Silicon carbide (SiC) is a versatile material with a wide range of forms and applications, each tailored to specific industrial needs. The different types of silicon carbide include bricks, foam, honeycomb, powder (micron and submicron), whiskers, nanoparticles, sponges, sputtering targets, and wool. These forms are engineered to meet the demands of various industries, such as aerospace, automotive, electronics, and energy, due to their exceptional properties like high thermal conductivity, chemical inertness, and mechanical strength. Understanding the distinct types of silicon carbide helps purchasers select the appropriate form for their specific requirements, ensuring optimal performance and cost-effectiveness.
Key Points Explained:
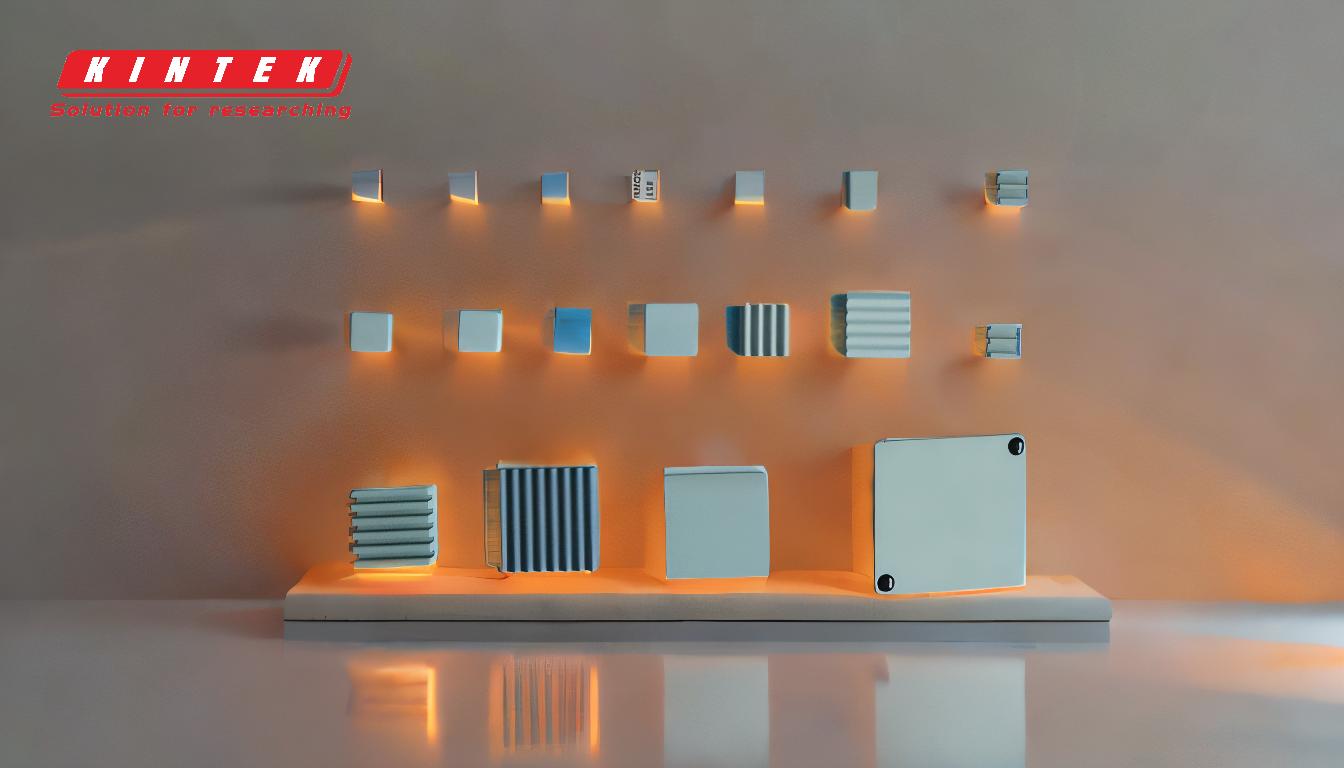
-
Silicon Carbide Bricks:
- These are dense, durable blocks used in high-temperature applications such as kiln linings and furnace components.
- They offer excellent thermal shock resistance and are ideal for environments requiring structural integrity under extreme heat.
-
Silicon Carbide Foam:
- A lightweight, porous material used in filtration systems, catalytic converters, and thermal insulation.
- Its high surface area and permeability make it suitable for applications requiring efficient gas or liquid flow.
-
Silicon Carbide Honeycomb:
- This structured form is commonly used in catalytic converters and heat exchangers.
- Its geometric design maximizes surface area while maintaining structural strength, making it effective for chemical reactions and heat transfer.
-
Silicon Carbide Powder:
- Available in micron and submicron sizes, this powder is used in abrasives, coatings, and advanced ceramics.
- Submicron powders are particularly valuable in precision applications like semiconductor manufacturing.
-
Silicon Carbide Whiskers:
- These are single-crystal fibers used as reinforcing agents in composite materials.
- They enhance the mechanical properties of composites, making them stronger and more resistant to wear.
-
Silicon Carbide Nanoparticles:
- Extremely small particles used in nanotechnology, coatings, and advanced materials.
- Their high surface-to-volume ratio makes them ideal for applications requiring enhanced reactivity or conductivity.
-
Silicon Carbide Sponges:
- Porous materials used for filtration, absorption, and thermal management.
- Their open-cell structure allows for efficient fluid or gas passage while maintaining thermal stability.
-
Silicon Carbide Sputtering Targets:
- Used in thin-film deposition processes for semiconductors and optical coatings.
- They provide high purity and uniformity, essential for producing high-quality thin films.
-
Silicon Carbide Wool:
- A fibrous form used for insulation in high-temperature environments.
- It offers excellent thermal resistance and flexibility, making it suitable for lining furnaces and kilns.
Each form of silicon carbide ceramic is designed to address specific industrial challenges, ensuring that purchasers can find the right material for their unique needs. By understanding the properties and applications of these different types, buyers can make informed decisions that optimize performance and cost-efficiency.
Summary Table:
Type | Applications | Key Properties |
---|---|---|
Bricks | Kiln linings, furnace components | High thermal shock resistance, structural integrity |
Foam | Filtration systems, catalytic converters, thermal insulation | Lightweight, porous, high surface area |
Honeycomb | Catalytic converters, heat exchangers | Geometric design, high surface area, structural strength |
Powder (Micron/Submicron) | Abrasives, coatings, advanced ceramics, semiconductor manufacturing | Precision, high purity, submicron size for advanced applications |
Whiskers | Reinforcing agents in composites | Single-crystal fibers, enhanced mechanical strength |
Nanoparticles | Nanotechnology, coatings, advanced materials | High surface-to-volume ratio, enhanced reactivity |
Sponges | Filtration, absorption, thermal management | Open-cell structure, thermal stability |
Sputtering Targets | Thin-film deposition for semiconductors, optical coatings | High purity, uniformity |
Wool | High-temperature insulation, furnace linings | Excellent thermal resistance, flexibility |
Need the right silicon carbide for your application? Contact us today for expert guidance!