Ball mills are widely used in grinding and milling operations, but they come with several limitations that can affect their efficiency, practicality, and suitability for certain applications. These limitations include issues related to energy consumption, operational noise, material handling, contamination risks, and physical constraints. Understanding these drawbacks is crucial for equipment purchasers to make informed decisions and explore alternative solutions when necessary.
Key Points Explained:
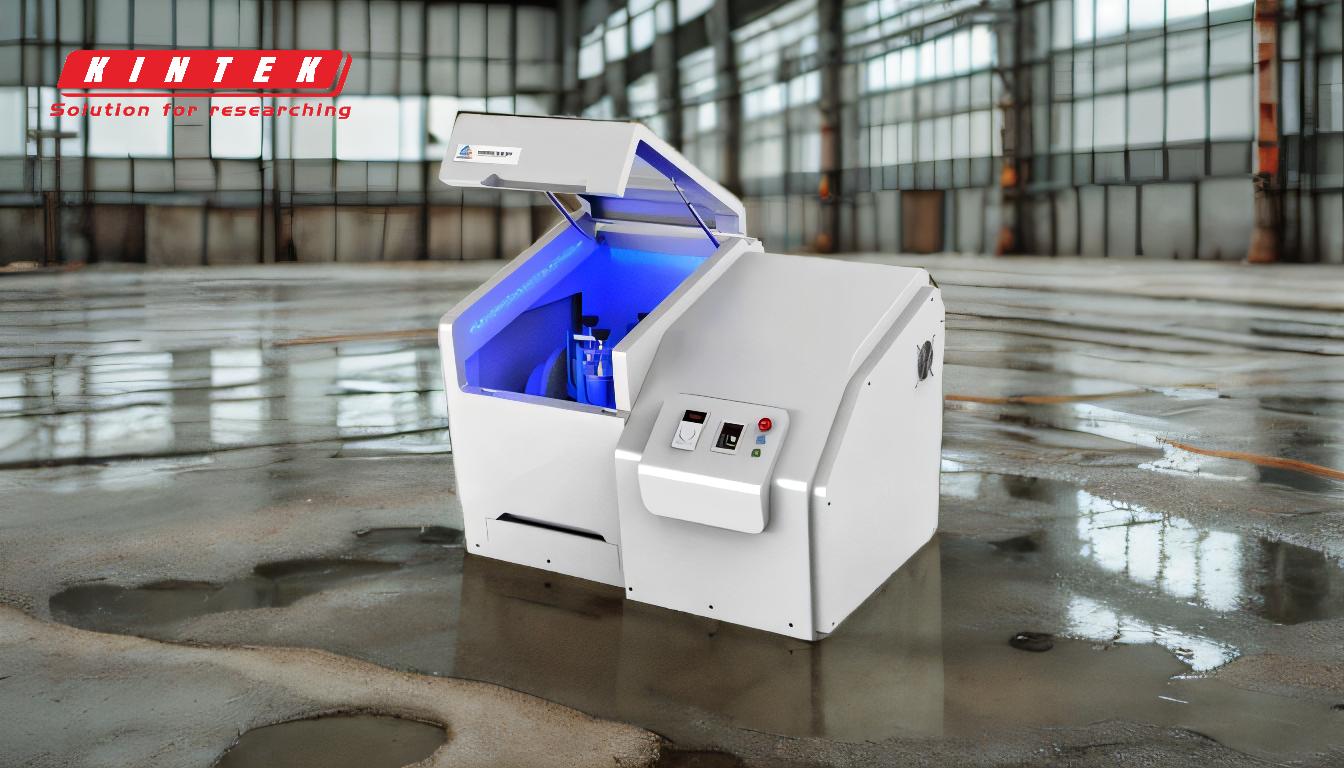
-
High Specific Energy Consumption:
- Ball mills are known for their high energy consumption, primarily due to the wear and tear of grinding balls and the mill's internal armor. This wear results from the constant friction between the balls and the material being ground, as well as the heat generated during the process. The energy required to overcome these factors makes ball mills less efficient compared to other grinding technologies.
