Brazing is a widely used joining process that involves melting a filler metal into the joint between two or more metal parts. The choice of brazing metals and alloys depends on the materials being joined, the required strength, and the operating conditions of the final assembly. Commonly used brazing filler metals include silver-copper, copper-zinc, copper-phosphorus, palladium, and nickel. For stainless steel brazing, additional options like tin-lead solder, manganese-based, and precious metal filler metals are also employed. Each filler metal has specific properties, such as melting point, flow characteristics, and compatibility with base metals, making it suitable for particular applications. Understanding these materials and their properties is essential for selecting the right filler metal for a given brazing task.
Key Points Explained:
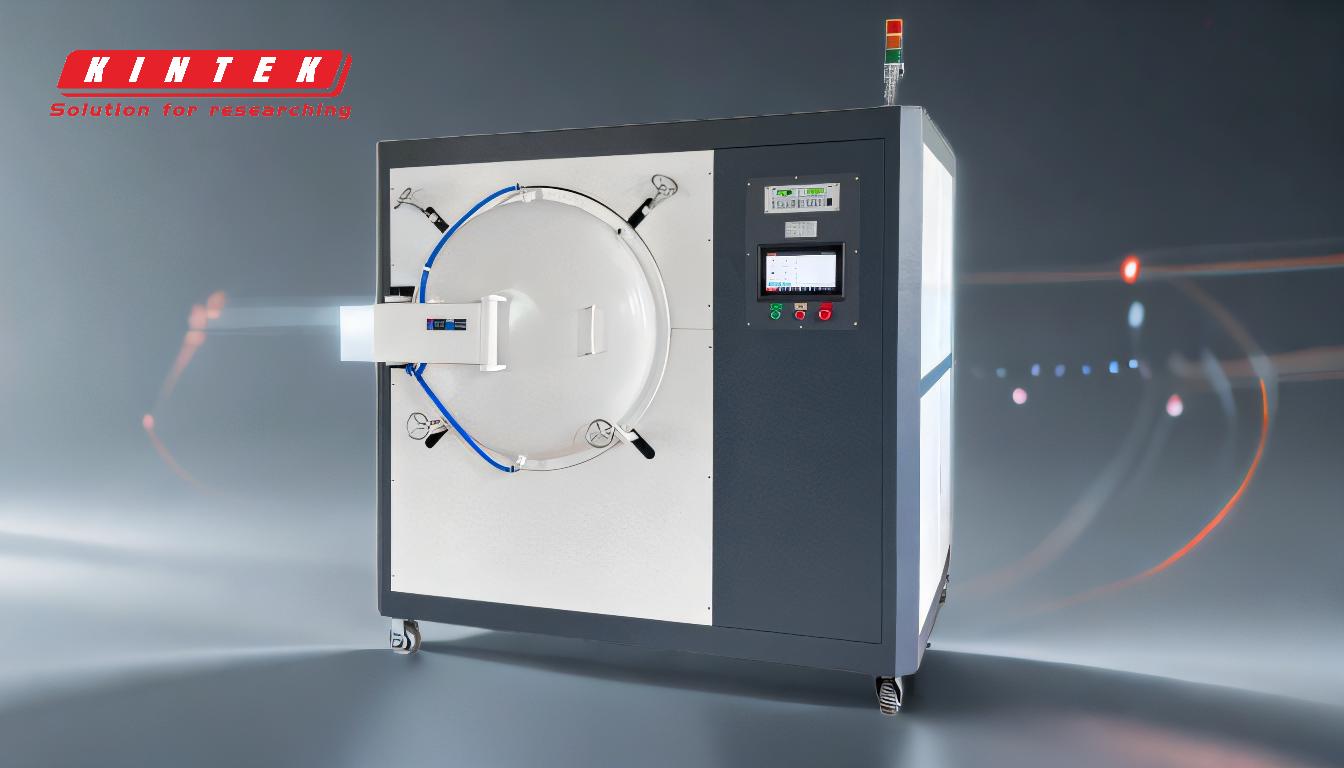
-
Silver-Copper Alloys:
- Silver-copper alloys are among the most widely used brazing filler metals due to their excellent flow properties, good wetting characteristics, and moderate melting temperatures.
