Molding is a critical process in manufacturing, where materials are shaped into desired forms using molds. The quality and efficiency of molding are influenced by several factors, including material properties, mold design, processing conditions, and environmental factors. Understanding these factors is essential for optimizing the molding process, reducing defects, and ensuring the production of high-quality parts. Key considerations include the type of material used, its flow characteristics, mold temperature, pressure, cooling rate, and the design of the mold itself. By carefully controlling these variables, manufacturers can achieve consistent results and minimize waste.
Key Points Explained:
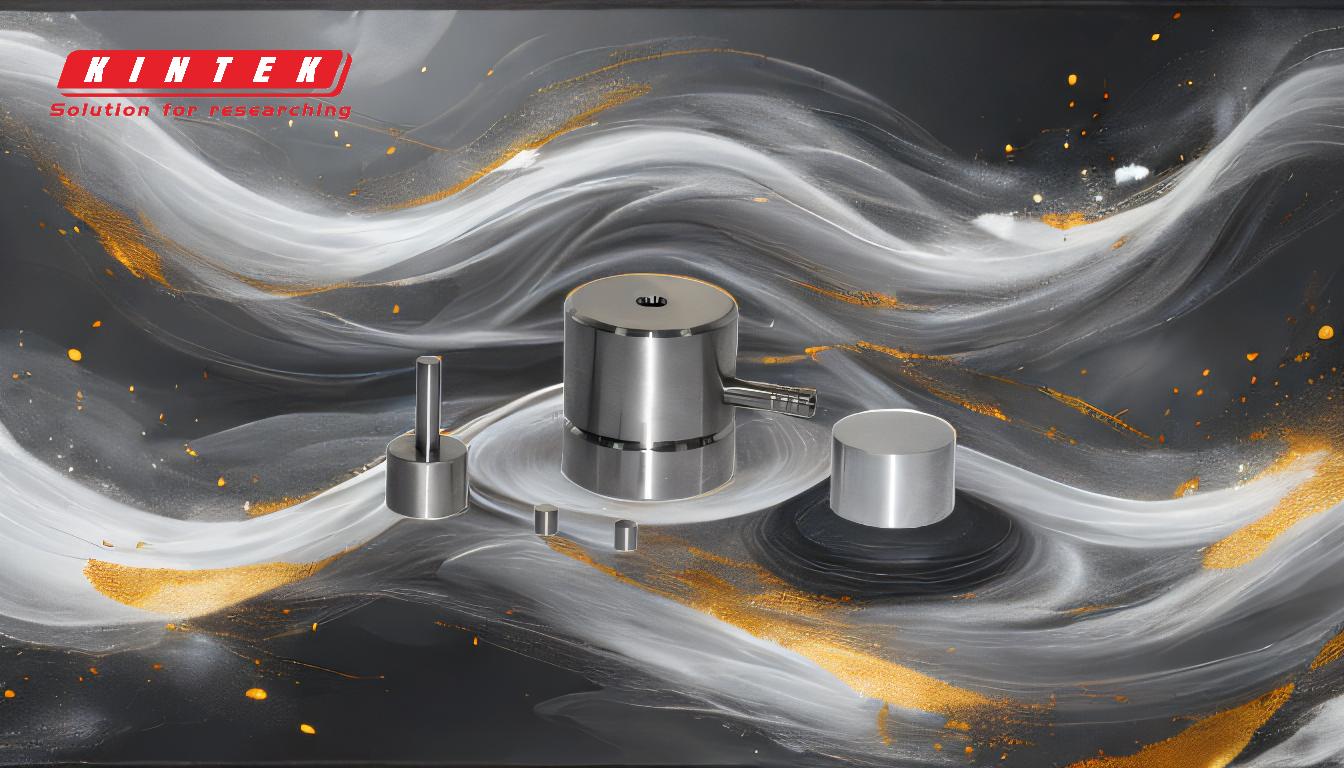
-
Material Properties:
- The type of material used in molding significantly impacts the process. Factors such as viscosity, thermal conductivity, and shrinkage rate play a crucial role in determining how the material flows and solidifies in the mold.
- For example, materials with high viscosity may require higher injection pressures, while those with low thermal conductivity may need longer cooling times.
- The material's ability to withstand temperature changes and its compatibility with the mold surface also affect the final product's quality.
-
Mold Design:
- The design of the mold is a critical factor in the molding process. This includes the shape, size, and complexity of the mold, as well as the placement of gates, vents, and cooling channels.
- Proper mold design ensures uniform filling, minimizes defects like air traps or warping, and facilitates easy ejection of the finished part.
- The choice of mold material, such as steel or aluminum, also affects heat transfer and durability during the molding process.
-
Processing Conditions:
- Processing conditions such as temperature, pressure, and injection speed are vital for achieving optimal results.
- Mold temperature affects the material's flow and cooling rate. Too high a temperature can cause defects like warping, while too low a temperature may result in incomplete filling.
- Injection pressure and speed must be carefully controlled to ensure the material fills the mold evenly without causing stress or defects.
- Cooling time is another critical factor, as it determines the part's dimensional stability and surface finish.
-
Environmental Factors:
- Environmental conditions, such as humidity and ambient temperature, can also influence the molding process.
- High humidity levels may affect the material's properties, while fluctuations in ambient temperature can impact mold temperature and cooling rates.
- Proper control of the manufacturing environment helps maintain consistency and reduces the risk of defects.
-
Operator Skill and Maintenance:
- The skill and experience of the operator play a significant role in the success of the molding process.
- Regular maintenance of the molding equipment, including cleaning and lubrication, ensures smooth operation and prolongs the life of the machinery.
- Proper training and adherence to best practices help minimize errors and improve overall efficiency.
By understanding and controlling these factors, manufacturers can optimize the molding process, reduce defects, and produce high-quality parts consistently. Each factor interrelates with the others, making it essential to consider the entire system when making adjustments or improvements.
Summary Table:
Factor | Key Considerations |
---|---|
Material Properties | Viscosity, thermal conductivity, shrinkage rate, temperature resistance |
Mold Design | Shape, size, complexity, gate/vent placement, cooling channels, mold material choice |
Processing Conditions | Temperature, pressure, injection speed, cooling time |
Environmental Factors | Humidity, ambient temperature, environmental control |
Operator Skill | Training, experience, adherence to best practices |
Maintenance | Regular cleaning, lubrication, and equipment upkeep |
Ready to optimize your molding process? Contact our experts today for tailored solutions!