Bio-oil, a renewable energy source derived from biomass, is produced through three primary methods: pyrolysis, hydrothermal liquefaction, and chemical extraction. Pyrolysis is the most common method, involving the rapid heating of biomass in the absence of oxygen to produce a liquid bio-oil, along with gas and solid char. Hydrothermal liquefaction uses water at high temperatures and pressures to convert wet biomass into bio-oil, making it suitable for high-moisture feedstocks. Chemical extraction involves isolating oils from biomass using solvents or mechanical methods, often used for oil-rich feedstocks like algae or seeds. Each method has its advantages and challenges, such as energy efficiency, feedstock suitability, and the need for further processing to improve bio-oil quality.
Key Points Explained:
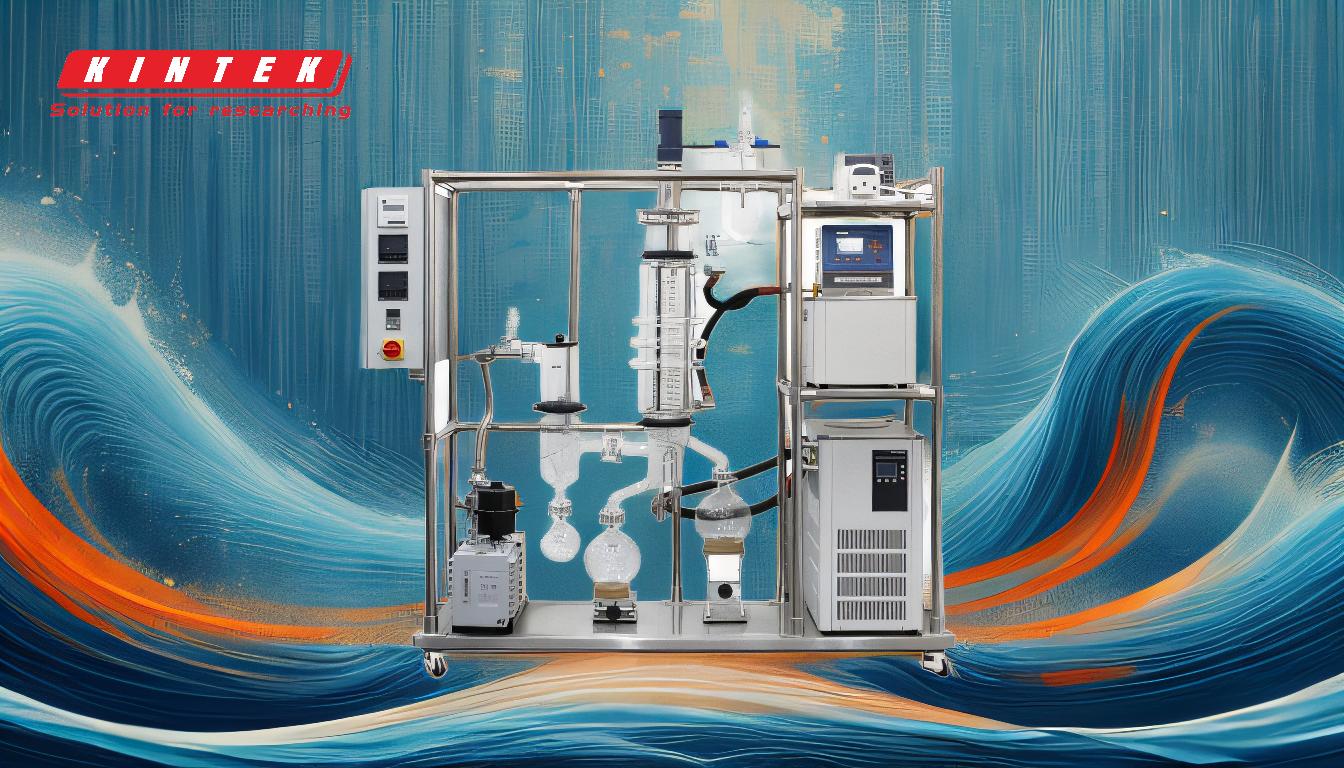
-
Pyrolysis
- Process Overview: Pyrolysis involves heating biomass to high temperatures (around 500°C) in the absence of oxygen. This process breaks down the biomass into gas, solid char, and liquid bio-oil.
