The sieving method is influenced by several factors that determine its accuracy and efficiency. These factors include the characteristics of the material being sieved, such as particle size, resistance to agglomeration, and susceptibility to static electricity. Environmental conditions like humidity also play a significant role, as dry conditions can cause particles to adhere to the sieve due to electrostatic charges. Additionally, the design and operation of the sieving equipment, including the motion of the sieve and the filling capacity of the machine, are critical for achieving reliable results. Understanding these factors helps in selecting the appropriate sieving method and equipment for specific applications.
Key Points Explained:
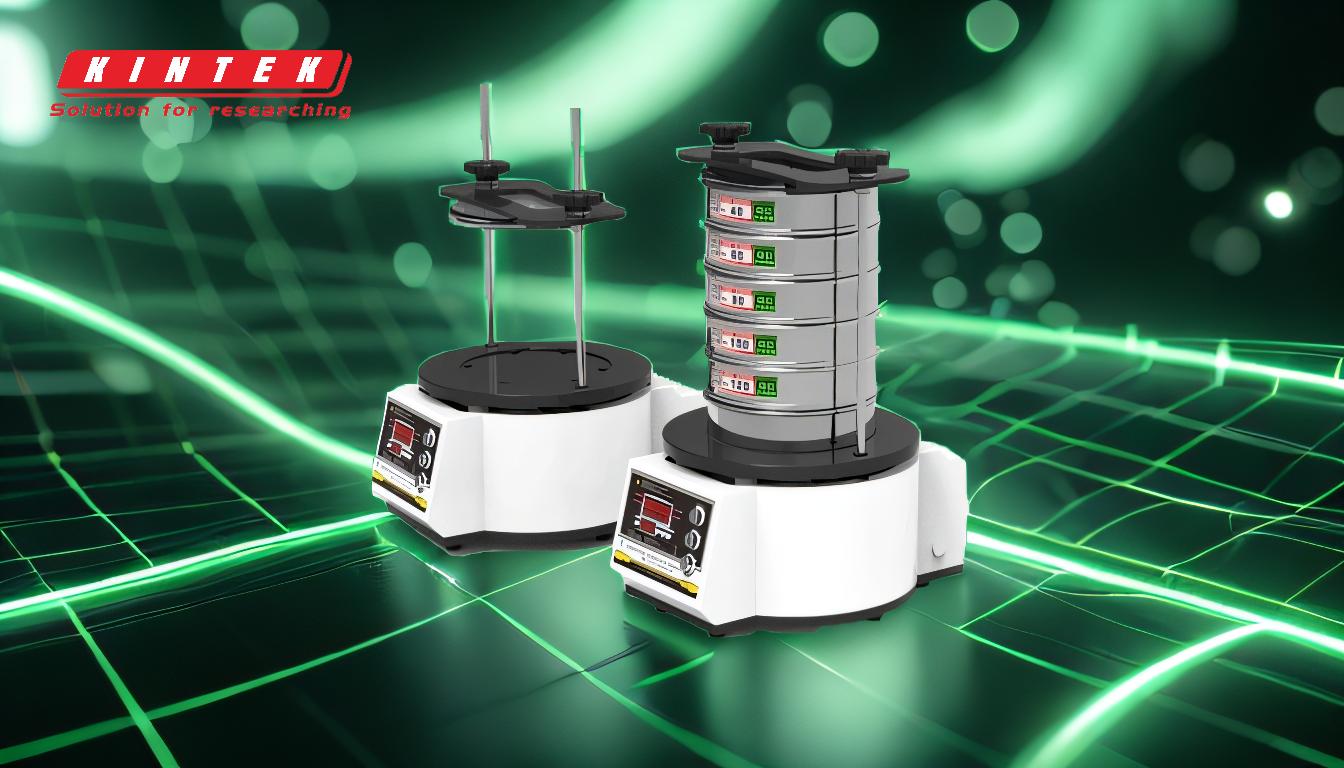
-
Material Characteristics:
- Particle Size: The minimum size of particles to be separated is crucial. Smaller particles may require finer mesh sieves, while larger particles need coarser meshes.
- Resistance to Agglomeration: Materials that tend to clump together can hinder the sieving process. Proper pre-treatment or the use of anti-agglomeration agents may be necessary.
- Static Electricity: Materials prone to static electricity can cause particles to stick to the sieve or each other, reducing the efficiency of the sieving process. This is particularly problematic in dry conditions.
-
Environmental Conditions:
- Humidity: High humidity can reduce static electricity, making it easier to sieve fine powders. Conversely, low humidity can increase static charges, causing particles to adhere to the sieve and each other.
- Temperature: Extreme temperatures can affect the material's properties and the sieving process. For example, high temperatures might cause materials to become more pliable or sticky.
-
Sieving Equipment Design and Operation:
- Sieve Motion: The effectiveness of sieving depends on the motion of the sieve. Vertical or horizontal motion ensures that particles are adequately agitated, allowing smaller particles to pass through the mesh while larger particles remain on the surface.
- Filling Capacity: The amount of material loaded into the sieve shaker must match the machine's capacity. Overloading can reduce efficiency, while underloading may not provide enough material for accurate separation.
- Compatibility: The sieving machine should be compatible with the specific requirements of the material and the application. This includes the type of sieve mesh, the size of the sieve, and the overall design of the machine.
-
Pre-Treatment of Materials:
- Drying or Moistening: Depending on the material and environmental conditions, pre-treatment such as drying or moistening may be necessary to optimize the sieving process.
- De-agglomeration: For materials that tend to clump, mechanical or chemical de-agglomeration methods can be employed to ensure a more uniform particle size distribution before sieving.
-
Maintenance and Calibration of Equipment:
- Regular Maintenance: Keeping the sieving equipment in good condition is essential for consistent performance. This includes cleaning the sieves, checking for wear and tear, and replacing damaged components.
- Calibration: Regular calibration of the sieving machine ensures that it operates within the specified parameters, providing accurate and reliable results.
By considering these factors, one can optimize the sieving process to achieve accurate and efficient separation of particles based on size. This is particularly important in industries where precise particle size distribution is critical, such as pharmaceuticals, food processing, and construction materials.
Summary Table:
Factor | Key Considerations |
---|---|
Material Characteristics | - Particle size: Finer or coarser mesh required. |
- Resistance to agglomeration: Pre-treatment may be needed. | |
- Static electricity: Dry conditions can cause particle adhesion. | |
Environmental Conditions | - Humidity: High humidity reduces static; low humidity increases it. |
- Temperature: Extreme temperatures affect material properties. | |
Equipment Design | - Sieve motion: Vertical or horizontal agitation improves separation. |
- Filling capacity: Overloading or underloading reduces efficiency. | |
- Compatibility: Match equipment to material and application needs. | |
Pre-Treatment | - Drying or moistening: Adjust material moisture for optimal sieving. |
- De-agglomeration: Ensure uniform particle size distribution. | |
Maintenance | - Regular cleaning and calibration ensure consistent performance. |
Need help optimizing your sieving process? Contact our experts today for tailored solutions!