Inert gases, such as nitrogen and argon, are widely used across various industries due to their non-reactive properties. Their primary advantage lies in preventing unwanted chemical reactions, such as oxidation and hydrolysis, which can degrade materials or samples. By creating a protective atmosphere, inert gases reduce reaction rates, minimize contamination risks, and enhance safety by preventing fires and explosions. They are particularly valuable in heat treatment processes, chemical reactions, and material processing, where maintaining a controlled, non-reactive environment is critical. Additionally, inert gases contribute to cost savings and improved performance in industrial applications by ensuring optimal conditions for sensitive processes.
Key Points Explained:
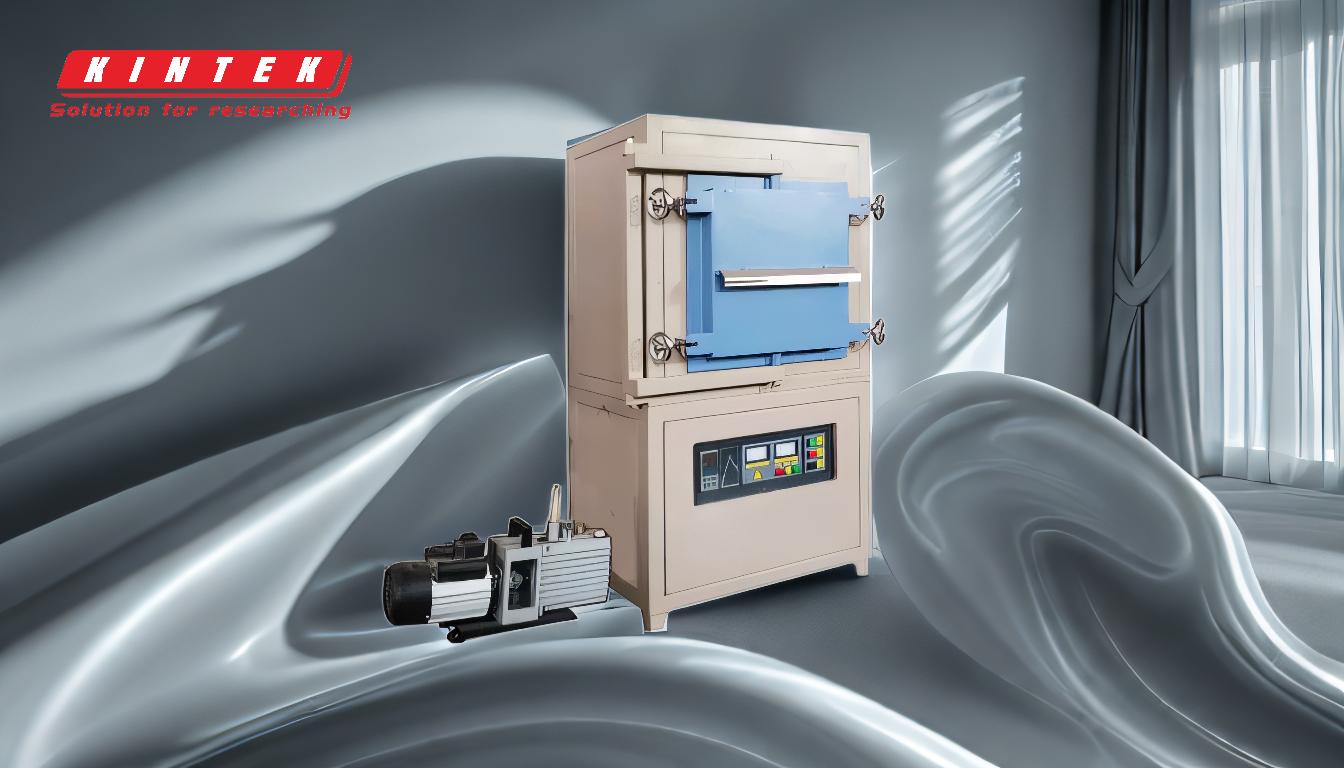
-
Prevention of Unwanted Chemical Reactions
- Inert gases like nitrogen and argon are chemically non-reactive, making them ideal for preventing oxidation, hydrolysis, and other undesirable reactions.
- These reactions often occur when materials are exposed to oxygen or moisture in the air, leading to degradation or contamination.
- By replacing reactive gases with inert gases, industries can maintain the integrity of sensitive materials and samples.
-
Reduction of Reaction Rates and Oxidation Potentials
- Inert gases slow down or completely halt chemical reactions, particularly oxidation processes.
- This is especially important in heat treatment applications, where oxidation can compromise the quality of materials like steel.
- For example, nitrogen is commonly used in furnaces to create a protective atmosphere that prevents carbon, oxygen, and nitrogen from reacting with steel.
-
Minimization of Contamination Risks
- Inert gases create a clean, non-reactive environment that reduces the risk of contamination from airborne particles or reactive gases.
- This is critical in industries such as pharmaceuticals, electronics, and food packaging, where even minor contamination can lead to product failure or safety hazards.
-
Enhanced Safety in Industrial Processes
- Inert gases are used to purge transfer lines, vessels, and reaction chambers to prevent fires and explosions.
- Their non-flammable nature makes them a reliable choice for creating a safe working environment in chemical plants and other high-risk settings.
- For example, argon is often used in welding to shield the weld area from reactive gases in the air, preventing combustion and ensuring a high-quality weld.
-
Optimization of Heat Treatment Processes
- Inert gas atmosphere furnaces are designed to provide precise temperature control and energy-efficient insulation.
- These features ensure optimal performance and cost savings while maintaining the quality of heat-treated materials.
- The use of inert gases in rotary tube furnaces, for instance, prevents oxidation during high-temperature processing of oxygen-sensitive materials.
-
Versatility in Applications
- Inert gases are used in a wide range of industries, including metallurgy, chemicals, electronics, and food packaging.
- Their ability to create a controlled, non-reactive environment makes them indispensable for processes like annealing, sintering, and chemical synthesis.
- For example, nitrogen is commonly used in food packaging to extend shelf life by displacing oxygen and preventing spoilage.
-
Cost-Effectiveness and Efficiency
- The use of inert gases can lead to significant cost savings by reducing material waste, improving process efficiency, and minimizing the need for post-processing treatments.
- Their non-reactive nature also reduces wear and tear on equipment, lowering maintenance costs over time.
- For instance, inert gas purging systems in chemical plants help maintain consistent product quality while reducing downtime and operational risks.
In summary, the advantages of inert gases stem from their non-reactive properties, which enable them to prevent unwanted chemical reactions, enhance safety, and optimize industrial processes. Their versatility and cost-effectiveness make them a valuable resource across a wide range of applications, ensuring high-quality outcomes and operational efficiency.
Summary Table:
Advantage | Key Benefit |
---|---|
Prevention of Unwanted Reactions | Stops oxidation, hydrolysis, and contamination. |
Reduction of Reaction Rates | Slows or halts oxidation, ensuring material quality. |
Minimization of Contamination Risks | Creates a clean, non-reactive environment for sensitive processes. |
Enhanced Safety | Prevents fires and explosions in high-risk settings. |
Optimization of Heat Treatment | Maintains precise temperature control and energy efficiency. |
Versatility in Applications | Used in metallurgy, electronics, food packaging, and more. |
Cost-Effectiveness and Efficiency | Reduces material waste, improves efficiency, and lowers maintenance costs. |
Learn how inert gases can transform your industrial processes—contact our experts today!