Milling in the pharmaceutical industry, while essential for particle size reduction, has several disadvantages, particularly when dealing with heat-sensitive materials. Mechanical milling can introduce heat and shear-related anomalies, which may compromise the chemical integrity of pharmaceuticals. To mitigate these issues, alternative methods like jet mills and cryogenic grinding are employed. However, these solutions come with their own challenges and limitations. Below is a detailed exploration of the disadvantages of milling in the pharmaceutical industry.
Key Points Explained:
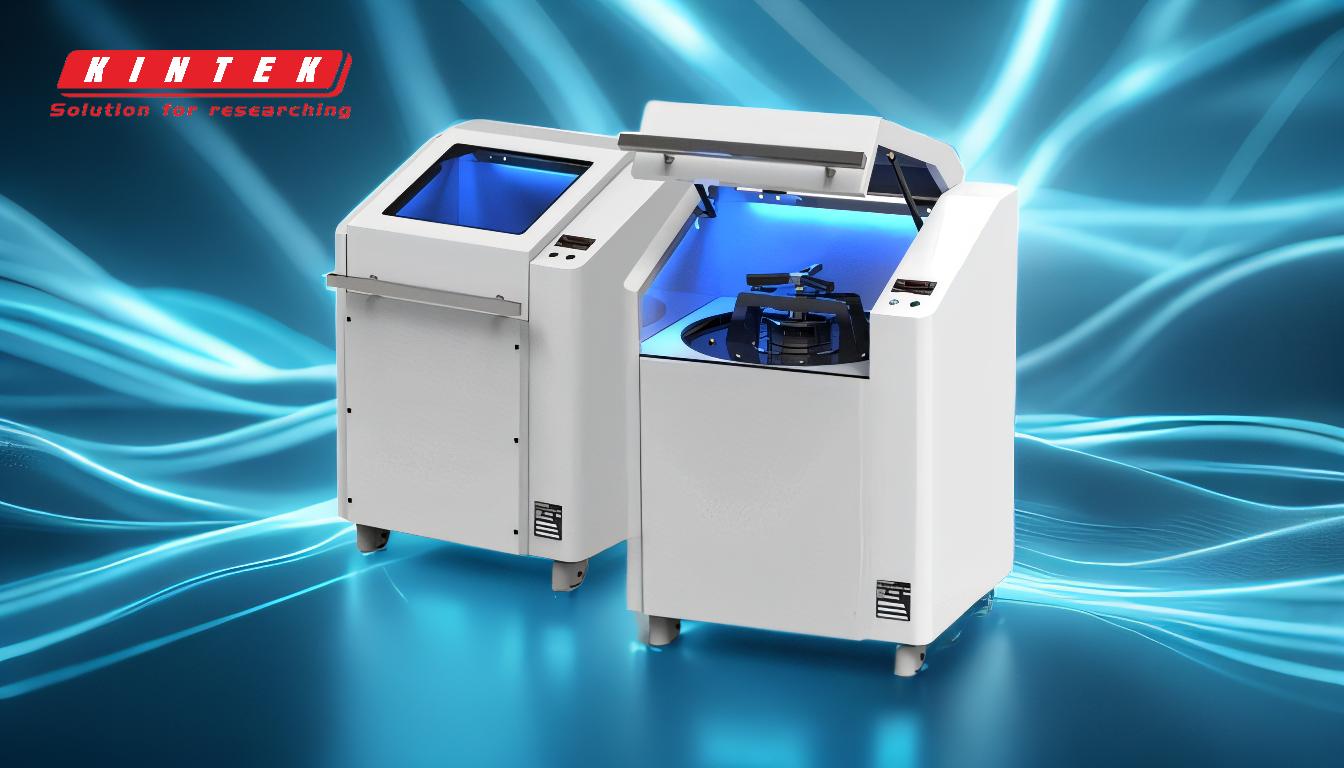
-
Heat Generation:
- Problem: Mechanical milling generates heat due to friction and impact forces. This heat can degrade heat-sensitive pharmaceutical compounds, leading to loss of efficacy or unwanted chemical reactions.
- Impact: For pharmaceuticals, maintaining the chemical integrity is crucial. Any degradation can render the product ineffective or even harmful.
- Example: Active pharmaceutical ingredients (APIs) that are thermolabile can degrade at elevated temperatures, reducing their therapeutic efficacy.
-
Shear-Related Anomalies:
- Problem: Shear forces during milling can cause structural changes in the material. This can lead to the formation of amorphous regions or even chemical degradation.
- Impact: Shear-induced changes can alter the bioavailability and stability of the pharmaceutical product.
- Example: Polymorphic transformations can occur, where the drug substance changes its crystalline form, affecting its dissolution rate and bioavailability.
-
Contamination Risks:
- Problem: Mechanical milling can introduce contaminants from the milling equipment, such as metal particles from wear and tear.
- Impact: Contaminants can pose serious health risks and lead to product recalls.
