Permanent mold casting is a versatile manufacturing process used to produce high-quality metal parts with excellent surface finish and dimensional accuracy. The process involves pouring molten metal into a reusable mold, typically made of steel or cast iron, which is designed to withstand repeated use. There are four main types of permanent mold casting: gravity, slush, low-pressure, and vacuum. Each type has unique characteristics, advantages, and applications, making them suitable for different manufacturing needs. Below, we explore these types in detail to help you understand their differences and determine which might be best for your specific requirements.
Key Points Explained:
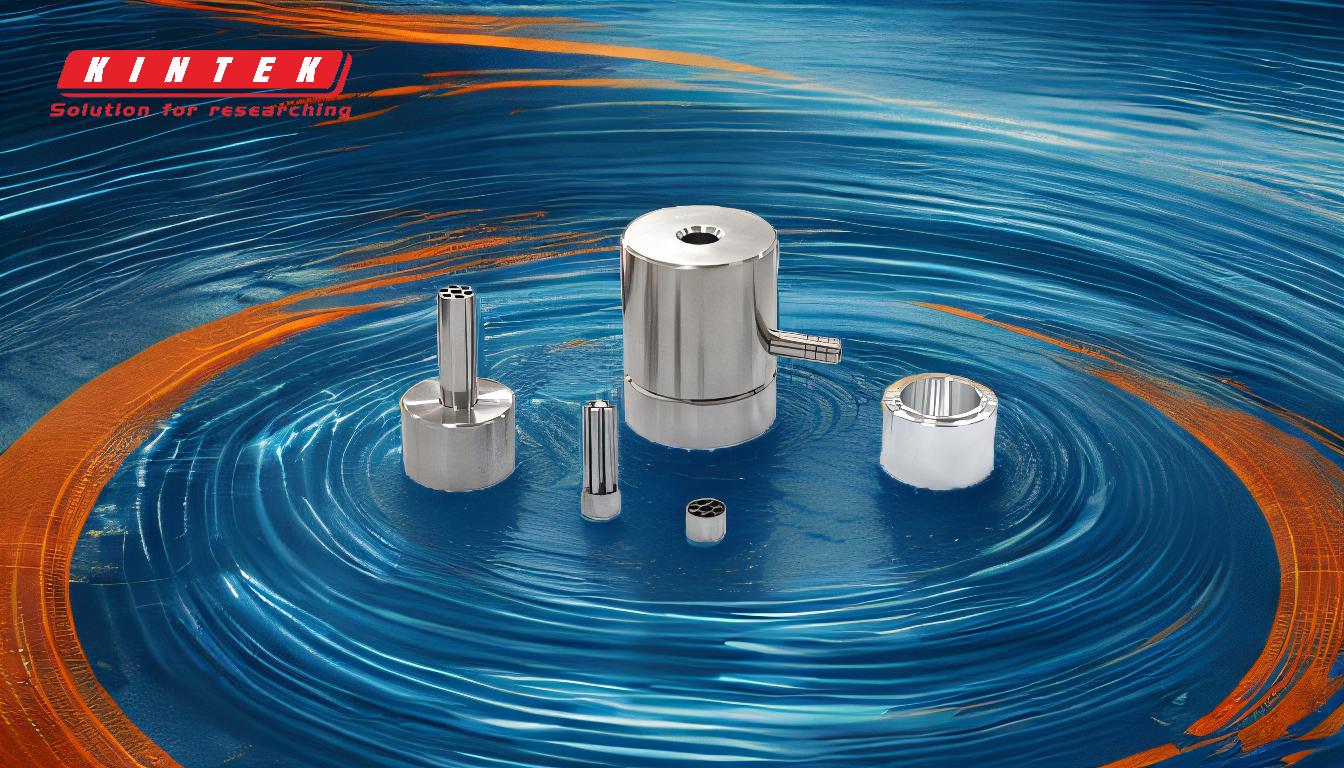
-
Gravity Permanent Mold Casting:
- Process: In gravity casting, molten metal is poured into the mold under the influence of gravity alone. The mold is preheated to ensure proper metal flow and solidification.
-
Advantages:
- Simple and cost-effective process.
- Suitable for producing parts with good surface finish and dimensional accuracy.
- Ideal for medium to high-volume production.
- Applications: Commonly used for manufacturing automotive components, such as engine blocks, cylinder heads, and wheels.
-
Slush Permanent Mold Casting:
- Process: Slush casting involves pouring molten metal into the mold and allowing it to solidify only on the outer surface. The remaining liquid metal is then poured out, leaving a hollow shell.
-
Advantages:
- Produces lightweight, hollow parts with thin walls.
- Reduces material usage and cost.
- Suitable for decorative or non-structural components.
- Applications: Often used for making decorative items, such as statues, lamps, and ornamental hardware.
-
Low-Pressure Permanent Mold Casting:
- Process: In low-pressure casting, molten metal is forced into the mold using low pressure (typically less than 1 bar). This ensures better control over the filling process and reduces turbulence.
-
Advantages:
- Produces parts with fewer defects, such as porosity and inclusions.
- Improves mechanical properties due to controlled solidification.
- Suitable for complex geometries and thin-walled parts.
- Applications: Widely used in the aerospace and automotive industries for components like engine pistons, transmission cases, and structural parts.
-
Vacuum Permanent Mold Casting:
- Process: Vacuum casting involves creating a vacuum inside the mold cavity to draw molten metal into the mold. This method minimizes air entrapment and oxidation.
-
Advantages:
- Produces high-quality parts with excellent surface finish and minimal defects.
- Reduces the risk of gas porosity and improves mechanical properties.
- Suitable for high-performance applications.
- Applications: Commonly used for manufacturing precision components in industries such as aerospace, medical, and electronics.
By understanding the differences between these four types of permanent mold casting, you can make an informed decision about which method best suits your manufacturing needs. Each type offers unique benefits, and the choice depends on factors such as part complexity, material requirements, production volume, and desired mechanical properties.
Summary Table:
Type | Process | Advantages | Applications |
---|---|---|---|
Gravity Casting | Molten metal poured under gravity; mold preheated for proper solidification. | Simple, cost-effective, good surface finish, medium to high-volume production. | Automotive components (engine blocks, cylinder heads, wheels). |
Slush Casting | Molten metal solidifies on outer surface; remaining liquid poured out. | Lightweight, hollow parts, reduced material usage, decorative applications. | Decorative items (statues, lamps, ornamental hardware). |
Low-Pressure Casting | Molten metal forced into mold using low pressure (<1 bar). | Fewer defects, improved mechanical properties, complex geometries. | Aerospace and automotive parts (engine pistons, transmission cases). |
Vacuum Casting | Vacuum draws molten metal into mold; minimizes air entrapment and oxidation. | High-quality parts, minimal defects, suitable for high-performance applications. | Precision components (aerospace, medical, electronics). |
Need help selecting the right permanent mold casting method for your project? Contact our experts today!