Two-roll mills are widely used in industries for processing high-viscosity pastes due to their ability to maintain low temperatures and handle demanding dispersion work. However, they come with notable disadvantages, primarily related to the exposure of the paste on the rollers. The vast exposed surface area of the paste on the rollers can lead to the loss of volatiles, which can compromise the quality and consistency of the final product. This issue is particularly significant in applications where the retention of volatile components is critical.
Key Points Explained:
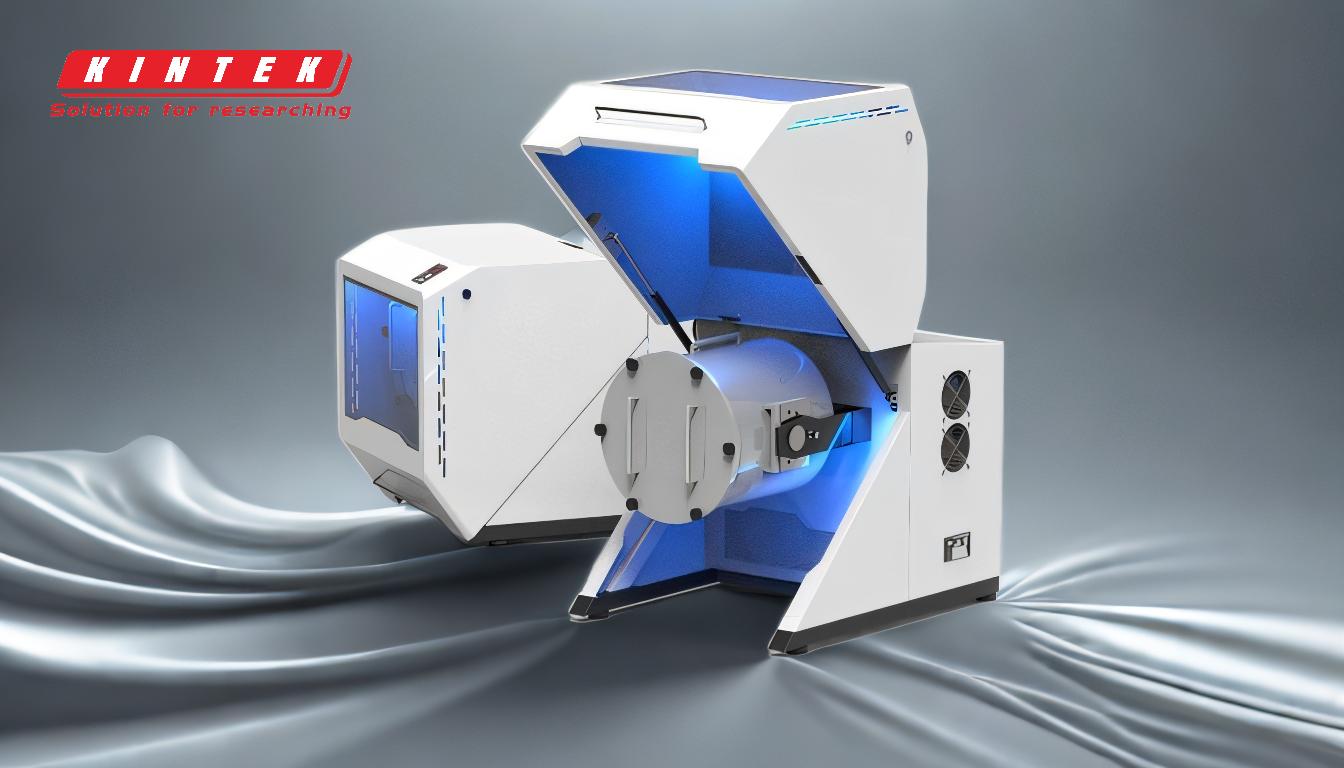
-
Volatile Loss Due to Exposed Surface Area:
- Explanation: One of the most significant disadvantages of a two-roll mill is the large exposed surface area of the paste on the rollers. This exposure can lead to the evaporation or loss of volatile components in the material being processed.
