Compression molding is a versatile manufacturing process used to shape materials like rubber and composites into desired forms. The process involves placing pre-measured material into a mold cavity, applying heat and pressure to fill the cavity, and allowing excess material (flash) to escape through grooves. There are four main types of compression molds: flash, positive, landed positive, and semi-positive. Additionally, compression molding can be categorized into bulk and sheet molding, with bulk molding involving a mixture of fillers, catalysts, and reinforcements. Each type has unique characteristics and applications, making it essential to choose the right mold and material for optimal results.
Key Points Explained:
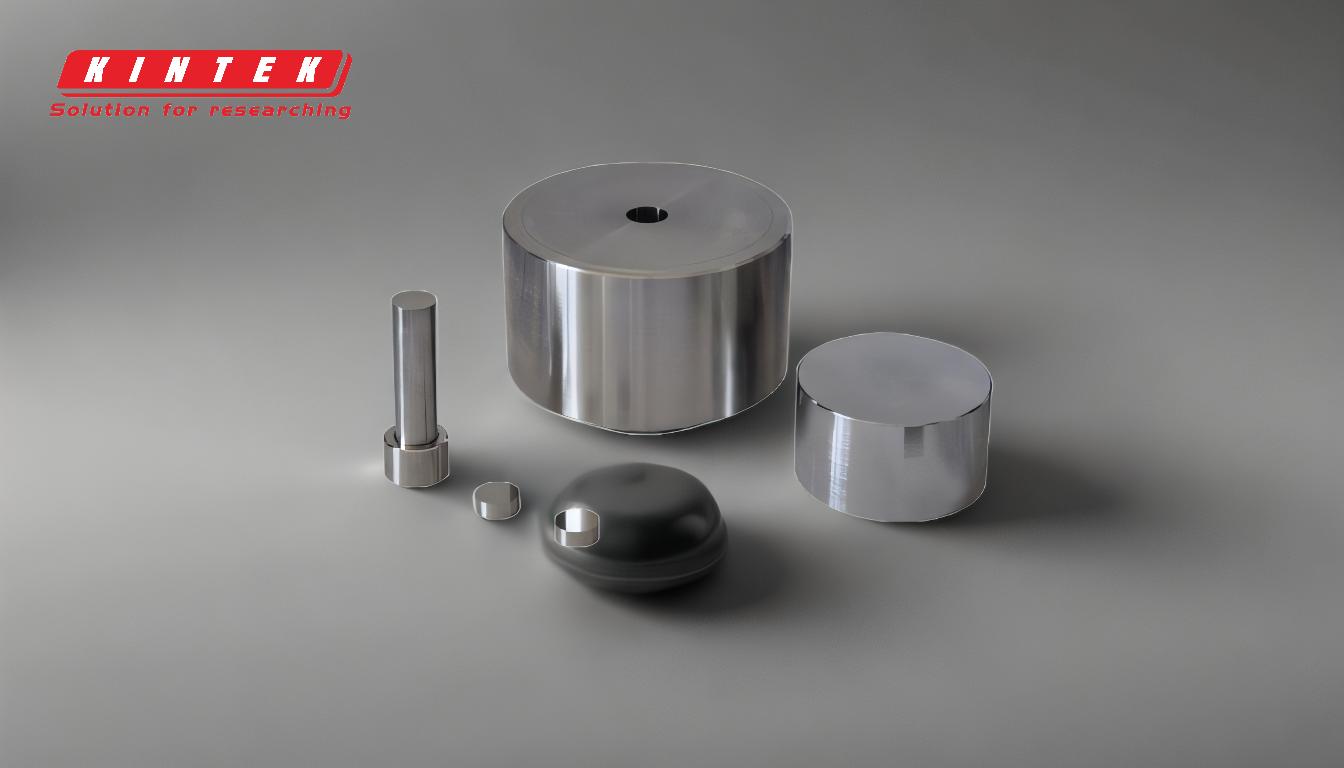
-
Types of Compression Molds:
- Flash Mold: The most commonly used type, where excess material (flash) flows out of the mold through special grooves. This type is suitable for simpler designs and allows for easy removal of excess material.
- Positive Mold: Designed to contain all the material within the mold cavity, leaving no room for flash. This type is ideal for high-precision parts but requires exact material measurement.
- Landed Positive Mold: A hybrid between flash and positive molds, where a small amount of flash is allowed but controlled. This type strikes a balance between precision and ease of use.
- Semi-Positive Mold: Similar to landed positive but with more controlled flash flow. It is used for complex shapes where some excess material is tolerable.
-
Types of Compression Molding:
- Bulk Molding: Involves using a mixture of fillers, catalysts, stabilizers, pigments, and fiber reinforcements. This method is ideal for creating strong, durable parts and is commonly used in automotive and industrial applications.
- Sheet Molding: Uses pre-formed sheets of material, which are cut to size and placed into the mold. This method is often used for larger, flatter parts and provides consistent material distribution.
-
Process Overview:
- Material is placed into the mold cavity in a well-shaped, un-branched form.
- The mold is closed and subjected to heat and pressure, causing the material to flow and fill the cavity.
- Excess material (flash) escapes through grooves, ensuring the final part is free of defects.
-
Challenges in Compression Molding:
- Material Measurement: Accurately cutting or weighing the material is crucial. Too little material can result in defects like flow lines, blisters, or unfilled parts.
- Excess Material: Overfilling the mold can lead to heavy flash, which is difficult to remove and can affect the final product's quality.
- Placement Precision: Incorrect placement of material in the mold can cause uneven distribution and defects.
-
Applications and Considerations:
- Material Selection: The choice of material (rubber, composites, etc.) depends on the desired properties of the final product, such as strength, flexibility, or heat resistance.
- Mold Design: The type of mold selected (flash, positive, etc.) impacts the ease of production, precision, and final product quality.
- Process Optimization: Properly balancing material quantity, placement, and mold type is essential for minimizing defects and maximizing efficiency.
By understanding these key points, equipment and consumable purchasers can make informed decisions about the types of molds and materials best suited for their specific needs in compression molding.
Summary Table:
Aspect | Details |
---|---|
Types of Molds | Flash, Positive, Landed Positive, Semi-Positive |
Molding Types | Bulk Molding (fillers, catalysts, reinforcements), Sheet Molding (pre-formed sheets) |
Process Overview | Material placed in mold, heat and pressure applied, excess material escapes through grooves |
Challenges | Material measurement, excess material, placement precision |
Applications | Automotive, industrial, and high-precision parts |
Ready to optimize your compression molding process? Contact our experts today for tailored solutions!