Diffusion pumps are widely used in high-vacuum applications due to their ability to achieve extremely low pressures (10^-2 to 10^-10 torr) without any moving parts, making them durable and reliable. They are commonly employed in fields like electron-beam microscopy, vacuum deposition, and vacuum furnaces. However, they require oil or other working fluids, which can introduce contamination risks and necessitate regular maintenance. Additionally, diffusion pumps are not suitable for applications requiring clean, oil-free environments. Despite these drawbacks, their high vacuum capabilities and lack of moving parts make them a preferred choice for many industrial and scientific applications.
Key Points Explained:
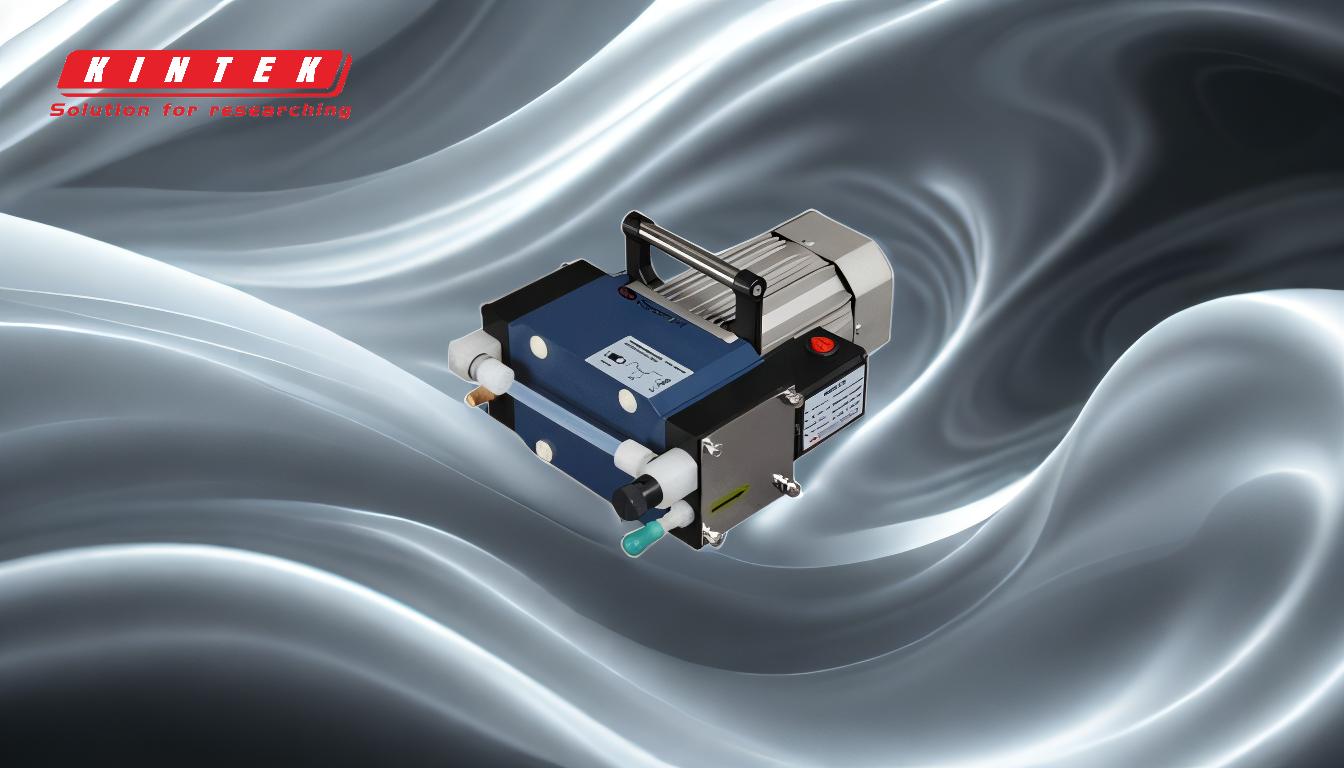
-
Advantages of Diffusion Pumps:
-
High Vacuum Capability:
- Diffusion pumps can achieve extremely low pressures, ranging from 10^-2 to 10^-10 torr, making them ideal for applications requiring high vacuum levels, such as electron-beam microscopy and vacuum deposition.
-
No Moving Parts:
- The absence of moving parts enhances their durability and reliability, reducing the likelihood of mechanical failure and minimizing maintenance requirements.
