Sputtering techniques are widely used in thin film deposition due to their unique advantages, such as high deposition rates, excellent film uniformity, and the ability to work with a broad range of materials, including high-melting-point substances. However, these techniques also come with challenges, including high system complexity, potential substrate heating, and higher operational costs. This analysis explores the key advantages and disadvantages of sputtering techniques, providing a comprehensive understanding of their applications and limitations.
Key Points Explained:
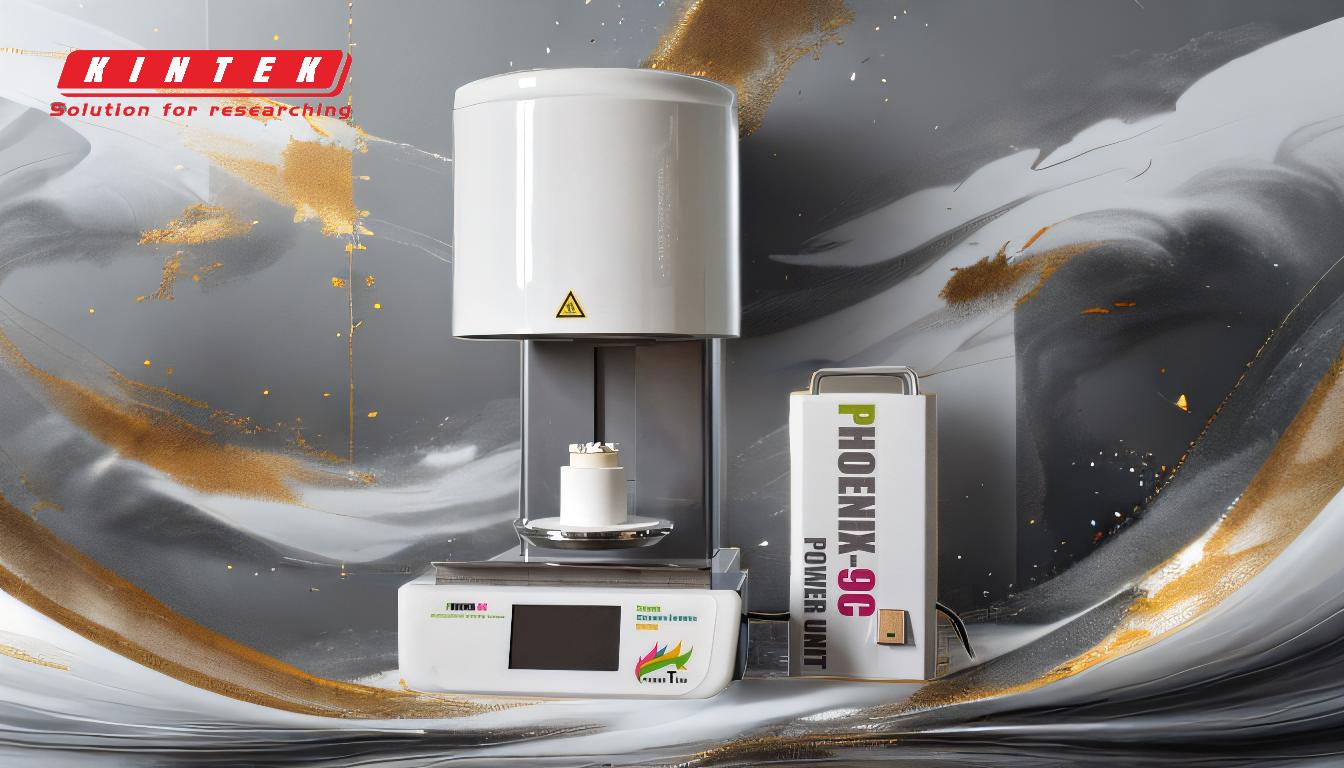
-
Advantages of Sputtering Techniques:
- High Deposition Rates and Throughput: Sputtering techniques, particularly ion beam sputtering (IBS), offer high deposition rates and throughput, making them efficient for large-scale production.
- Uniform and Dense Films: Sputtering produces films with excellent uniformity and high density, even at low temperatures, which is crucial for applications requiring precise film properties.
- Broad Material Compatibility: Sputtering is compatible with a wide range of materials, including metals, alloys, dielectrics, and even high-melting-point materials, which are challenging for other deposition methods.
- Molecular-Level Precision: The process allows for atomic-level control over film deposition, enabling the creation of pristine interfaces and the ability to tune film properties through precise parameter control.
- Better Adhesion: Sputtered atoms have higher kinetic energy compared to evaporated materials, resulting in stronger adhesion to the substrate.
- Reproducibility and Automation: Sputtering offers high reproducibility and simpler process automation compared to methods like thermal evaporation or E-Beam deposition.
- Environmental and Operational Benefits: Sputtering does not produce atmospheric pollution, has no heated parts, and can coat substrates in various orientations, including upside-down.
-
Disadvantages of Sputtering Techniques:
- High System Complexity and Cost: Sputtering systems are complex and expensive to set up and maintain, which can be a barrier for smaller operations.
- Substrate Heating: The energized vapor material in sputtering can cause substrate heating, which may be undesirable for temperature-sensitive materials.
- Chamber Coating and Surface Impurities: The process can lead to chamber coating and potential surface impurities, which may affect film quality and require additional cleaning steps.
- Poor Deposition Rates for Dielectrics: While sputtering works well with many materials, it has relatively poor deposition rates for dielectric materials, limiting its efficiency in certain applications.
- Operational Challenges: The process can be complicated, requiring precise control over parameters and careful handling to avoid contamination or defects.
-
Applications of Sputtering:
- Thin Film Deposition: Sputtering is widely used for depositing thin films ranging from nanometers to micrometers in thickness, suitable for applications in electronics, optics, and coatings.
- Surface Cleaning and Analysis: In surface physics, sputtering is used for cleaning high-purity surfaces and analyzing the chemical composition of materials.
- Alloy and Composite Film Creation: Sputtering allows for the deposition of alloys and composite materials in a single run, making it versatile for creating multi-layered structures.
-
Comparison with Other Deposition Methods:
- Versatility: Sputtering outperforms methods like thermal evaporation in terms of material compatibility and film quality, especially for high-melting-point materials.
- Precision and Control: The ability to achieve molecular-level precision and control over film properties makes sputtering a preferred choice for advanced applications.
- Cost and Complexity: While sputtering offers superior results, it is more complex and costly compared to simpler methods like thermal evaporation.
In summary, sputtering techniques offer significant advantages in terms of film quality, material compatibility, and precision, making them indispensable in many high-tech applications. However, the associated high costs, system complexity, and operational challenges must be carefully considered when choosing this method for specific applications.
Summary Table:
Aspect | Advantages | Disadvantages |
---|---|---|
Deposition Rates | High deposition rates and throughput, ideal for large-scale production. | Poor deposition rates for dielectric materials. |
Film Quality | Uniform, dense films with excellent adhesion and reproducibility. | Substrate heating may affect temperature-sensitive materials. |
Material Compatibility | Works with metals, alloys, dielectrics, and high-melting-point materials. | High system complexity and operational costs. |
Precision | Molecular-level control for pristine interfaces and tunable film properties. | Chamber coating and surface impurities may require additional cleaning. |
Environmental Impact | No atmospheric pollution, no heated parts, and versatile substrate coating. | Operational challenges and potential contamination risks. |
Discover how sputtering techniques can elevate your thin film deposition process—contact us today for expert advice!