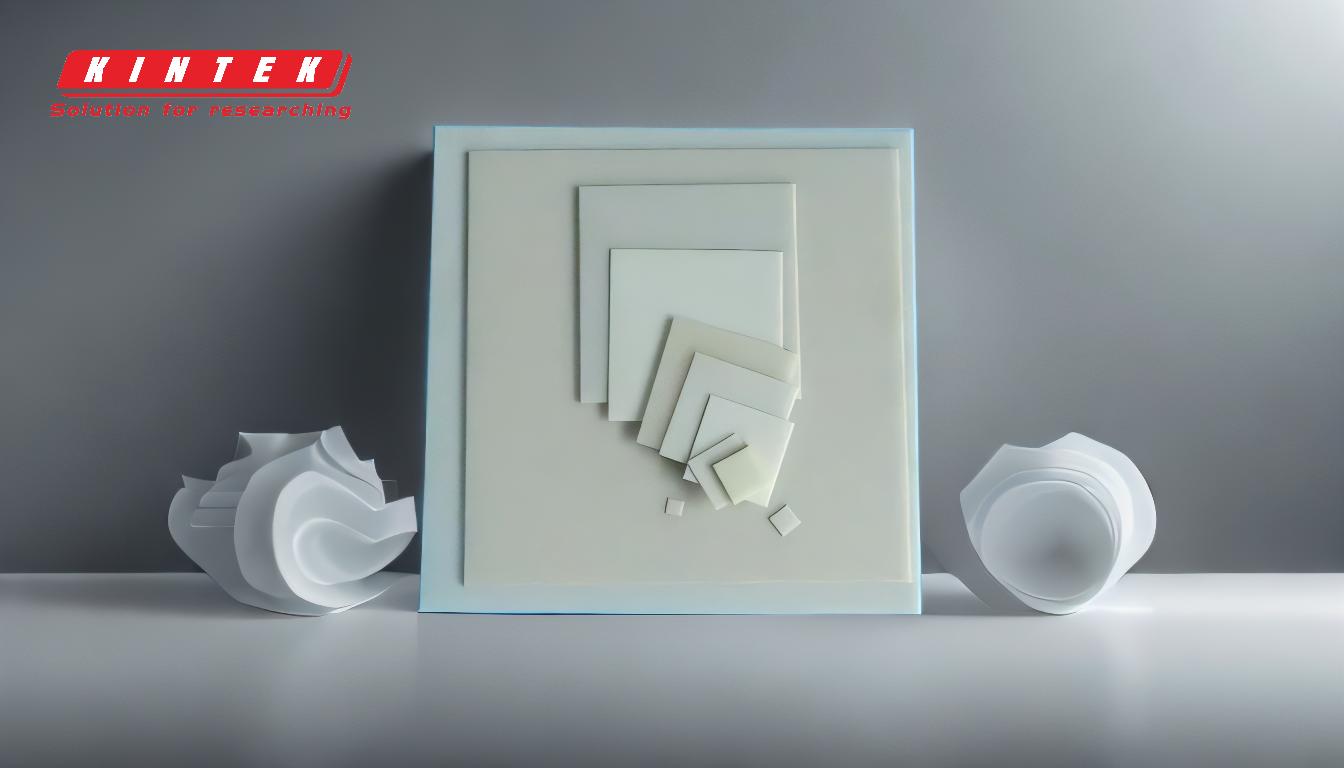
-
Sand Casting
- Process Overview: Sand casting involves creating a mold from a sand mixture, into which molten aluminum is poured. Once the metal solidifies, the mold is broken to retrieve the casting.
-
Advantages:
- Suitable for large and complex parts.
- Low tooling costs, making it ideal for low to medium-volume production.
- Can accommodate a wide range of alloys.
-
Limitations:
- Lower dimensional accuracy and surface finish compared to other methods.
- Longer production time due to mold preparation and cooling.
- Applications: Commonly used for engine blocks, pump housings, and other industrial components.
-
Die Casting
- Process Overview: Die casting uses reusable steel molds (dies) and high pressure to inject molten aluminum into the mold cavity. The process is highly automated and suited for high-volume production.
-
Advantages:
- High precision and excellent surface finish.
- Fast production cycles, making it cost-effective for mass production.
- Ability to produce thin-walled and intricate parts.
-
Limitations:
- High initial tooling costs.
- Limited to smaller parts due to machine size constraints.
- Applications: Widely used in automotive components, consumer electronics, and household appliances.
-
Permanent Mold Casting
- Process Overview: Permanent mold casting uses reusable metal molds, typically made of steel or cast iron, into which molten aluminum is poured. The molds are often coated with a refractory material to improve mold life and casting quality.
-
Advantages:
- Better dimensional accuracy and surface finish than sand casting.
- Faster production cycles compared to sand casting.
- Suitable for medium to high-volume production.
-
Limitations:
- Higher tooling costs than sand casting.
- Limited to simpler geometries compared to die casting.
- Applications: Commonly used for automotive parts, aerospace components, and industrial machinery.
By understanding these three basic methods, manufacturers can choose the most suitable casting process based on factors such as production volume, part complexity, and cost considerations. Each method offers distinct benefits, ensuring that aluminum alloy castings meet the specific requirements of various industries.
Summary Table:
Method | Advantages | Limitations | Applications |
---|---|---|---|
Sand Casting | - Suitable for large/complex parts - Low tooling costs - Wide alloy range |
- Lower dimensional accuracy - Longer production time |
Engine blocks, pump housings, industrial components |
Die Casting | - High precision - Fast production - Thin-walled/intricate parts |
- High initial tooling costs - Limited to smaller parts |
Automotive components, consumer electronics, household appliances |
Permanent Mold Casting | - Better accuracy than sand casting - Faster cycles - Medium-high volume |
- Higher tooling costs - Limited to simpler geometries |
Automotive parts, aerospace components, industrial machinery |
Need help choosing the right casting method for your project? Contact our experts today for personalized guidance!