Ion Beam Deposition (IBD) is a highly precise and controlled method for depositing thin films, particularly in applications requiring exceptional uniformity and sub-Angstrom thickness precision. However, it comes with several disadvantages that make it less suitable for certain applications or cost-sensitive projects. These include a small deposition area, low effective deposition rate, high equipment and operating costs, complexity in scaling up, and unsuitability for large-area uniform films. While IBD excels in high-performance applications like MRAM and advanced CMOS technology, its limitations often make alternative methods like ion-assisted deposition or magnetron sputtering more attractive for broader or cost-sensitive uses.
Key Points Explained:
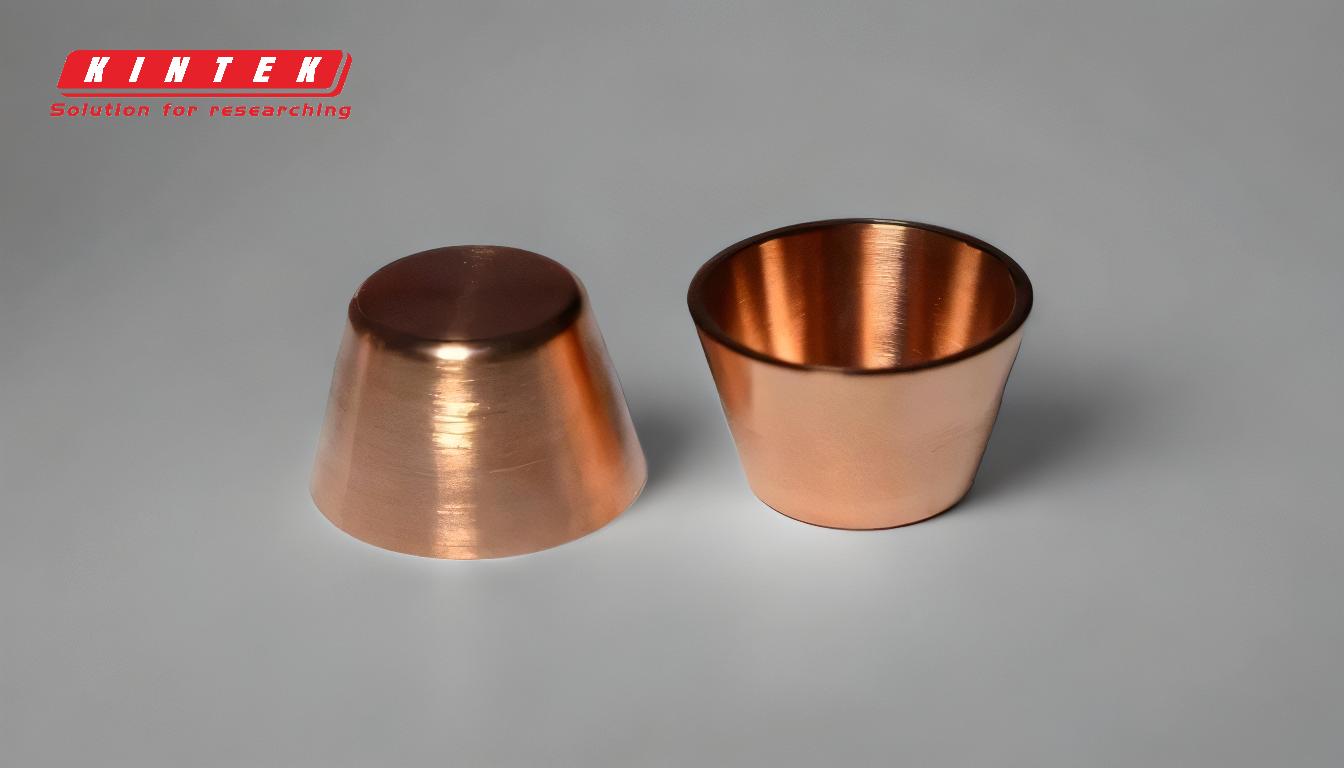
-
Small Deposition Area:
- IBD is limited by its small target area, which restricts the size of the films it can deposit. This makes it unsuitable for applications requiring large-area uniform films.
- The small target area also contributes to a lower deposition rate, further limiting its efficiency for large-scale production.
-
Low Deposition Rate:
- The effective deposition rate of IBD is generally low compared to other Physical Vapor Deposition (PVD) methods. This slow rate can increase production time and costs, making it less efficient for high-volume manufacturing.
- Even with advanced techniques like dual ion beam sputtering, the deposition rate remains a limiting factor, particularly for large-scale or industrial applications.
-
High Equipment and Operating Costs:
- IBD systems are complex and require sophisticated equipment, leading to high initial capital costs.
- The maintenance and operational costs are also significant, as the equipment demands precise calibration and frequent upkeep to maintain performance.
-
Complexity and Difficulty in Scaling Up:
- The complexity of IBD systems makes them challenging to scale up for larger production needs. This limits their applicability in industries where scalability is a priority.
- The high level of technical expertise required to operate and maintain IBD systems further complicates their use in large-scale or less specialized environments.
-
Unsuitability for Large-Area Uniform Films:
- Due to its small target area and low deposition rate, IBD is not ideal for applications requiring uniform film thickness over large surfaces. This limitation can be a significant drawback in industries like display manufacturing or large-scale optics.
-
Alternative Methods for Cost-Sensitive Applications:
- For projects where cost is a primary concern, alternative methods like ion-assisted deposition or magnetron sputtering may be more suitable. These methods offer higher deposition rates and lower costs, albeit with potentially less precision than IBD.
- However, for applications where tight control over film properties and high performance are critical, IBD remains the preferred choice despite its disadvantages.
In summary, while Ion Beam Deposition offers unparalleled precision and control, its disadvantages—such as small deposition area, low deposition rate, high costs, and complexity—make it less suitable for large-scale or cost-sensitive applications. Understanding these limitations is crucial for selecting the appropriate deposition method based on specific project requirements.
Summary Table:
Disadvantage | Description |
---|---|
Small Deposition Area | Limited target area restricts film size, unsuitable for large-area applications. |
Low Deposition Rate | Slower than other PVD methods, increasing production time and costs. |
High Equipment Costs | Complex systems with high initial and maintenance expenses. |
Difficulty in Scaling Up | Challenging to scale for large production due to system complexity. |
Unsuitable for Large Films | Not ideal for uniform film thickness over large surfaces. |
Alternative Methods | Cost-sensitive projects may prefer ion-assisted deposition or sputtering. |
Need help choosing the right deposition method? Contact our experts today for tailored solutions!