Ball milling is a widely used method for material processing, particularly in nanoparticle synthesis and mechanical alloying. While it offers advantages such as cost-effectiveness, ease of operation, and the ability to introduce crystal defects, it also has significant limitations. These include issues related to material properties, equipment wear, energy consumption, thermal damage, noise, and contamination. Understanding these limitations is crucial for selecting the appropriate milling method for specific applications, especially in industries like pharmaceuticals, food processing, and advanced materials.
Key Points Explained:
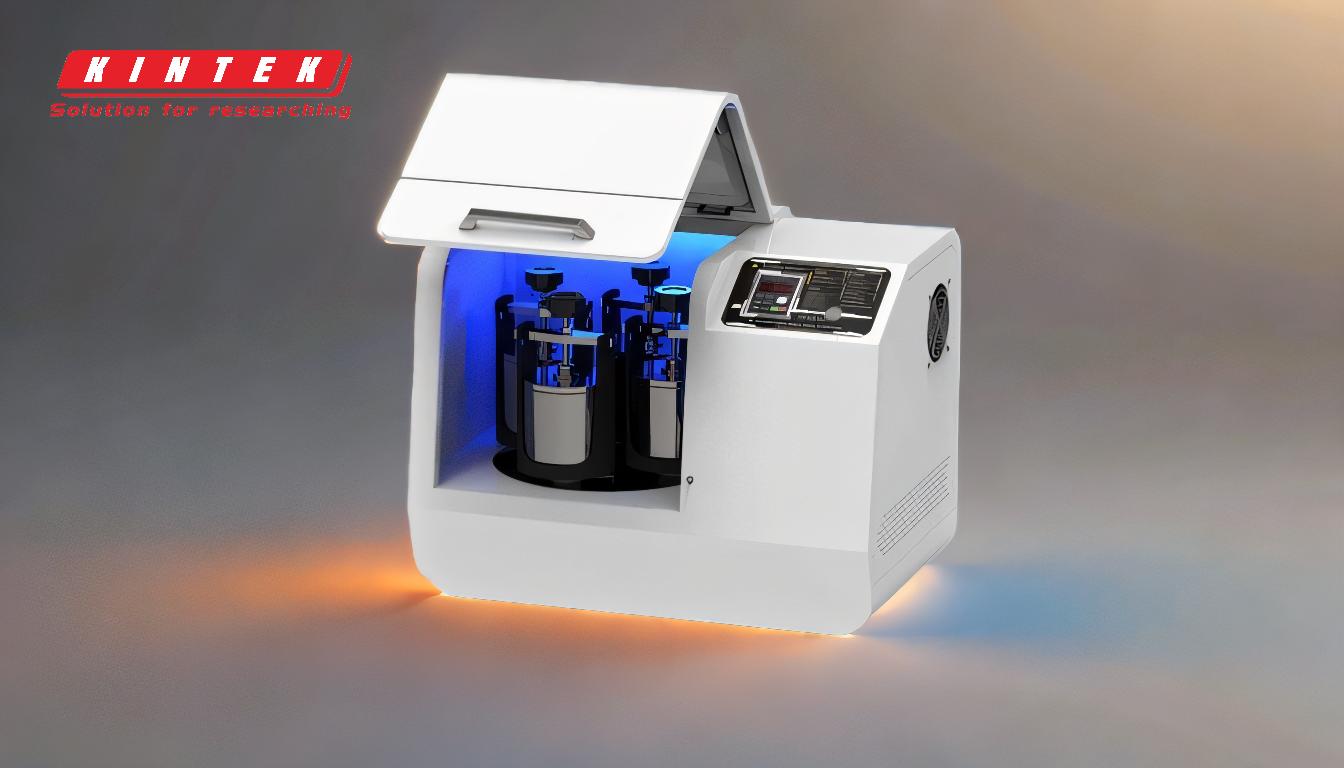
-
Material Limitations:
- Soft, Tacky, and Fibrous Materials: Ball milling is ineffective for reducing the size of soft, tacky, or fibrous materials. These materials tend to stick to the grinding media or the walls of the milling chamber, reducing efficiency and potentially clogging the equipment.
- Heat-Sensitive Materials: The process generates heat due to friction and impact, which can damage heat-sensitive materials like pharmaceuticals and food products. This thermal degradation can alter the chemical and physical properties of the materials, rendering them unsuitable for their intended use.
-
Equipment Wear and Maintenance:
- High Wear Rates: The friction between the grinding media (balls) and the material being milled leads to significant wear of the milling components. This wear necessitates frequent replacement of parts, increasing maintenance costs and downtime.
- Contamination Risks: Wear inside the milling cylinders can introduce contaminants into the material being processed. This is particularly problematic in industries where purity is critical, such as pharmaceuticals and electronics.
-
Energy Consumption:
- High Energy Requirements: Ball milling is an energy-intensive process. The grinding process consumes a large amount of energy, making it less efficient compared to other milling methods like jet milling or cryogenic grinding.
- Energy Management: Effective energy management is crucial to mitigate the high energy consumption, but this can add complexity and cost to the process.
-
Thermal Damage:
- Heat Generation: The high-speed rotation and impact of the grinding media generate significant heat. This can cause thermal damage to the materials being milled, affecting their quality and performance.
- Mitigation Strategies: While some strategies, like using inert atmospheres or cooling systems, can mitigate thermal damage, they add to the complexity and cost of the process.
-
Noise and Vibrations:
- Loud Noise: The operation of ball mills produces loud noise due to the high-speed rotation of the equipment and the impact of the grinding media. This can be a significant issue in environments where noise control is important.
- Vibrations: Ball mills produce strong vibrations, which can affect the stability of the equipment and the quality of the milled product. While rubber balls can reduce some of the noise and vibration, they do not eliminate the problem entirely.
-
Product Quality Issues:
- Polydisperse Size Distributions: Ball milling often results in a wide range of particle sizes (polydispersity), which can be undesirable for applications requiring uniform particle sizes.
- Partially Amorphous States: The as-prepared powders can be partially amorphous, which may not be suitable for applications requiring crystalline materials.
- Low Surface Area: The process typically produces particles with lower surface areas compared to other methods like spray drying or freeze-drying, which can be a disadvantage in applications where high surface area is beneficial.
-
Scale-Up Challenges:
- Limited Capacity: Ball mills have limited capacity for handling large quantities of material, making them less suitable for large-scale production.
- Cost Considerations: While ball milling is generally inexpensive, the cost of scaling up the process, including the need for larger equipment and higher energy consumption, can be significant.
In summary, while ball milling is a versatile and cost-effective method for material processing, it has several limitations that need to be carefully considered. These include challenges related to material properties, equipment wear, energy consumption, thermal damage, noise, and product quality. Understanding these limitations is essential for selecting the right milling method for specific applications and for optimizing the process to achieve the desired outcomes.
Summary Table:
Limitation | Key Challenges |
---|---|
Material Limitations | Ineffective for soft, tacky, or fibrous materials; damages heat-sensitive materials. |
Equipment Wear | High wear rates and contamination risks from milling components. |
Energy Consumption | Energy-intensive process with high operational costs. |
Thermal Damage | Heat generation can degrade materials; requires costly mitigation strategies. |
Noise and Vibrations | Produces loud noise and strong vibrations, affecting stability and product quality. |
Product Quality Issues | Polydisperse size distributions, partially amorphous states, and low surface area. |
Scale-Up Challenges | Limited capacity and high costs for large-scale production. |
Need help selecting the right milling method for your application? Contact our experts today!