Ball mills are versatile grinding machines used in various industries for size reduction and mixing of materials. They operate on different principles and come in various types, each suited for specific applications. The primary modes of ball mills include planetary ball mills, mixer mills, vibration mills, and horizontal rolling ball mills. These modes differ in their operating mechanisms, capacities, and the nature of the materials they can process. Planetary ball mills are known for their high-energy grinding, while mixer mills are ideal for small-scale applications. Vibration mills are used for fine grinding, and horizontal rolling ball mills are suitable for large-scale operations. Understanding these modes helps in selecting the right ball mill for specific needs.
Key Points Explained:
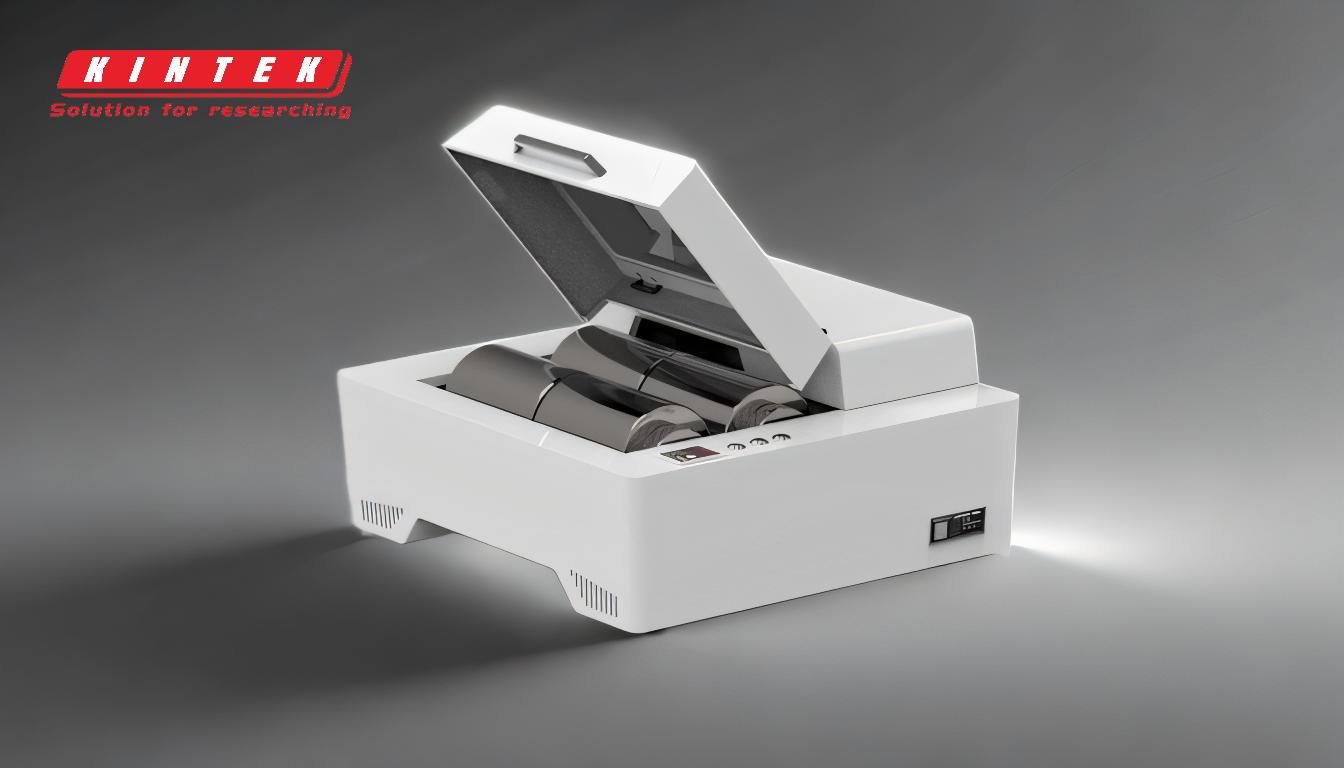
-
Planetary Ball Mills:
- Operating Principle: Planetary ball mills operate on the principle of high-energy impact grinding. They consist of a rotating disc (sun wheel) and several grinding jars (planets) that rotate around the central axis. The centrifugal forces generated by the rotation cause the grinding balls to collide with the material, resulting in fine grinding.
