Optimizing a PECVD (Plasma-Enhanced Chemical Vapor Deposition) process involves fine-tuning several machine parameters to achieve high-quality thin films with desired properties. The main parameters include gas flow rate, temperature, pressure, RF power, plate spacing, reaction chamber dimensions, and substrate conditions. These factors influence plasma generation, film density, deposition uniformity, and overall process stability. Proper control of these parameters, along with regular equipment maintenance and a deep understanding of process principles, ensures reproducibility and high-quality results. Below is a detailed breakdown of the key parameters and their roles in optimizing the PECVD process.
Key Points Explained:
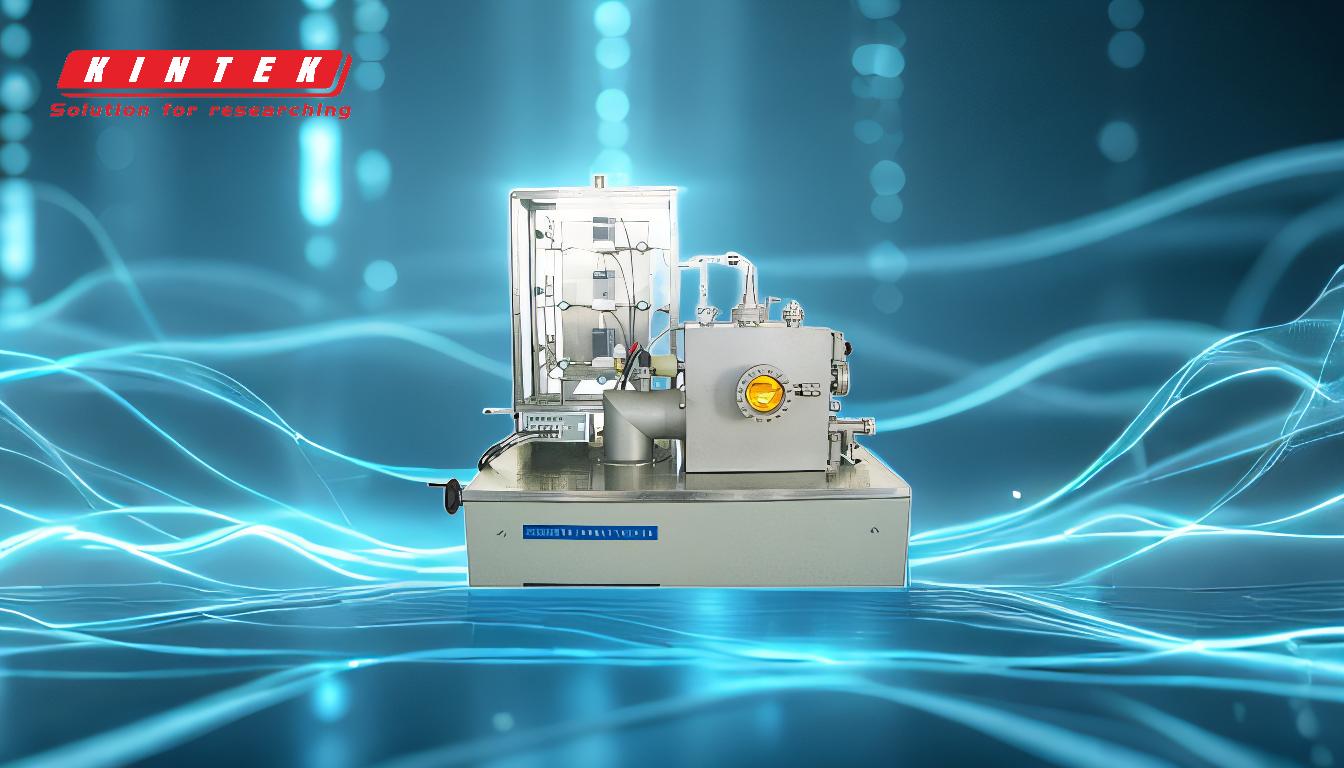
-
Gas Flow Rate:
- Role: Controls the supply of precursor gases into the reaction chamber.
- Impact: Affects the chemical reactions and deposition rate. Too high or too low flow rates can lead to poor film quality or incomplete reactions.
- Optimization: Adjust flow rates to ensure a balanced supply of reactants for uniform film growth.