- Example: Metal contamination can be particularly dangerous in injectable pharmaceuticals, where even small particles can cause significant harm.
-
Particle Size Distribution Issues:
- Problem: Achieving a uniform particle size distribution can be challenging with mechanical milling. Over-milling can lead to fines, while under-milling can result in larger particles.
- Impact: Inconsistent particle size can affect the drug's dissolution rate, bioavailability, and overall performance.
- Example: A wide particle size distribution can lead to inconsistent dosing in solid dosage forms like tablets.
-
Energy Consumption:
- Problem: Mechanical milling is energy-intensive, requiring significant power to achieve the desired particle size reduction.
- Impact: High energy consumption increases operational costs and has a larger environmental footprint.
- Example: Continuous milling operations can lead to substantial energy bills, impacting the overall cost-effectiveness of the manufacturing process.
-
Equipment Wear and Maintenance:
- Problem: The mechanical components of milling equipment are subject to wear and tear, necessitating frequent maintenance and replacement.
- Impact: Downtime for maintenance can disrupt production schedules and increase operational costs.
- Example: Frequent replacement of milling blades or screens can be costly and time-consuming.
-
Limited Applicability for Certain Materials:
- Problem: Some pharmaceutical materials are not suitable for mechanical milling due to their sensitivity to heat or shear.
- Impact: Alternative milling methods must be employed, which may not be as efficient or cost-effective.
- Example: Biopharmaceuticals, which are often proteins or peptides, may require specialized milling techniques to avoid denaturation.
-
Noise and Vibration:
- Problem: Mechanical milling operations can generate significant noise and vibration, which can be disruptive and harmful to operators.
- Impact: Prolonged exposure to high noise levels can lead to hearing loss, and vibrations can cause discomfort or even injury.
- Example: Operators working in close proximity to milling equipment may require protective gear, adding to operational complexity.
-
Regulatory Challenges:
- Problem: Ensuring compliance with stringent regulatory requirements for pharmaceutical manufacturing can be challenging with mechanical milling.
- Impact: Any deviation from regulatory standards can lead to product recalls, legal issues, and damage to the company’s reputation.
- Example: Regulatory bodies like the FDA require thorough documentation and validation of milling processes, which can be resource-intensive.
-
Alternative Methods and Their Limitations:
- Jet Mills: While jet mills reduce particle size through high-speed collisions without generating heat, they can be less efficient for certain materials and may require specialized equipment.
- Cryogenic Grinding: Freezing materials before milling can maintain chemical integrity, but the process is energy-intensive and may not be suitable for all pharmaceuticals.
- Impact: These alternative methods, while effective in mitigating some disadvantages, come with their own set of challenges, including higher costs and operational complexities.
In summary, while milling is a critical process in the pharmaceutical industry, it comes with several disadvantages, particularly related to heat generation, shear forces, contamination, and energy consumption. These challenges necessitate the use of alternative methods like jet mills and cryogenic grinding, which, while effective, also have their own limitations. Understanding these disadvantages is crucial for pharmaceutical manufacturers to optimize their processes and ensure the production of safe and effective drugs.
Summary Table:
Disadvantage | Problem | Impact | Example |
---|---|---|---|
Heat Generation | Friction and impact forces generate heat, degrading heat-sensitive compounds. | Loss of efficacy or unwanted chemical reactions. | Thermolabile APIs degrade at elevated temperatures. |
Shear-Related Anomalies | Shear forces cause structural changes or chemical degradation. | Alters bioavailability and stability. | Polymorphic transformations affect dissolution rates. |
Contamination Risks | Metal particles from equipment wear contaminate products. | Health risks and product recalls. | Metal contamination in injectable pharmaceuticals. |
Particle Size Distribution | Inconsistent particle sizes due to over- or under-milling. | Affects dissolution rate, bioavailability, and dosing consistency. | Wide particle size distribution in tablets. |
Energy Consumption | High energy usage for particle size reduction. | Increased operational costs and environmental impact. | Continuous milling leads to high energy bills. |
Equipment Wear and Maintenance | Frequent wear and tear require maintenance. | Downtime disrupts production and increases costs. | Frequent replacement of milling blades or screens. |
Limited Applicability | Some materials are unsuitable due to heat or shear sensitivity. | Requires alternative, less efficient methods. | Biopharmaceuticals may denature during milling. |
Noise and Vibration | High noise and vibration levels harm operators. | Hearing loss, discomfort, or injury. | Operators require protective gear near milling equipment. |
Regulatory Challenges | Compliance with strict manufacturing standards is difficult. | Product recalls, legal issues, and reputational damage. | FDA requires extensive documentation and validation. |
Alternative Methods | Jet mills and cryogenic grinding have their own limitations. | Higher costs and operational complexities. | Cryogenic grinding is energy-intensive and not universally applicable. |
Struggling with milling challenges in your pharmaceutical processes? Contact our experts today to explore tailored solutions!