-
Types of Pyrolysis:
- Fast Pyrolysis: The most common method, characterized by rapid heating and cooling, which maximizes liquid bio-oil yield.
- Catalytic Pyrolysis: Incorporates catalysts during pyrolysis to improve the quality of bio-oil by reducing oxygen content in situ.
- Output Characteristics: Bio-oil produced through pyrolysis is typically dark brown to black, with a density of about 1.2 kg/liter. It contains water and organic compounds derived from cellulose, hemicellulose, and lignin in the biomass.
- Applications: Bio-oil can be used as a substitute for fossil fuels in heating, electricity generation, and transportation after further processing.
-
Hydrothermal Liquefaction
- Process Overview: This method uses water at high temperatures (200–400°C) and pressures (5–20 MPa) to convert wet biomass into bio-oil. It is particularly suitable for feedstocks with high moisture content, such as algae or sewage sludge.
-
Advantages:
- Eliminates the need for drying biomass, reducing energy consumption.
- Can process a wide range of feedstocks, including those unsuitable for pyrolysis.
- Output Characteristics: The bio-oil produced is often more stable and has a higher energy density compared to pyrolysis-derived bio-oil.
- Challenges: High operating costs due to the need for specialized equipment to handle high pressures and temperatures.
-
Chemical Extraction
- Process Overview: This method involves extracting oils from biomass using solvents or mechanical pressing. It is commonly used for oil-rich feedstocks like algae, seeds, or nuts.
-
Types of Extraction:
- Solvent Extraction: Uses organic solvents to dissolve and separate oils from biomass.
- Mechanical Extraction: Involves pressing or grinding biomass to release oils, often used for seeds like soybeans or sunflower seeds.
-
Advantages:
- Simple and cost-effective for specific feedstocks.
- Produces high-quality oils suitable for direct use or further refining.
- Challenges: Limited to feedstocks with naturally high oil content and may require additional processing to remove solvents or impurities.
-
Upgrading Bio-Oil
- Hydrodeoxygenation: A post-processing method to upgrade bio-oil by removing oxygen, which improves its stability and compatibility with existing fuel infrastructure. However, it requires high pressure and is costly.
- Catalytic Upgrading: Involves using catalysts during or after pyrolysis to enhance bio-oil quality, such as reducing acidity or improving energy density.
-
Comparison of Methods
-
Feedstock Suitability:
- Pyrolysis: Best for dry biomass.
- Hydrothermal Liquefaction: Ideal for wet biomass.
- Chemical Extraction: Suitable for oil-rich biomass.
-
Energy Efficiency:
- Pyrolysis and hydrothermal liquefaction are energy-intensive but yield high-quality bio-oil.
- Chemical extraction is less energy-intensive but limited to specific feedstocks.
-
Economic Considerations:
- Pyrolysis and hydrothermal liquefaction require significant capital investment but offer scalable solutions.
- Chemical extraction is cost-effective for niche applications but lacks scalability for large-scale production.
-
Feedstock Suitability:
-
Future Prospects
- Research is focused on improving the efficiency and cost-effectiveness of bio-oil production methods.
- Innovations in catalysts and process optimization are expected to enhance bio-oil quality and reduce production costs.
- Integration with renewable energy systems, such as solar or wind, could further reduce the carbon footprint of bio-oil production.
By understanding these methods, stakeholders can choose the most appropriate production technique based on their specific feedstock, energy requirements, and economic constraints.
Summary Table:
Method | Key Features | Advantages | Challenges |
---|---|---|---|
Pyrolysis | - Rapid heating of biomass (500°C) in the absence of oxygen. | - Maximizes liquid bio-oil yield. | - Energy-intensive; requires further processing for stability. |
Hydrothermal Liquefaction | - Uses water at high temperatures (200–400°C) and pressures (5–20 MPa). | - Suitable for wet biomass; eliminates drying needs. | - High operating costs; specialized equipment required. |
Chemical Extraction | - Extracts oils using solvents or mechanical methods. | - Simple and cost-effective for oil-rich feedstocks. | - Limited to specific feedstocks; may require solvent removal. |
Ready to explore bio-oil production methods? Contact us today to learn more!