Silicon carbide (SiC) is a highly versatile material widely used in the metallurgical industry due to its exceptional properties, such as high thermal conductivity, excellent thermal shock resistance, and superior mechanical strength. However, despite its advantages, silicon carbide ceramics face several challenges in their application, particularly in high-temperature and harsh environments like furnaces. These challenges include material degradation, cost, and manufacturing complexities.
Key Points Explained:
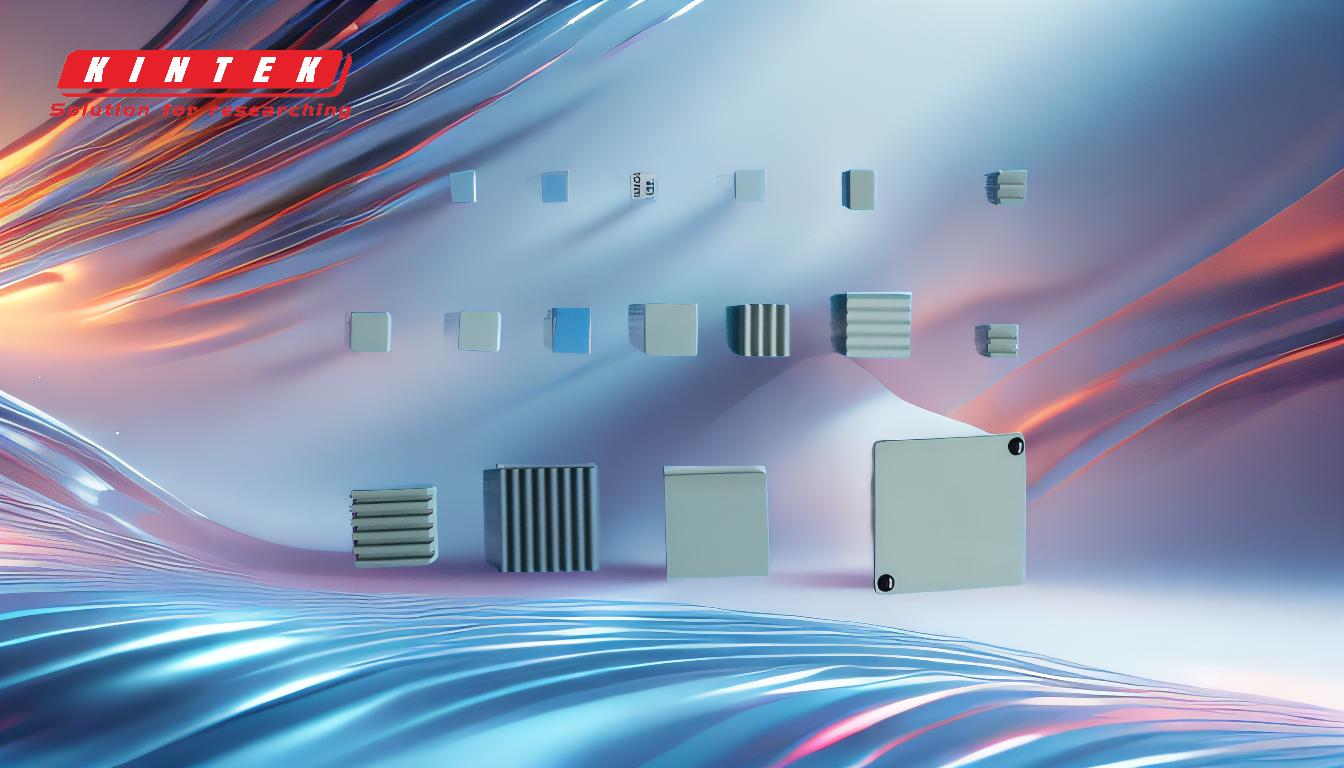
-
Material Degradation in High-Temperature Environments:
- Silicon carbide ceramics are often used in high-temperature applications, such as lining blocks and bricks for blast furnaces, muffle furnaces, and other types of furnaces. However, prolonged exposure to extreme temperatures can lead to oxidation and corrosion, which degrade the material over time.
- Oxidation occurs when silicon carbide reacts with oxygen at high temperatures, forming a silica layer. While this layer can provide some protection, it can also crack under thermal cycling, exposing the underlying material to further oxidation.
- Corrosion can occur when silicon carbide is exposed to molten metals or slag, leading to chemical reactions that weaken the material.
-
High Manufacturing Costs:
- The production of silicon carbide ceramics involves complex processes, such as sintering and machining, which require specialized equipment and high energy consumption. These factors contribute to the high cost of silicon carbide components.
- Additionally, the raw materials used in the production of silicon carbide, such as high-purity silicon and carbon, are expensive, further driving up the overall cost.
-
Brittleness and Mechanical Limitations:
- Despite its high hardness and strength, silicon carbide is inherently brittle, making it susceptible to cracking and fracture under mechanical stress or impact. This brittleness limits its use in applications where toughness and ductility are required.
- In applications like guide rails in blast furnaces and continuous furnaces, the mechanical wear and tear can lead to premature failure of silicon carbide components.
-
Thermal Shock Resistance Limitations:
- While silicon carbide has excellent thermal shock resistance compared to many other materials, it is not immune to thermal stress. Rapid temperature changes, such as those encountered in furnace operations, can cause microcracks to form and propagate, eventually leading to material failure.
-
Challenges in Machining and Fabrication:
- Silicon carbide is a hard and abrasive material, making it difficult to machine and shape into complex geometries. Specialized tools and techniques are required, which add to the cost and complexity of manufacturing.
- The precision required for applications like lining blocks and bricks further complicates the fabrication process, as even minor defects can compromise the performance of the final product.
-
Limited Availability of High-Quality Raw Materials:
- The quality of silicon carbide ceramics is highly dependent on the purity and consistency of the raw materials used. However, sourcing high-purity silicon and carbon can be challenging, and impurities in the raw materials can negatively affect the properties of the final product.
-
Environmental and Health Concerns:
- The production and processing of silicon carbide can generate dust and particulates that pose health risks to workers. Proper safety measures and ventilation systems are required to mitigate these risks.
- Additionally, the energy-intensive nature of silicon carbide production contributes to its environmental footprint, making sustainability a concern for manufacturers.
In summary, while silicon carbide ceramics offer significant advantages in high-temperature and harsh environments, they also present several challenges that need to be addressed. These include material degradation, high manufacturing costs, brittleness, thermal shock resistance limitations, machining difficulties, raw material availability, and environmental concerns. Addressing these challenges through advanced manufacturing techniques, material innovations, and sustainable practices will be key to expanding the use of silicon carbide in the metallurgical industry and beyond.
Summary Table:
Challenge | Description |
---|---|
Material Degradation | Oxidation and corrosion in high-temperature environments weaken the material over time. |
High Manufacturing Costs | Complex processes and expensive raw materials drive up production costs. |
Brittleness | Susceptible to cracking and fracture under mechanical stress or impact. |
Thermal Shock Resistance | Rapid temperature changes can cause microcracks and material failure. |
Machining Difficulties | Hard and abrasive nature complicates fabrication and increases costs. |
Raw Material Availability | Sourcing high-purity silicon and carbon is challenging and costly. |
Environmental and Health Concerns | Dust generation and energy-intensive processes pose health and sustainability risks. |
Learn how to address silicon carbide challenges in your applications—contact our experts today!