Low-cost catalysts for pyrolysis are essential for making the process economically viable, especially in large-scale applications. These catalysts are typically derived from natural or waste materials, such as zeolites, clay minerals like kaolin, biochar, and inorganic materials inherently present in biomass. They enhance the pyrolysis process by promoting desirable chemical reactions, improving product quality, and increasing yields of biofuels and valuable chemicals. While commercial catalysts can be expensive, low-cost alternatives like biochar and biomass-derived inorganic materials offer effective catalytic activity. Additionally, coupling secondary porosity with conventional catalysts can further improve performance. These low-cost options make pyrolysis more accessible and sustainable.
Key Points Explained:
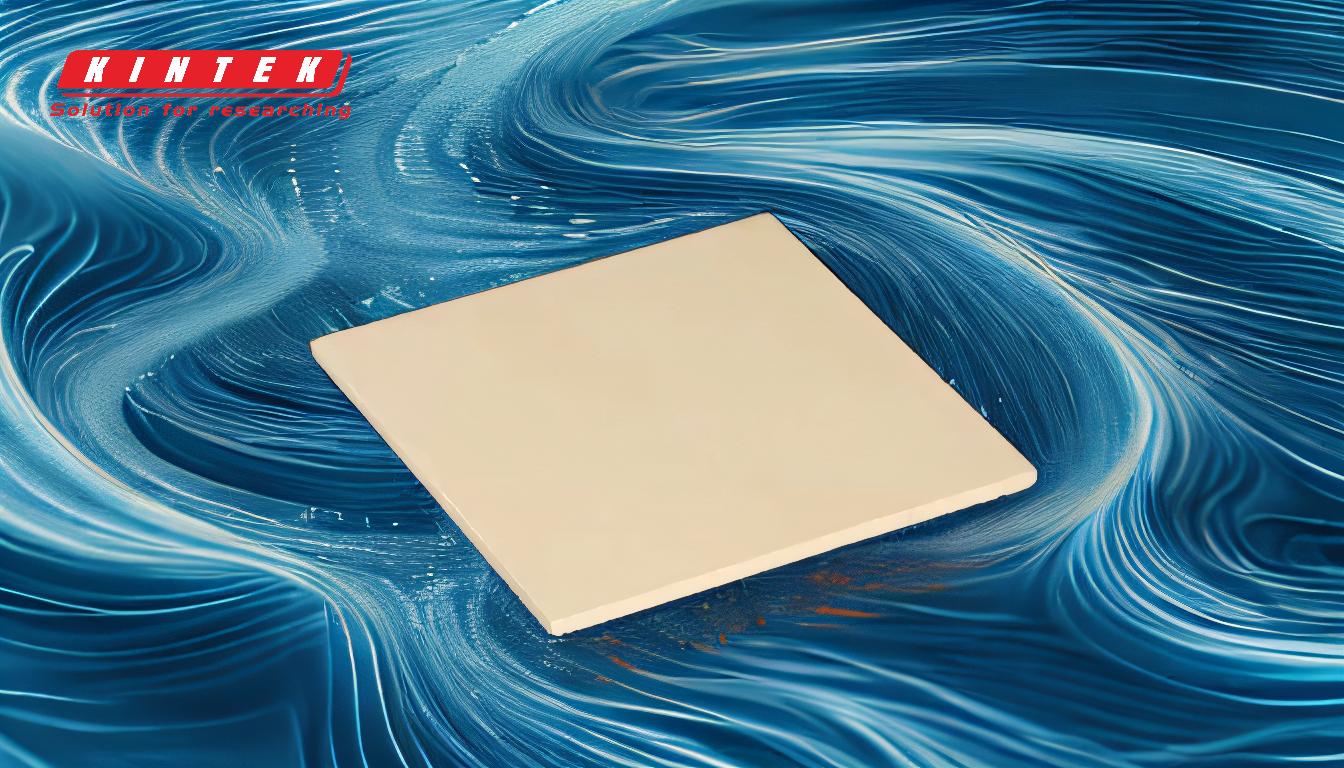
-
Zeolites as Low-Cost Catalysts:
- Zeolites are porous materials composed of aluminum and silicon oxides, making them cost-effective and widely available.
- They selectively crack heavy hydrocarbons and condense light hydrocarbons, producing C1, C2, and C3 hydrocarbons from biomass.
- Their natural abundance and ability to tailor pore sizes for specific reactions make them a practical choice for pyrolysis.
-
Clay Minerals (e.g., Kaolin):
- Clay minerals like kaolin are inexpensive and abundant, making them suitable for large-scale pyrolysis applications.
- They exhibit catalytic activity by promoting the cracking of hydrocarbons and improving the yield of desired products.
- Their natural composition and low cost make them an attractive alternative to synthetic catalysts.
-
Biochar-Based Catalysts:
- Biochar, a byproduct of biomass pyrolysis, can be used as a catalyst to promote desirable chemical reactions during pyrolysis.
- It improves the yield of biofuels and valuable chemicals, enhancing the overall efficiency of the process.
- Using biochar as a catalyst is cost-effective and sustainable, as it recycles waste materials.
-
Inorganic Materials in Biomass:
- Alkali and alkali-earth metals inherently present in biomass exhibit catalytic activity during pyrolysis.
- These materials reduce the need for external catalysts, lowering costs and simplifying the process.
- Their natural presence in biomass makes them a practical and low-cost option for pyrolysis.
-
Heterogeneous Catalysts for Specific Applications:
- For furfural production, low-cost heterogeneous catalysts like titanium compounds (e.g., TiN) and metal nitrides (e.g., GaN) are effective.
- These catalysts promote the production of furfural compounds, a valuable chemical derived from biomass.
- Their use in fast pyrolysis demonstrates their versatility and cost-effectiveness for targeted applications.
-
Coupling Secondary Porosity with Conventional Catalysts:
- Adding a secondary level of porosity to conventional catalysts creates a multidimensional structure (micro, meso, and macro pores).
- This approach improves molecular traffic control, enhancing the efficiency and selectivity of the catalyst.
- While not inherently low-cost, this method can optimize the performance of existing catalysts, making them more cost-effective in the long run.
-
Economic and Environmental Benefits:
- Low-cost catalysts reduce the overall cost of pyrolysis, making it more accessible for large-scale industrial applications.
- Using natural or waste-derived catalysts aligns with sustainability goals by minimizing environmental impact.
- These catalysts improve product quality, enabling the production of drop-in fuels and other valuable chemicals.
By leveraging these low-cost catalysts, pyrolysis can become a more economically viable and environmentally friendly process for converting biomass and waste materials into valuable products.
Summary Table:
Catalyst Type | Key Benefits | Applications |
---|---|---|
Zeolites | Cost-effective, widely available, tailorable pore sizes for specific reactions | Cracking heavy hydrocarbons, producing C1, C2, and C3 hydrocarbons |
Clay Minerals (Kaolin) | Inexpensive, abundant, promotes hydrocarbon cracking | Large-scale pyrolysis, improving product yield |
Biochar | Sustainable, cost-effective, improves biofuel and chemical yields | Recycling waste materials, enhancing pyrolysis efficiency |
Inorganic Biomass Materials | Natural catalytic activity, reduces need for external catalysts | Simplifying pyrolysis processes, lowering costs |
Heterogeneous Catalysts | Effective for furfural production, versatile, cost-effective | Targeted applications like fast pyrolysis |
Secondary Porosity Coupling | Improves molecular traffic control, enhances catalyst efficiency | Optimizing conventional catalysts for better performance |
Ready to optimize your pyrolysis process with low-cost catalysts? Contact our experts today for tailored solutions!