Sputtering and evaporation are both physical vapor deposition (PVD) techniques used to create thin films, but they differ significantly in their mechanisms, advantages, and applications. Sputtering offers several advantages over evaporation, including better adhesion, superior film quality, and more precise control over film composition. While evaporation is simpler and faster, sputtering provides higher uniformity, scalability, and compatibility with a wider range of materials. This analysis explores the key advantages of sputtering over evaporation, focusing on factors like adhesion, film quality, composition control, and scalability.
Key Points Explained:
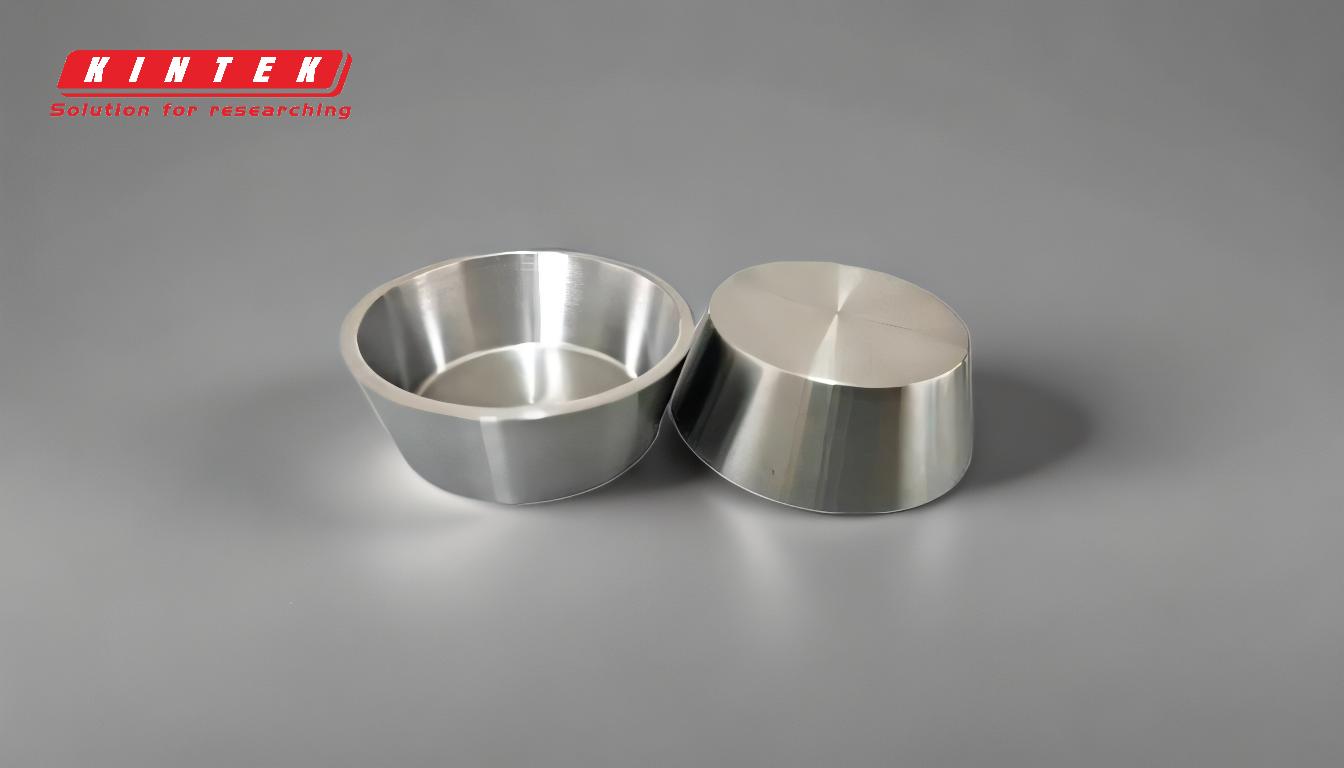
-
Better Adhesion
- Sputtering provides stronger adhesion between the deposited film and the substrate compared to evaporation. This is because sputtered particles have higher kinetic energy, which allows them to embed more effectively into the substrate surface.
- In evaporation, the vapor stream condenses on the substrate with lower energy, resulting in weaker bonding and adhesion.
- Strong adhesion is critical for applications requiring durable and long-lasting coatings, such as in semiconductor devices or protective coatings.
