The quality of powder in powder metallurgy is influenced by several factors, including the material properties of the metal powder, the particle size and distribution, phase composition, grain size, and the manufacturing process itself. These factors collectively determine the hardness, tensile strength, impact toughness, fatigue strength, and corrosion resistance of the final product. Understanding and controlling these variables is crucial for producing high-quality components that meet specific application requirements.
Key Points Explained:
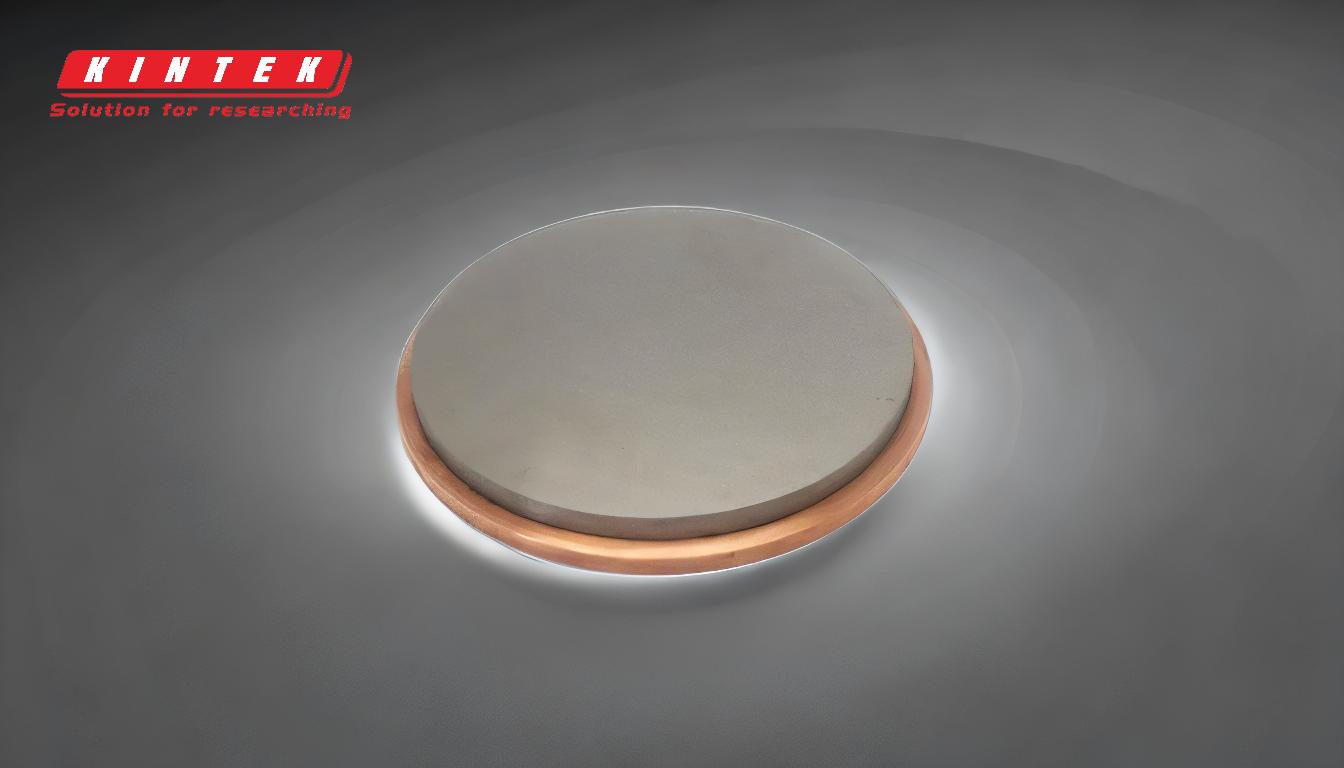
-
Material Properties of the Metal Powder:
- Corrosion Resistance: The ability of the metal to resist degradation due to chemical reactions with the environment. This is crucial for parts exposed to harsh conditions.
- Hardness: Determines the resistance of the material to deformation. Higher hardness is often required for wear-resistant components.
- Tensile Strength: The maximum stress that a material can withstand while being stretched or pulled before breaking. This is critical for structural components.
- Impact Toughness: The ability of the material to absorb energy and plastically deform without fracturing. Important for parts subjected to sudden impacts.
- Fatigue Strength: The ability of the material to withstand repeated loading and unloading without failure. Essential for components experiencing cyclic stresses.
-
Particle Size and Distribution:
- Particle Size: Smaller particles generally lead to better packing density and more uniform sintering, which can improve the mechanical properties of the final product.
- Particle Distribution: A narrow particle size distribution ensures more consistent compaction and sintering behavior, leading to more predictable mechanical properties.
-
Phase Composition:
- Phase Stability: The presence of different phases in the powder can affect the hardness and melt properties, which in turn influence the pressing efficiency and sintering behavior.
- Phase Transformation: Changes in phase composition during processing can lead to variations in the final properties of the part, such as hardness and strength.
-
Grain Size:
- Grain Size Control: Fine grain sizes generally lead to higher strength and toughness due to the Hall-Petch relationship, which states that smaller grains result in higher yield strength.
- Grain Growth: During sintering, grain growth can occur, which may reduce the strength of the material. Controlling the sintering conditions is essential to maintain the desired grain size.
-
Manufacturing Process:
- Compaction: The process of pressing the powder into a desired shape. The uniformity of compaction affects the density and mechanical properties of the final part.
- Sintering: The process of heating the compacted powder to a temperature below its melting point to bond the particles together. The sintering temperature and time must be carefully controlled to achieve the desired properties.
- Isostatic Pressing: This method applies uniform pressure from all directions, leading to more uniform density and better mechanical properties in the final product.
-
Environmental and Operational Factors:
- Atmosphere Control: The sintering atmosphere (e.g., inert gas, vacuum) can affect the oxidation state of the powder and the final properties of the part.
- Temperature Control: Precise control of the sintering temperature is crucial to avoid defects such as warping or cracking and to achieve the desired phase composition and grain size.
By carefully considering and controlling these factors, manufacturers can produce high-quality powder metallurgy components that meet the specific requirements of their applications.
Summary Table:
Factor | Description |
---|---|
Material Properties | Includes corrosion resistance, hardness, tensile strength, impact toughness, and fatigue strength. |
Particle Size & Distribution | Smaller particles and narrow distribution improve packing density and sintering uniformity. |
Phase Composition | Affects hardness, melt properties, and phase transformation during processing. |
Grain Size | Fine grains enhance strength and toughness; controlled sintering prevents grain growth. |
Manufacturing Process | Compaction, sintering, and isostatic pressing influence density and mechanical properties. |
Environmental Factors | Atmosphere and temperature control during sintering are crucial for final properties. |
Optimize your powder metallurgy process for superior results—contact our experts today!