- Implications for Purchasers: High energy consumption translates to increased operational costs. Buyers should consider the long-term energy expenses and explore energy-efficient alternatives if cost-effectiveness is a priority.
-
Noise and Vibrations:
- Ball mills produce significant noise and vibrations during operation, which can be disruptive and require additional measures to mitigate. While the use of rubber balls can reduce noise to some extent, the overall noise level remains a concern in many industrial settings.
- Implications for Purchasers: Noise pollution can affect workplace safety and compliance with environmental regulations. Purchasers may need to invest in soundproofing or noise reduction technologies, adding to the overall cost.
-
Slow Processing Speed:
- Ball mills are generally slower compared to other grinding methods. The grinding process can take a considerable amount of time, especially when fine particles are required. This slow speed can be a bottleneck in high-throughput operations.
- Implications for Purchasers: If time efficiency is critical, buyers should evaluate whether the slower processing speed of ball mills aligns with their production timelines or if faster alternatives are more suitable.
-
Inability to Handle Certain Materials:
- Ball mills struggle with soft, tacky, or fibrous materials, which can clog the mill or fail to grind effectively. This limitation restricts the versatility of ball mills in handling a wide range of materials.
- Implications for Purchasers: If the intended application involves grinding such materials, buyers should consider alternative equipment like hammer mills or specialized grinders designed for these materials.
-
Wear and Contamination Risks:
- The internal components of ball mills, such as the grinding balls and cylinder walls, are subject to wear over time. This wear can lead to contamination of the ground material, which is particularly problematic in industries requiring high purity, such as pharmaceuticals or food processing.
- Implications for Purchasers: Regular maintenance and replacement of worn parts are necessary to minimize contamination risks. Buyers should factor in the cost of maintenance and potential downtime when evaluating ball mills.
-
Limited Capacity for Large Quantities:
- Ball mills have a limited capacity for handling large quantities of material. This limitation can be a significant drawback in industries requiring bulk processing.
- Implications for Purchasers: For large-scale operations, buyers may need to invest in multiple ball mills or consider alternative equipment with higher throughput capabilities.
-
Unhandiness and Large Weight:
- Ball mills are often bulky and heavy, making them difficult to transport, install, and relocate. This can be a logistical challenge, especially in facilities with space constraints or those requiring frequent equipment reconfiguration.
- Implications for Purchasers: The physical size and weight of ball mills may necessitate additional infrastructure or handling equipment, adding to the overall cost and complexity of the setup.
Conclusion:
While ball mills are effective for many grinding applications, their limitations—such as high energy consumption, noise, slow processing speed, material handling constraints, contamination risks, and physical bulkiness—should be carefully considered. Equipment purchasers should weigh these drawbacks against their specific operational needs and explore alternative grinding technologies if necessary. Understanding these limitations ensures that the chosen equipment aligns with both production goals and cost considerations.
Summary Table:
Limitation | Description | Implications for Purchasers |
---|---|---|
High Specific Energy Consumption | High energy use due to wear and tear of grinding balls and internal armor. | Increased operational costs; consider energy-efficient alternatives. |
Noise and Vibrations | Significant noise and vibrations during operation. | Requires soundproofing or noise reduction technologies; adds to costs. |
Slow Processing Speed | Slower grinding compared to other methods; time-consuming for fine particles. | May not align with high-throughput production timelines; evaluate faster alternatives. |
Inability to Handle Certain Materials | Struggles with soft, tacky, or fibrous materials. | Consider alternative equipment like hammer mills for such materials. |
Wear and Contamination Risks | Internal wear leads to material contamination; problematic for high-purity industries. | Regular maintenance and part replacement required; adds to costs and downtime. |
Limited Capacity for Large Quantities | Limited throughput; unsuitable for bulk processing. | May need multiple units or higher-capacity alternatives for large-scale operations. |
Unhandiness and Large Weight | Bulky and heavy; difficult to transport, install, and relocate. | Requires additional infrastructure or handling equipment; increases setup complexity and cost. |
Need help choosing the right grinding equipment? Contact our experts today to find the best solution for your needs!