XRF (X-ray fluorescence) analysis is a powerful technique for material analysis, but it is not without its potential errors. These errors can arise from various sources, including instrumental limitations, sample preparation, and environmental factors. Understanding these errors is crucial for ensuring accurate and reliable results. Advances in AI, machine learning, and cloud computing are helping to mitigate some of these errors by improving calibration, data processing, and analysis efficiency. However, it is still important to be aware of the common errors and their causes.
Key Points Explained:
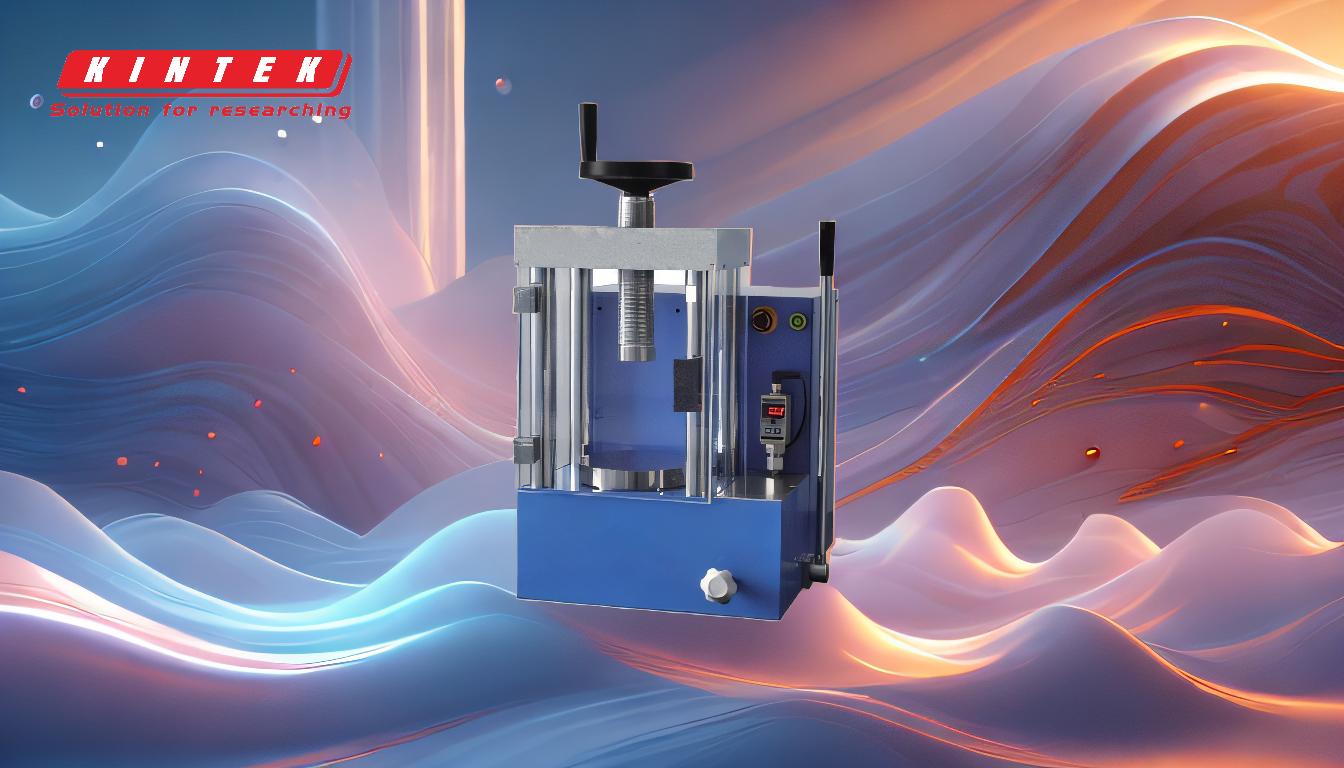
-
Instrumental Errors:
- Detector Limitations: The sensitivity and resolution of the XRF detector can impact the accuracy of the analysis. High-resolution detectors are better at distinguishing between closely spaced X-ray peaks, reducing the chance of misidentification.
- Source Instability: The X-ray tube or radioactive source used in XRF can degrade over time, leading to fluctuations in the intensity of the emitted X-rays. This can cause inconsistencies in the results.
- Calibration Drift: Over time, the calibration of the XRF instrument can drift due to changes in temperature, humidity, or other environmental factors. Regular recalibration is necessary to maintain accuracy.
-
Sample-Related Errors:
- Sample Heterogeneity: If the sample is not homogeneous, the XRF analysis may not be representative of the entire sample. This is particularly problematic for materials with varying compositions or layered structures.
- Surface Roughness: The surface condition of the sample can affect the intensity of the X-ray fluorescence signal. Rough or uneven surfaces can scatter X-rays, leading to inaccurate readings.
- Sample Thickness: For thin samples, the X-rays may penetrate through the material, leading to incomplete detection of elements. Conversely, for very thick samples, the X-rays may not penetrate deeply enough, causing surface elements to be overrepresented.
-
Matrix Effects:
- Absorption and Enhancement: The presence of certain elements in the sample can absorb or enhance the X-ray fluorescence of other elements, leading to errors in quantification. This is known as the matrix effect and can be corrected using advanced algorithms and calibration standards.
- Interelement Interference: Elements with similar X-ray emission lines can interfere with each other, making it difficult to accurately identify and quantify individual elements. This requires careful selection of analytical lines and the use of sophisticated software to deconvolute overlapping peaks.
-
Environmental and Operational Errors:
- Temperature and Humidity: Changes in temperature and humidity can affect the performance of the XRF instrument and the stability of the sample. For example, high humidity can cause condensation on the detector window, reducing sensitivity.
- Operator Error: Incorrect handling of the sample, improper calibration, or misalignment of the instrument can lead to errors in the analysis. Proper training and adherence to standard operating procedures are essential to minimize these errors.
-
Advancements in Technology:
- AI and Machine Learning: These technologies are being used to improve the accuracy of XRF analysis by automating calibration, correcting for matrix effects, and identifying patterns in the data that may indicate errors. For example, machine learning algorithms can be trained to recognize and correct for interelement interference.
- Cloud Computing: Cloud-based platforms allow for real-time data sharing and analysis, enabling more efficient collaboration and faster identification of errors. They also provide access to large databases of reference materials and calibration standards, improving the accuracy of the analysis.
In conclusion, while XRF analysis is a robust and efficient method for material analysis, it is important to be aware of potential errors and their sources. Advances in technology, such as AI, machine learning, and cloud computing, are helping to reduce these errors, but careful attention to sample preparation, instrument calibration, and environmental conditions remains essential for achieving accurate results.
Summary Table:
Error Type | Key Causes | Mitigation Strategies |
---|---|---|
Instrumental Errors | Detector limitations, source instability, calibration drift | Use high-resolution detectors, regular recalibration, and monitor source stability |
Sample-Related Errors | Sample heterogeneity, surface roughness, sample thickness | Ensure homogeneous samples, polish surfaces, and optimize sample thickness |
Matrix Effects | Absorption and enhancement, interelement interference | Use advanced algorithms, calibration standards, and deconvolution software |
Environmental Errors | Temperature and humidity changes, operator error | Control lab conditions, provide proper training, and follow standard procedures |
Tech Advancements | AI, machine learning, cloud computing | Automate calibration, correct matrix effects, and leverage cloud-based data analysis |
Ensure accurate XRF analysis results—contact our experts today for tailored solutions and support!