- Implications: The loss of volatiles can alter the chemical composition and physical properties of the paste, potentially leading to suboptimal product quality. This is especially problematic in industries where precise formulations are required, such as pharmaceuticals, cosmetics, and specialty chemicals.
- Mitigation: To address this issue, operators may need to adjust processing conditions, such as reducing the temperature or increasing the speed of the rollers, but these adjustments can have trade-offs in terms of processing efficiency and product consistency.
-
Limited Control Over Temperature and Shear:
- Explanation: While two-roll mills are effective at maintaining low temperatures due to the high surface contact with cooled rollers, they offer limited control over the precise temperature and shear forces applied to the material.
- Implications: Inconsistent temperature and shear can lead to uneven dispersion and mixing, which may affect the homogeneity and performance of the final product. This limitation can be particularly challenging when processing sensitive materials that require precise control over these parameters.
- Mitigation: Advanced two-roll mills with enhanced temperature control systems and adjustable roller speeds can help mitigate this issue, but they may come at a higher cost and complexity.
-
Potential for Material Contamination:
- Explanation: The open design of two-roll mills can expose the material to environmental contaminants, such as dust, moisture, and other airborne particles.
- Implications: Contamination can compromise the purity and quality of the product, particularly in industries where high levels of cleanliness are required, such as food processing and pharmaceuticals.
- Mitigation: Implementing enclosed or semi-enclosed designs and maintaining a clean processing environment can help reduce the risk of contamination, but these measures may add to the operational complexity and cost.
-
Operational Complexity and Maintenance:
- Explanation: Two-roll mills require regular maintenance to ensure optimal performance, including roller alignment, temperature control, and cleaning.
- Implications: The need for frequent maintenance can lead to downtime and increased operational costs. Additionally, the complexity of the equipment may require skilled operators, further adding to the operational expenses.
- Mitigation: Investing in high-quality equipment with robust maintenance features and providing adequate training for operators can help reduce downtime and maintenance costs.
-
Limited Scalability:
- Explanation: Two-roll mills are typically designed for batch processing, which can limit their scalability for large-scale production.
- Implications: For industries requiring high-volume production, the batch processing nature of two-roll mills may result in inefficiencies and higher production costs.
- Mitigation: While some two-roll mills can be scaled up, they may not be as efficient as continuous processing systems, such as three-roll mills or other advanced mixing technologies.
In summary, while two-roll mills offer several advantages, including the ability to handle high-viscosity pastes and maintain low temperatures, they also come with significant disadvantages. These include the loss of volatiles due to the exposed surface area, limited control over temperature and shear, potential for material contamination, operational complexity, and limited scalability. Understanding these drawbacks is crucial for equipment purchasers to make informed decisions and implement appropriate mitigation strategies to ensure optimal performance and product quality.
Summary Table:
Disadvantage | Explanation | Implications | Mitigation Strategies |
---|---|---|---|
Volatile Loss | Large exposed surface area leads to evaporation of volatile components. | Alters chemical composition, affecting product quality. | Adjust processing conditions (e.g., temperature, roller speed). |
Limited Temperature & Shear Control | Inconsistent temperature and shear forces during processing. | Uneven dispersion and mixing, impacting product homogeneity. | Use advanced mills with better control systems. |
Material Contamination | Open design exposes material to dust, moisture, and airborne particles. | Compromises product purity, especially in sensitive industries. | Implement enclosed designs and maintain a clean environment. |
Operational Complexity | Requires regular maintenance (roller alignment, temperature control, cleaning). | Increases downtime and operational costs. | Invest in high-quality equipment and train operators. |
Limited Scalability | Designed for batch processing, not ideal for large-scale production. | Inefficient for high-volume production, leading to higher costs. | Consider continuous processing systems like three-roll mills. |
Need help choosing the right equipment for your needs? Contact us today for expert guidance!