Ion beam sputtering (IBS) is a highly precise and versatile thin-film deposition technique, but it comes with several disadvantages that limit its applicability in certain scenarios. These drawbacks include changes to film stoichiometry, limited scalability for large surfaces, low deposition rates, high maintenance requirements, and process complexity. Understanding these limitations is crucial for determining whether IBS is suitable for specific applications, particularly when uniformity, scalability, or cost-effectiveness are key considerations.
Key Points Explained:
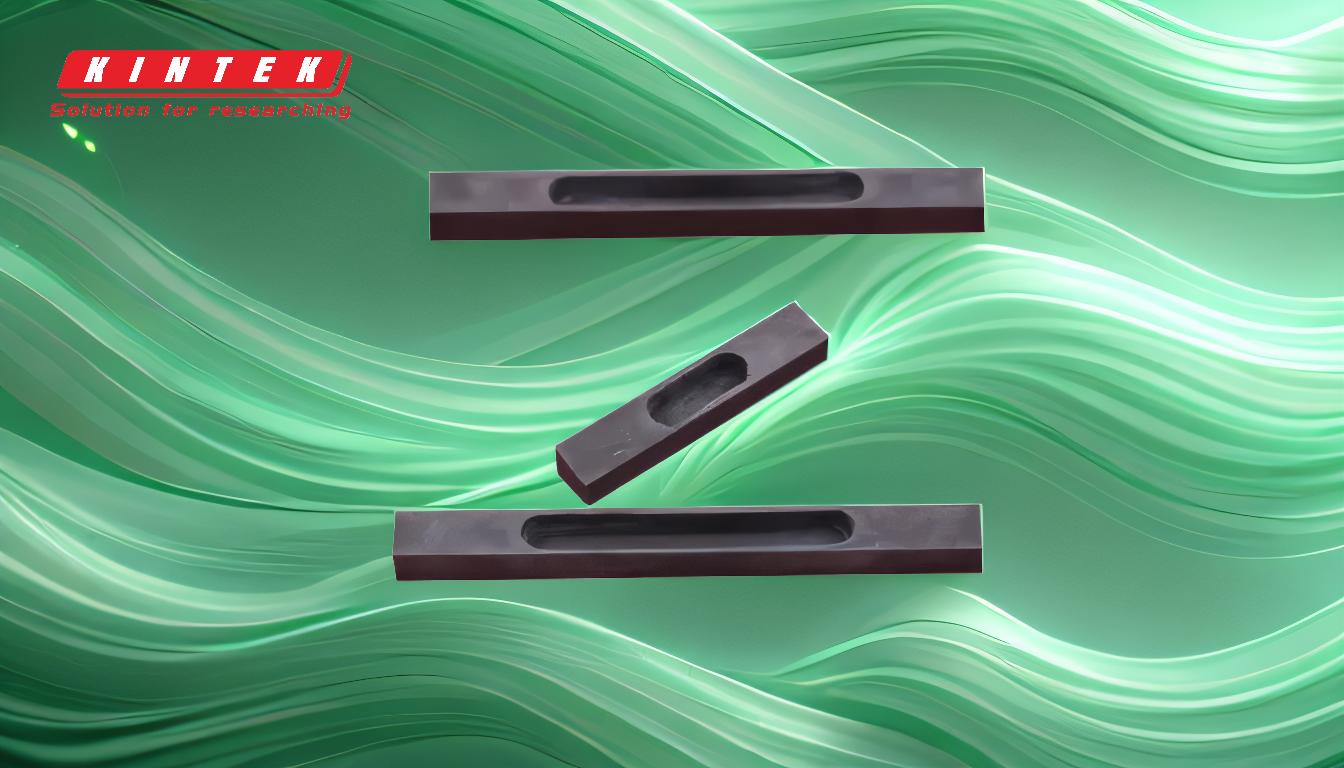
-
Changes to Film Stoichiometry
- Ion beam sputtering can alter the chemical composition and physical properties of the deposited film.
- When films are bombarded with ions like O2+ and Ar+, the process can lead to:
- Increased density of the film.
- Modifications to the crystal structure, which may affect the film's mechanical and optical properties.
- Decreased water permeability, which could be undesirable in applications requiring breathable or permeable coatings.
- These changes may compromise the intended functionality of the film, making IBS less suitable for applications where precise stoichiometry is critical.
-
Limited Scalability for Large Surfaces
- IBS is not ideal for coating large surfaces that require uniform film thickness.
- The target area in IBS is typically limited, which results in a low deposition rate.
- Even with dual ion beam sputtering, the target area may not be sufficient to achieve uniform coatings over large substrates.
- This limitation makes IBS less practical for industrial-scale applications where high throughput and large-area uniformity are essential.
-
Low Deposition Rate
- The deposition rate in IBS is generally lower compared to other thin-film deposition techniques.
- This is due to the relatively small target area and the precise nature of the process.
- A low deposition rate can increase production time and costs, making IBS less efficient for high-volume manufacturing.
-
High Maintenance Requirements
- IBS systems are complex and require regular maintenance to ensure optimal performance.
- The precision components, such as ion sources and vacuum systems, are prone to wear and tear, necessitating frequent servicing.
- High maintenance demands can increase operational costs and downtime, reducing the overall efficiency of the process.
-
Process Complexity
- IBS is a technically complex process that requires specialized knowledge and expertise to operate effectively.
- The setup and calibration of the system can be challenging, particularly for users unfamiliar with the technology.
- The complexity of the process can also make it difficult to scale up for industrial applications, where simplicity and ease of use are often prioritized.
-
Cost Considerations
- The high initial investment and operational costs associated with IBS can be prohibitive for some users.
- The need for advanced equipment, skilled personnel, and regular maintenance further adds to the overall expense.
- These cost factors may limit the adoption of IBS, especially in cost-sensitive industries.
In summary, while ion beam sputtering offers advantages such as precision control and superior film quality, its disadvantages—including changes to film stoichiometry, limited scalability, low deposition rates, high maintenance, process complexity, and cost—must be carefully weighed when selecting a deposition technique. These limitations make IBS more suitable for specialized applications where precision and quality are paramount, rather than large-scale or cost-sensitive projects.
Summary Table:
Disadvantage | Description |
---|---|
Changes to Film Stoichiometry | Alters chemical composition, density, and crystal structure, affecting properties. |
Limited Scalability | Not suitable for large surfaces; low deposition rates limit industrial use. |
Low Deposition Rate | Slower compared to other techniques, increasing production time and costs. |
High Maintenance Requirements | Complex systems require frequent servicing, raising operational costs. |
Process Complexity | Technically challenging, requiring specialized knowledge and expertise. |
High Costs | Expensive initial investment and operational expenses limit adoption. |
Want to learn more about ion beam sputtering and its alternatives? Contact our experts today for tailored advice!