-
Versatility in Size and Application:
- Diffusion pumps are available in various sizes, allowing them to be tailored to specific industrial or scientific needs. They are widely used in vacuum furnaces, coatings, and other high-vacuum processes.
-
Cost-Effectiveness for High-Vacuum Applications:
- Compared to other high-vacuum pumps, diffusion pumps are often more cost-effective due to their simple design and long operational lifespan.
-
High Vacuum Capability:
-
Disadvantages of Diffusion Pumps:
-
Requirement for Working Fluids:
- Diffusion pumps rely on oil or other working fluids to create a vacuum. This can lead to contamination risks, especially in applications requiring clean, oil-free environments, such as semiconductor manufacturing or certain scientific experiments.
-
Maintenance and Operational Costs:
- While they have no moving parts, diffusion pumps still require regular maintenance, including the replacement of working fluids and cleaning to prevent contamination. This can increase operational costs over time.
-
Not Suitable for Low-Vacuum Applications:
- Diffusion pumps are optimized for high-vacuum environments and are less efficient or effective in low-vacuum applications. Other pump types, such as diaphragm or rotary pumps, may be more suitable for such scenarios.
-
Potential for Backstreaming:
- Backstreaming, where oil or fluid vapors migrate into the vacuum chamber, can occur if the pump is not properly maintained or operated. This can compromise the integrity of the vacuum process and contaminate the system.
-
Requirement for Working Fluids:
-
Comparison with Other Pump Types:
-
Diaphragm Pumps:
- Unlike diffusion pumps, diaphragm pumps are dry and do not require oil or working fluids, making them suitable for clean environments. However, they typically achieve lower vacuum levels and are more expensive.
-
Rotary Pumps:
- Rotary pumps are often used in conjunction with diffusion pumps to achieve high vacuum levels. While rotary pumps are more versatile for low to medium vacuum applications, they have moving parts and require more frequent maintenance.
-
Diaphragm Pumps:
-
Applications of Diffusion Pumps:
-
Electron-Beam Microscopy:
- Diffusion pumps are commonly used in electron-beam microscopy to create the high vacuum necessary for accurate imaging.
-
Vacuum Deposition and Coatings:
- They are essential in processes like physical vapor deposition (PVD) and chemical vapor deposition (CVD), where high vacuum levels are required to deposit thin films or coatings.
-
Vacuum Furnaces:
- Diffusion pumps are used in vacuum furnaces to achieve the low pressures needed for processes like annealing, brazing, and sintering.
-
Electron-Beam Microscopy:
-
Considerations for Purchasers:
-
Application Requirements:
- Buyers should evaluate whether their application requires the high vacuum levels that diffusion pumps provide or if a lower vacuum pump would suffice.
-
Contamination Sensitivity:
- For applications sensitive to contamination, such as semiconductor manufacturing, alternative pump types like diaphragm or turbomolecular pumps may be more appropriate.
-
Maintenance and Operational Costs:
- While diffusion pumps are cost-effective in terms of initial investment, purchasers should factor in the ongoing costs of working fluids and maintenance.
-
Application Requirements:
By understanding these advantages and disadvantages, purchasers can make informed decisions about whether diffusion pumps are the right choice for their specific needs.
Summary Table:
Aspect | Details |
---|---|
Advantages | |
High Vacuum Capability | Achieves pressures from 10^-2 to 10^-10 torr, ideal for high-vacuum needs. |
No Moving Parts | Durable, reliable, and low-maintenance due to no mechanical components. |
Versatility | Available in various sizes for tailored industrial or scientific use. |
Cost-Effective | Affordable for high-vacuum applications compared to other pump types. |
Disadvantages | |
Requires Working Fluids | Oil or fluids can cause contamination in clean environments. |
Maintenance Needs | Regular fluid replacement and cleaning increase operational costs. |
Not for Low-Vacuum | Less efficient in low-vacuum applications; other pumps may be better. |
Backstreaming Risk | Improper maintenance can lead to oil vapor contamination in the system. |
Applications | |
Electron-Beam Microscopy | Essential for creating high vacuum in imaging. |
Vacuum Deposition | Used in PVD and CVD processes for thin film coatings. |
Vacuum Furnaces | Enables low-pressure processes like annealing and sintering. |
Need help choosing the right diffusion pump for your application? Contact our experts today for personalized advice!