PVD (Physical Vapor Deposition) coatings offer a versatile range of color options, catering to both aesthetic and functional requirements. The colors achieved through PVD depend on the material being vaporized, the reactive gases used, and the deposition process conditions. Metallic shades like gold, rose gold, bronze, brass, nickel, chrome, and copper are common, while non-metallic colors such as black, blue, green, red, purple, and smoky tones are also achievable. These coatings can be applied to various substrates, including metals and plastics, and are available in polished, satin, or matte finishes. The ability to match specific color requirements makes PVD coatings ideal for industries requiring precise color consistency.
Key Points Explained:
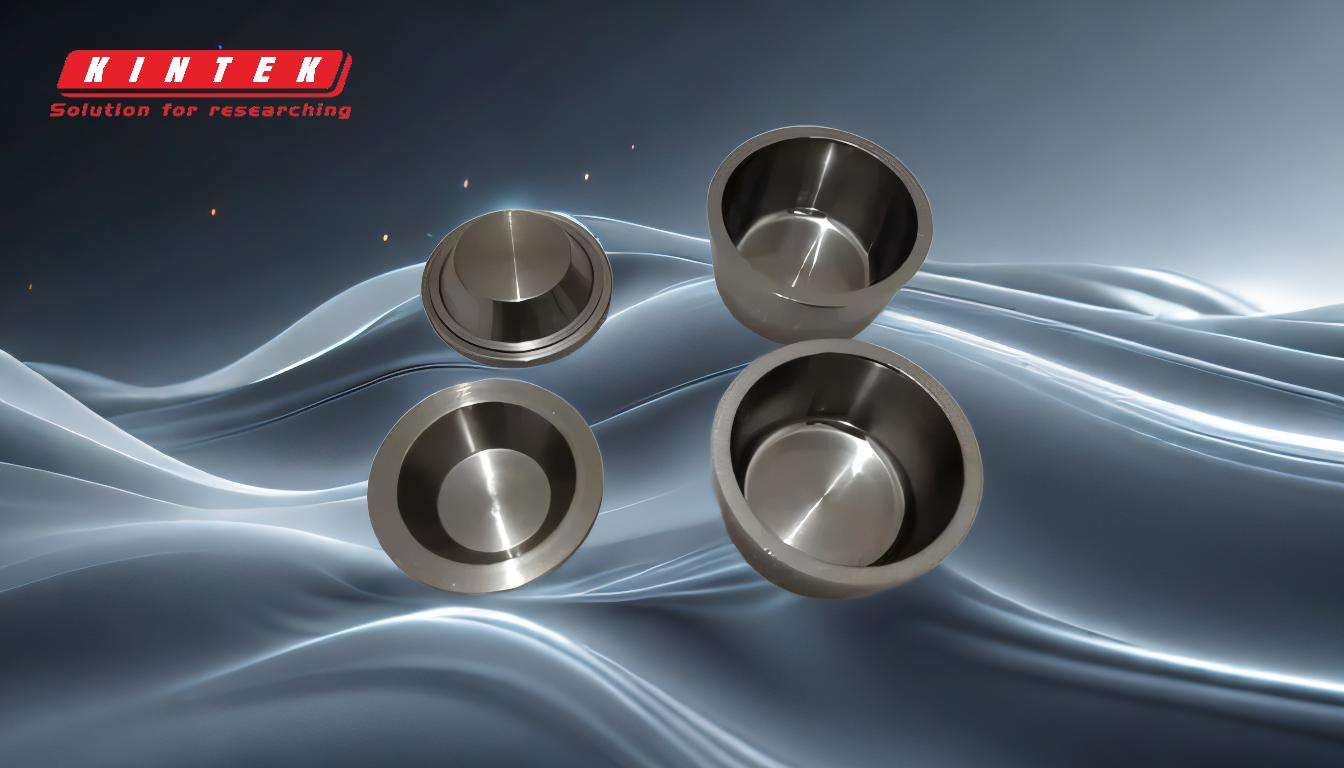
-
Wide Range of Metallic Colors:
- PVD coatings can produce metallic shades such as:
- Gold (including 24K gold and rose gold)
- Bronze
- Brass
- Nickel
- Chrome
- Copper
- These colors are achieved by vaporizing specific metals (targets) and controlling the deposition process conditions.
- PVD coatings can produce metallic shades such as:
-
Non-Metallic Colors:
- PVD coatings also support non-metallic colors, including:
- Black
- Blue
- Green
- Red
- Purple
- Smoky tones
- These colors are created by adjusting the reactive gas mixtures and deposition parameters.
- PVD coatings also support non-metallic colors, including:
-
Finish Options:
- PVD coatings are available in various finishes to suit different aesthetic and functional needs:
- Polished (high-gloss)
- Satin (semi-gloss)
- Matte (non-reflective)
- The finish can significantly impact the final appearance and application suitability.
- PVD coatings are available in various finishes to suit different aesthetic and functional needs:
-
Substrate Compatibility:
- PVD coatings can be applied to a wide range of substrates, including:
- Metals (e.g., stainless steel, copper, zinc alloy)
- Plastics
- This versatility allows for uniform color matching across different materials, ensuring consistency in product design.
- PVD coatings can be applied to a wide range of substrates, including:
-
Custom Color Matching:
- PVD coatings can be tailored to meet specific color requirements.
- For critical color matching, a combination of PVD layers and colored protective layers may be used to achieve precise results.
-
Affordability and Versatility:
- PVD coatings provide an affordable alternative to using pure metals for achieving specific colors.
- The wide range of available colors and finishes makes PVD coatings suitable for industries such as automotive, jewelry, electronics, and architecture.
-
Process Dependence:
- The exact color achieved depends on:
- The material being vaporized (target)
- The mixture of reactive gases used during deposition
- The conditions of the deposition process (e.g., temperature, pressure)
- This process dependence allows for fine-tuning of colors to meet specific needs.
- The exact color achieved depends on:
-
Examples of Rich Colors:
- PVD coatings can produce rich and vibrant colors, such as:
- Gold
- Rose gold
- Chrome
- Gunmetal
- Purple
- Burgundy
- These colors enhance the visual appeal of products while maintaining durability and resistance to wear.
- PVD coatings can produce rich and vibrant colors, such as:
By leveraging the flexibility of PVD coatings, manufacturers can achieve a wide spectrum of colors and finishes, ensuring both aesthetic appeal and functional performance in their products.
Summary Table:
Aspect | Details |
---|---|
Metallic Colors | Gold, rose gold, bronze, brass, nickel, chrome, copper |
Non-Metallic Colors | Black, blue, green, red, purple, smoky tones |
Finish Options | Polished (high-gloss), satin (semi-gloss), matte (non-reflective) |
Substrate Compatibility | Metals (e.g., stainless steel, copper), plastics |
Custom Color Matching | Tailored to meet specific requirements for precise color consistency |
Industries | Automotive, jewelry, electronics, architecture |
Unlock the full potential of PVD coatings for your products—contact our experts today!