- These alloys are often used for joining copper, brass, and stainless steel, and they provide strong, corrosion-resistant joints.
- The addition of other elements, such as zinc or cadmium, can further enhance their properties, though cadmium is increasingly avoided due to environmental concerns.
-
Copper-Zinc Alloys:
- Copper-zinc (brass) filler metals are commonly used for brazing steel and cast iron due to their high strength and relatively low cost.
- These alloys have higher melting points compared to silver-based fillers, making them suitable for applications requiring higher temperature resistance.
- However, they may not be ideal for joining non-ferrous metals like aluminum or magnesium due to compatibility issues.
-
Copper-Phosphorus Alloys:
- Copper-phosphorus alloys are specifically designed for brazing copper and copper alloys, as they are self-fluxing and do not require additional flux.
- These filler metals are cost-effective and provide good electrical conductivity, making them ideal for electrical and plumbing applications.
- However, they are not suitable for ferrous metals or alloys containing nickel due to the formation of brittle phosphides.
-
Palladium-Based Alloys:
- Palladium-based filler metals are used in high-performance applications, such as aerospace and electronics, where high strength and corrosion resistance are critical.
- These alloys have excellent wetting properties and can join a wide range of metals, including stainless steel, nickel, and titanium.
- Their high cost limits their use to specialized applications.
-
Nickel-Based Alloys:
- Nickel-based filler metals are preferred for high-temperature applications, such as gas turbines and chemical processing equipment, due to their exceptional strength and resistance to oxidation and corrosion.
- These alloys are suitable for joining nickel-based superalloys, stainless steel, and other high-temperature materials.
- They often require specialized brazing techniques, such as vacuum or controlled atmosphere brazing, to achieve optimal results.
-
Filler Metals for Stainless Steel:
- Stainless steel brazing requires filler metals that can withstand its unique properties, such as high chromium content and low thermal conductivity.
- Common choices include silver-based, copper-based, manganese-based, and nickel-based filler metals, as well as precious metal fillers like gold and platinum.
- Tin-lead solder is also used for low-temperature applications but is less common due to environmental regulations.
-
Considerations for Preventing Distortion:
- While not directly related to filler metal selection, preventing distortion during brazing is crucial for maintaining the integrity of the joint.
- Techniques such as stress relieving parts before brazing, using rigid fixtures, and designing parts to resist deformation can minimize distortion.
- Despite these measures, some distortion may still occur, especially in complex assemblies or thin-walled components.
By understanding the properties and applications of these brazing filler metals, manufacturers and engineers can make informed decisions to achieve strong, reliable, and durable joints tailored to their specific needs.
Summary Table:
Filler Metal | Key Properties | Common Applications |
---|---|---|
Silver-Copper | Excellent flow, good wetting, moderate melting point | Copper, brass, stainless steel |
Copper-Zinc | High strength, low cost, high melting point | Steel, cast iron |
Copper-Phosphorus | Self-fluxing, cost-effective, good electrical conductivity | Copper and copper alloys (electrical, plumbing) |
Palladium-Based | High strength, corrosion resistance, excellent wetting | Aerospace, electronics (stainless steel, nickel, titanium) |
Nickel-Based | High-temperature resistance, oxidation and corrosion resistance | Gas turbines, chemical processing (nickel superalloys, stainless steel) |
Stainless Steel | Compatible with high chromium content, low thermal conductivity | Silver, copper, manganese, nickel, and precious metal fillers (gold, platinum) |
Tin-Lead Solder | Low-temperature applications (less common due to environmental concerns) | Low-temperature stainless steel brazing |
Need help selecting the right brazing filler metal for your application? Contact our experts today for personalized advice!