Ball mills, while widely used for grinding and mixing materials, come with several notable disadvantages. These include being a slow and inefficient process, generating significant noise and vibrations, and having limitations in handling certain types of materials like soft, tacky, or fibrous substances. Additionally, ball mills are prone to wear and tear, which can lead to contamination and high energy consumption. Their large size and weight also make them cumbersome to handle and transport. These drawbacks must be carefully considered when selecting equipment for grinding or mixing applications.
Key Points Explained:
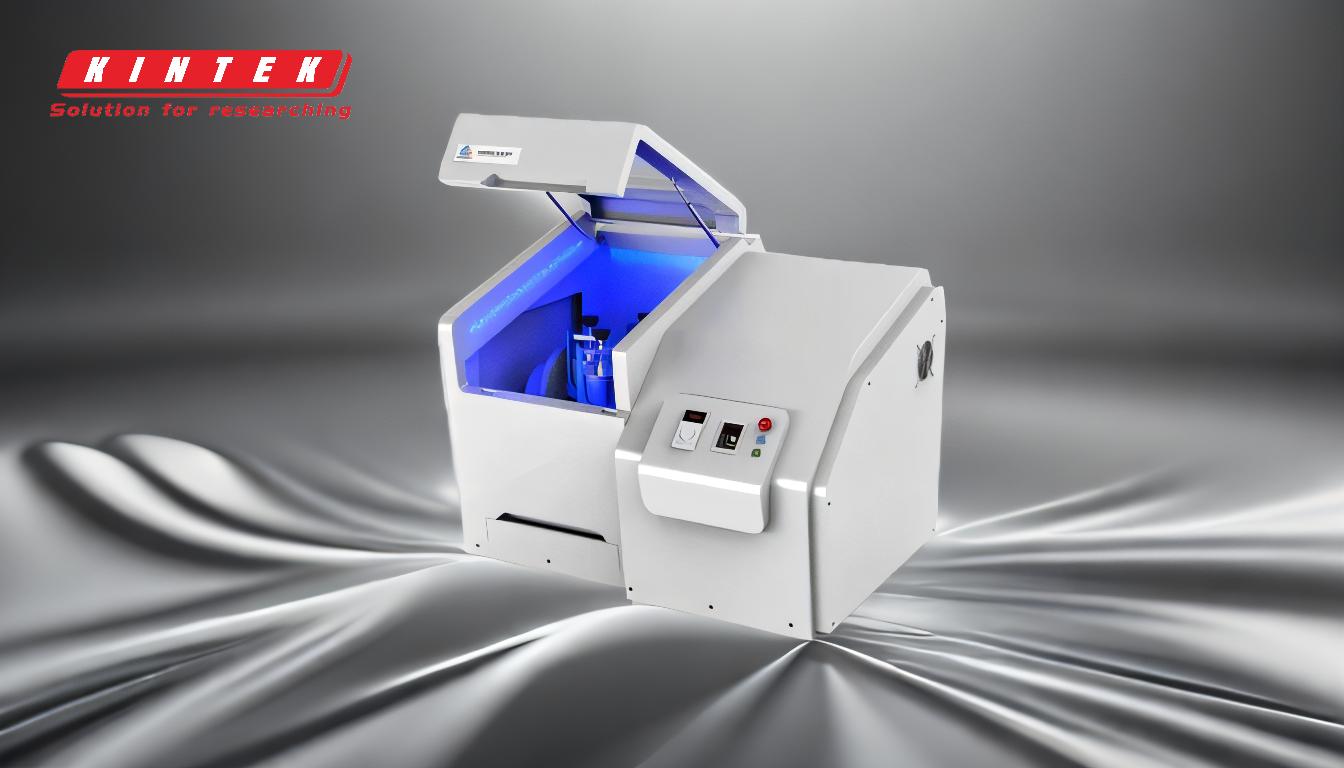
-
Slow Process:
- Ball mills are inherently slow in operation due to the grinding mechanism, which relies on the cascading and tumbling of grinding media (balls) inside the cylinder. This results in longer processing times compared to other grinding equipment, such as hammer mills or jet mills.
- The inefficiency is further compounded by the need for repeated grinding cycles to achieve the desired particle size, making it unsuitable for applications requiring rapid processing.
-
Noise and Vibrations:
- Ball mills generate significant noise and vibrations during operation, which can be disruptive and harmful in industrial settings. While the use of rubber balls can mitigate some of the noise, it does not eliminate the issue entirely.
- The vibrations can also lead to structural wear and tear on the mill itself, as well as on surrounding equipment, potentially increasing maintenance costs.
-
Inability to Handle Certain Materials:
- Ball mills are not well-suited for grinding soft, tacky, or fibrous materials. These materials tend to clog the grinding media or stick to the walls of the cylinder, reducing efficiency and requiring frequent cleaning.
- This limitation makes ball mills less versatile compared to other grinding technologies that can handle a wider range of material types.
-
Wear and Contamination:
- The grinding process causes wear on the balls and the inner walls of the cylinder, leading to the gradual degradation of the equipment. This wear can introduce contamination into the processed material, which is particularly problematic in industries requiring high purity, such as pharmaceuticals or food processing.
- Regular replacement of grinding media and liners is necessary, adding to operational costs.
-
High Energy Consumption:
- Ball mills are energy-intensive due to friction between the grinding media, the material being processed, and the cylinder walls. This results in high specific energy consumption, making them less cost-effective for large-scale operations.
- The energy inefficiency is further exacerbated by heat generation, which can negatively affect heat-sensitive materials.
-
Limited Capacity for Large Quantities:
- Ball mills have a limited capacity for handling large quantities of material, making them unsuitable for high-throughput applications. Scaling up production often requires multiple units, increasing both capital and operational expenses.
- The large size and weight of ball mills also make them difficult to transport and install, further limiting their practicality in some settings.
-
Cumbersome and Heavy:
- The design of ball mills, which includes heavy grinding media and robust construction, makes them bulky and difficult to maneuver. This can pose challenges in terms of installation, maintenance, and relocation.
- The large footprint of ball mills may also be a constraint in facilities with limited space.
In summary, while ball mills are effective for certain grinding applications, their disadvantages—such as slow processing, noise, wear, and limited versatility—make them less suitable for some industries and materials. Careful consideration of these drawbacks is essential when selecting grinding equipment to ensure optimal performance and cost-effectiveness.
Summary Table:
Disadvantage | Description |
---|---|
Slow Process | Inefficient grinding mechanism, longer processing times, and repeated cycles. |
Noise and Vibrations | Disruptive noise and vibrations, leading to structural wear and higher costs. |
Material Limitations | Poor handling of soft, tacky, or fibrous materials, reducing efficiency. |
Wear and Contamination | Equipment wear introduces contamination, requiring frequent maintenance. |
High Energy Consumption | Energy-intensive operation, leading to higher costs and heat generation. |
Limited Capacity | Unsuitable for large quantities, requiring multiple units for scaling. |
Cumbersome and Heavy | Bulky design, difficult to transport, and challenging to install in tight spaces. |
Need help choosing the right grinding equipment? Contact our experts today for tailored solutions!