- Applications: Ideal for laboratory use, especially for small sample sizes. They are used in material science, chemistry, and biology for grinding, mixing, and homogenizing.
- Advantages: High-energy grinding, capable of producing very fine particles. Suitable for both wet and dry grinding.
- Limitations: Limited capacity, typically used for small-scale operations.
-
Mixer Mills:
- Operating Principle: Mixer mills use a high-frequency shaking motion to grind materials. The grinding jars are filled with grinding balls and the material to be ground. The jars are then shaken vigorously, causing the balls to impact the material.
- Applications: Suitable for small-scale grinding and mixing of materials. Commonly used in laboratories for sample preparation.
- Advantages: Compact design, easy to operate, and suitable for small sample sizes.
- Limitations: Limited to small-scale operations, not suitable for large quantities.
-
Vibration Mills:
- Operating Principle: Vibration mills use high-frequency vibrations to grind materials. The grinding chamber is filled with grinding balls and the material to be ground. The vibrations cause the balls to move rapidly, resulting in fine grinding.
- Applications: Used for fine grinding of materials in various industries, including pharmaceuticals, chemicals, and food processing.
- Advantages: Capable of producing very fine particles, suitable for both wet and dry grinding.
- Limitations: High energy consumption, may require frequent maintenance.
-
Horizontal Rolling Ball Mills:
- Operating Principle: Horizontal rolling ball mills consist of a horizontal cylinder filled with grinding balls and the material to be ground. The cylinder rotates around its longitudinal axis, causing the balls to cascade and grind the material.
- Applications: Suitable for large-scale operations, used in industries such as mining, cement, and ceramics.
- Advantages: High capacity, capable of processing large quantities of material. Suitable for both wet and dry grinding.
- Limitations: Requires a large space, higher energy consumption compared to other types.
-
Capacity Considerations:
- Planetary Ball Mills: Typically have small capacities, ranging from a few milliliters to a few liters.
- Mixer Mills: Designed for small-scale operations, with capacities usually less than a liter.
- Vibration Mills: Can handle small to medium capacities, depending on the design.
- Horizontal Rolling Ball Mills: Capable of handling large capacities, up to several hundred liters.
-
Material Considerations:
- Planetary Ball Mills: Suitable for a wide range of materials, including hard and brittle substances.
- Mixer Mills: Best for soft to medium-hard materials.
- Vibration Mills: Ideal for fine grinding of brittle materials.
- Horizontal Rolling Ball Mills: Suitable for a wide range of materials, including hard and abrasive substances.
-
Energy Efficiency:
- Planetary Ball Mills: High energy efficiency due to the high-energy impact grinding mechanism.
- Mixer Mills: Moderate energy efficiency, suitable for small-scale operations.
- Vibration Mills: High energy consumption due to the high-frequency vibrations.
- Horizontal Rolling Ball Mills: Moderate to high energy consumption, depending on the size and operational parameters.
-
Maintenance and Operational Costs:
- Planetary Ball Mills: Low maintenance, but may require frequent replacement of grinding balls.
- Mixer Mills: Low maintenance, easy to operate.
- Vibration Mills: High maintenance due to the wear and tear caused by high-frequency vibrations.
- Horizontal Rolling Ball Mills: Moderate to high maintenance, depending on the scale of operation.
In conclusion, the choice of ball mill mode depends on the specific requirements of the application, including the type of material, desired particle size, and scale of operation. Each mode has its advantages and limitations, and understanding these can help in selecting the most appropriate ball mill for a given task.
Summary Table:
Ball Mill Type | Operating Principle | Applications | Advantages | Limitations |
---|---|---|---|---|
Planetary Ball Mills | High-energy impact grinding | Laboratories, small sample sizes | High-energy grinding, fine particles | Limited capacity, small-scale operations |
Mixer Mills | High-frequency shaking motion | Small-scale grinding, sample preparation | Compact design, easy to operate | Limited to small-scale operations |
Vibration Mills | High-frequency vibrations | Fine grinding in pharmaceuticals, chemicals | Produces very fine particles | High energy consumption, frequent maintenance |
Horizontal Rolling Ball Mills | Horizontal cylinder rotation | Large-scale operations in mining, cement | High capacity, processes large quantities | Requires large space, higher energy usage |
Need help choosing the right ball mill for your application? Contact our experts today for personalized guidance!