-
Temperature:
- Role: Influences the kinetics of chemical reactions and the mobility of atoms on the substrate.
- Impact: Higher temperatures generally improve film density and adhesion but may also increase stress or cause unwanted reactions.
- Optimization: Maintain an optimal temperature range to balance film quality and substrate integrity.
-
Pressure:
- Role: Determines the density of the plasma and the mean free path of particles.
- Impact: Affects plasma uniformity, deposition rate, and film properties such as density and stress.
- Optimization: Adjust pressure to achieve stable plasma conditions and uniform film deposition.
-
RF Power:
- Role: Provides energy to ionize gas molecules and sustain the plasma.
- Impact: Higher RF power increases plasma density and ion bombardment, improving film density but potentially causing damage to the substrate.
- Optimization: Fine-tune RF power to achieve the desired plasma characteristics without compromising substrate quality.
-
Plate Spacing and Reaction Chamber Dimensions:
- Role: Determines the distribution of the electric field and plasma density.
- Impact: Affects ignition voltage, deposition uniformity, and film thickness.
- Optimization: Adjust plate spacing and chamber dimensions to ensure uniform plasma distribution and consistent film deposition.
-
Operating Frequency of the RF Power Supply:
- Role: Influences ion energy and plasma density.
- Impact: Higher frequencies generally result in lower ion energy but higher plasma density, affecting film density and stress.
- Optimization: Select an appropriate frequency to balance ion energy and plasma density for the desired film properties.
-
Substrate Temperature and Bias:
- Role: Affects the mobility of deposited atoms and the energy of ions impacting the substrate.
- Impact: Influences film adhesion, stress, and microstructure.
- Optimization: Control substrate temperature and bias to achieve the desired film properties and minimize defects.
-
Discharge Methods and Voltage:
- Role: Determines how the plasma is generated and sustained.
- Impact: Different discharge methods (e.g., DC, RF, microwave) affect plasma characteristics and film properties.
- Optimization: Choose the appropriate discharge method and voltage to achieve stable and efficient plasma generation.
-
Ventilation Methods:
- Role: Controls the removal of by-products and excess gases from the reaction chamber.
- Impact: Affects the purity and uniformity of the deposited film.
- Optimization: Ensure efficient ventilation to maintain a clean reaction environment and consistent film quality.
-
Equipment Stability and Maintenance:
- Role: Ensures consistent operation and reproducibility of the PECVD process.
- Impact: Equipment instability can lead to variations in film properties and process failures.
- Optimization: Regularly maintain and calibrate equipment to ensure stable and reliable performance.
By systematically optimizing these parameters, the PECVD process can be fine-tuned to produce high-quality thin films with the desired properties, ensuring reproducibility and efficiency in manufacturing.
Summary Table:
Parameter | Role | Impact | Optimization |
---|---|---|---|
Gas Flow Rate | Controls precursor gas supply | Affects deposition rate and film quality | Adjust for balanced reactant supply |
Temperature | Influences reaction kinetics and atom mobility | Impacts film density, adhesion, and stress | Maintain optimal range for quality and substrate integrity |
Pressure | Determines plasma density and particle mean free path | Affects plasma uniformity and film properties | Adjust for stable plasma and uniform deposition |
RF Power | Provides energy for plasma generation | Increases plasma density but may damage substrate | Fine-tune for desired plasma characteristics |
Plate Spacing & Dimensions | Affects electric field distribution and plasma density | Influences ignition voltage and deposition uniformity | Adjust for uniform plasma and consistent film deposition |
RF Frequency | Influences ion energy and plasma density | Affects film density and stress | Select frequency to balance ion energy and plasma density |
Substrate Temp & Bias | Affects atom mobility and ion energy | Influences adhesion, stress, and microstructure | Control for desired film properties and defect minimization |
Discharge Methods & Voltage | Determines plasma generation method | Affects plasma characteristics and film properties | Choose appropriate method for stable and efficient plasma |
Ventilation Methods | Removes by-products and excess gases | Impacts film purity and uniformity | Ensure efficient ventilation for clean reaction environment |
Equipment Stability | Ensures consistent operation and reproducibility | Instability leads to process variations and failures | Regular maintenance and calibration for reliable performance |
Ready to optimize your PECVD process? Contact our experts today for tailored solutions and support!