Moulding, particularly plastic injection moulding, offers several advantages such as high precision, repeatability, speed, and cost-effectiveness for large production runs. It also provides a wide range of material options, making it versatile for various applications. However, the process comes with disadvantages, including higher initial costs and longer lead times compared to other manufacturing methods. These factors make it important to carefully evaluate the specific needs of a project before choosing moulding as the preferred manufacturing process.
Key Points Explained:
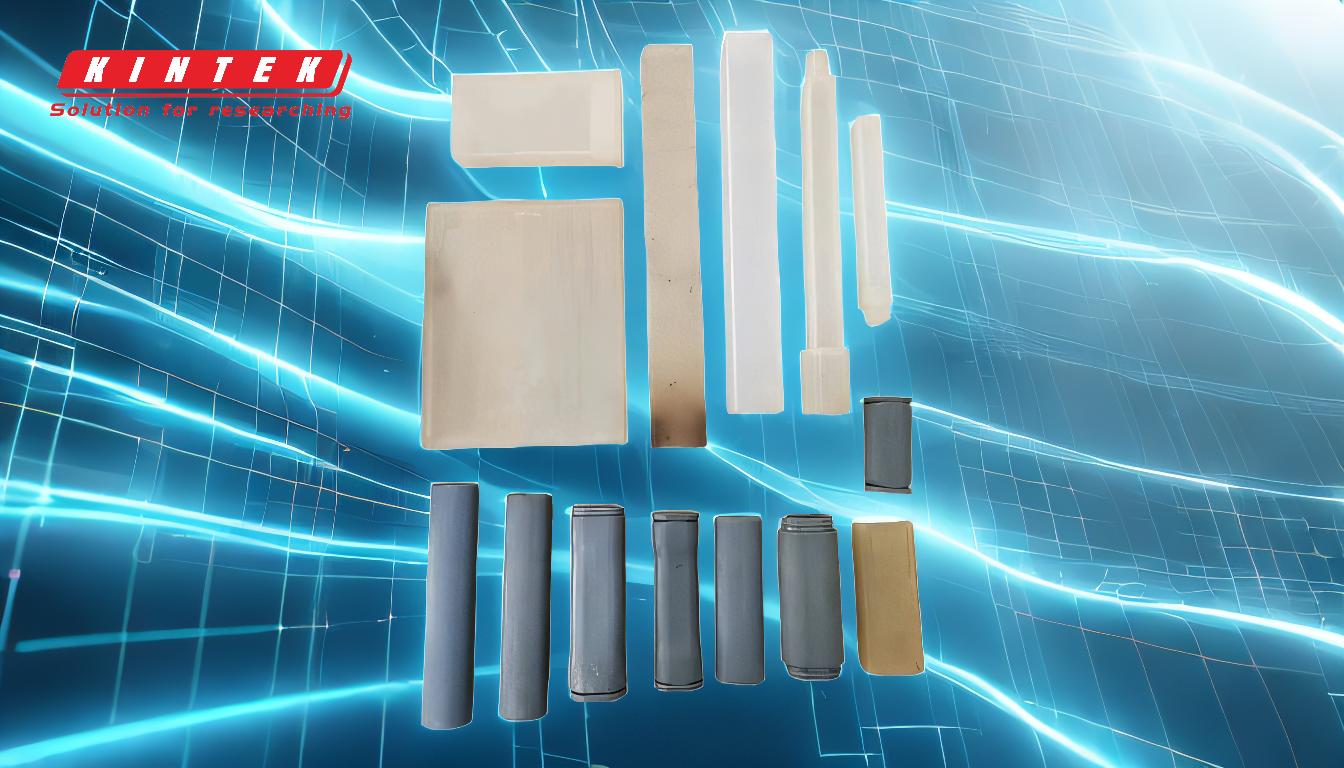
-
Advantages of Moulding:
- High Precision: Moulding allows for the production of parts with very tight tolerances, ensuring that each piece is consistent and meets exact specifications. This is particularly important in industries where precision is critical, such as automotive or medical device manufacturing.
- High Repeatability: The process is highly repeatable, meaning that once the mould is created, it can produce thousands or even millions of identical parts. This consistency is crucial for mass production.
- Speed: Moulding is a fast process, especially when compared to other manufacturing methods like machining or 3D printing. This speed makes it ideal for high-volume production runs.
- Low Cost per Part: While the initial setup costs can be high, the cost per part decreases significantly with large production runs. This makes moulding a cost-effective option for mass production.
- Wide Range of Materials: Moulding can be done with a vast array of plastics, each with different properties (e.g., strength, flexibility, heat resistance). This versatility allows manufacturers to choose the best material for their specific application.
-
Disadvantages of Moulding:
- Higher Initial Cost: The cost of creating the moulds can be quite high, especially for complex designs. This initial investment can be a barrier for small-scale production or for companies with limited budgets.
- Longer Lead Time: The process of designing and manufacturing the moulds can take a significant amount of time, which can delay the start of production. This is a disadvantage for projects with tight deadlines.
- Limited Flexibility for Design Changes: Once a mould is created, making changes to the design can be costly and time-consuming. This lack of flexibility can be a disadvantage if the design needs to be modified during the production process.
- Material Waste: Although moulding is efficient, there can still be some material waste, especially during the initial setup and testing phases. This waste can add to the overall cost and environmental impact of the process.
-
Considerations for Equipment and Consumable Purchasers:
- Volume of Production: For high-volume production, the advantages of moulding often outweigh the disadvantages. However, for low-volume or custom production, other methods might be more cost-effective.
- Material Selection: The wide range of available materials is a significant advantage, but it also requires careful consideration. Purchasers need to ensure that the chosen material meets the specific requirements of their application.
- Lead Time and Budget: The initial cost and lead time are important factors to consider, especially for projects with tight budgets or deadlines. Purchasers should evaluate whether the benefits of moulding justify these initial investments.
- Design Complexity: For complex designs, the precision and repeatability of moulding are significant advantages. However, the cost and time associated with creating complex moulds should be carefully weighed against the benefits.
In summary, moulding, particularly plastic injection moulding, offers numerous advantages such as precision, repeatability, speed, and cost-effectiveness for large production runs. However, it also has some disadvantages, including higher initial costs and longer lead times. Equipment and consumable purchasers should carefully evaluate their specific needs, including production volume, material requirements, budget, and design complexity, to determine whether moulding is the best option for their project.
Summary Table:
Aspect | Advantages | Disadvantages |
---|---|---|
Precision | Produces parts with tight tolerances, ideal for critical industries. | Higher initial costs for mould creation. |
Repeatability | Consistent production of identical parts, perfect for mass production. | Longer lead times for mould design and manufacturing. |
Speed | Faster than machining or 3D printing, ideal for high-volume production. | Limited flexibility for design changes after mould creation. |
Cost per Part | Low cost per part for large production runs, cost-effective for mass output. | Material waste during setup and testing phases. |
Material Versatility | Wide range of plastics available, suitable for diverse applications. | Requires careful evaluation of production volume, budget, and complexity. |
Need help deciding if moulding is right for your project? Contact our experts today for personalized advice!