-
Superior Film Quality and Uniformity
- Sputtering produces films with better uniformity and fewer defects compared to evaporation. The process allows for precise control over film thickness and composition, even on complex geometries.
- Evaporation, while faster, often results in less uniform films, especially on non-planar surfaces, due to the directional nature of the vapor stream.
- The higher film quality achieved through sputtering is essential for applications like optical coatings, where consistency and precision are paramount.
-
Composition Control
- Sputtering maintains the composition of the source material in the deposited film, making it ideal for depositing alloys and complex materials. This is because sputtering ejects atoms directly from the target, preserving their stoichiometry.
- In evaporation, especially with alloys, different elements may vaporize at different rates, leading to compositional discrepancies in the deposited film.
- This advantage makes sputtering the preferred method for depositing multi-component materials, such as in the production of thin-film solar cells or magnetic storage media.
-
Higher Energy Deposited Species
- Sputtered particles have higher energy compared to evaporated particles, which improves film density and reduces porosity. This results in films with better mechanical and electrical properties.
- Evaporated particles, having lower energy, tend to form less dense films with larger grain sizes, which can affect performance in certain applications.
- The higher energy of sputtered particles also enhances step coverage, making it suitable for coating trenches and vias in microelectronics.
-
Scalability and Automation
- Sputtering is highly scalable and can be easily automated for large-scale production. This makes it suitable for industrial applications requiring consistent and high-quality coatings.
- While evaporation is faster and more cost-effective, it is less scalable and often requires manual intervention, limiting its use in high-volume manufacturing.
- The ability to automate sputtering processes reduces labor costs and improves reproducibility, which is critical for industries like automotive and aerospace.
-
Compatibility with a Wider Range of Materials
- Sputtering can deposit a broader range of materials, including high-melting-point metals, ceramics, and alloys, which are difficult to evaporate.
- Evaporation is limited to materials that can be vaporized at relatively low temperatures, restricting its applicability.
- This versatility makes sputtering the go-to method for advanced applications, such as depositing refractory metals in semiconductor manufacturing.
-
Lower Vacuum Requirements
- Sputtering operates at lower vacuum levels compared to evaporation, reducing the complexity and cost of the vacuum system.
- Evaporation requires a higher vacuum to prevent contamination and ensure efficient vaporization, which increases operational costs.
- The lower vacuum requirements of sputtering make it more accessible for smaller-scale operations and research laboratories.
-
Environmental and Safety Advantages
- Sputtering is generally safer and more environmentally friendly than evaporation, as it does not involve heating materials to extremely high temperatures, reducing the risk of thermal decomposition or hazardous emissions.
- Evaporation, particularly electron beam evaporation, requires high temperatures, which can pose safety risks and environmental concerns.
In summary, sputtering offers significant advantages over evaporation in terms of adhesion, film quality, composition control, and scalability. While evaporation is faster and more cost-effective for certain applications, sputtering is the preferred method for high-precision, high-performance coatings in industries ranging from microelectronics to optics. Its ability to deposit a wide range of materials with superior properties makes it a versatile and reliable choice for modern thin-film deposition.
Summary Table:
Aspect | Sputtering | Evaporation |
---|---|---|
Adhesion | Stronger adhesion due to higher kinetic energy of particles | Weaker bonding due to lower energy of vapor stream |
Film Quality | Superior uniformity, fewer defects, and precise thickness control | Less uniform films, especially on non-planar surfaces |
Composition Control | Maintains source material composition, ideal for alloys and complex materials | Compositional discrepancies due to varying vaporization rates |
Energy of Particles | Higher energy improves film density and reduces porosity | Lower energy results in less dense films with larger grain sizes |
Scalability | Highly scalable and easily automated for large-scale production | Less scalable, often requires manual intervention |
Material Compatibility | Deposits a wide range of materials, including high-melting-point metals | Limited to materials that can be vaporized at low temperatures |
Vacuum Requirements | Operates at lower vacuum levels, reducing system complexity and cost | Requires higher vacuum, increasing operational costs |
Environmental Safety | Safer and more environmentally friendly, with no extreme heating required | Higher temperatures pose safety and environmental risks |
Ready to elevate your thin-film deposition process? Contact us today to learn how sputtering can meet your needs!