Leak detection in vacuum systems is a critical process to ensure the system's integrity and performance. Several methods are employed to identify and locate leaks, ranging from simple observations to sophisticated instrumentation. These methods include using vacuum mud for temporary repairs, helium mass spectrometer leak detectors, injecting acetone or ether into suspected leak points, and employing blind plates for sectional testing. Additionally, techniques like the blowing method, suction nozzle method, and residual gas analysis are used for more precise detection. Monitoring changes in vacuum or pressure, using hydrogen detectors, and performing preventive maintenance are also essential practices.
Key Points Explained:
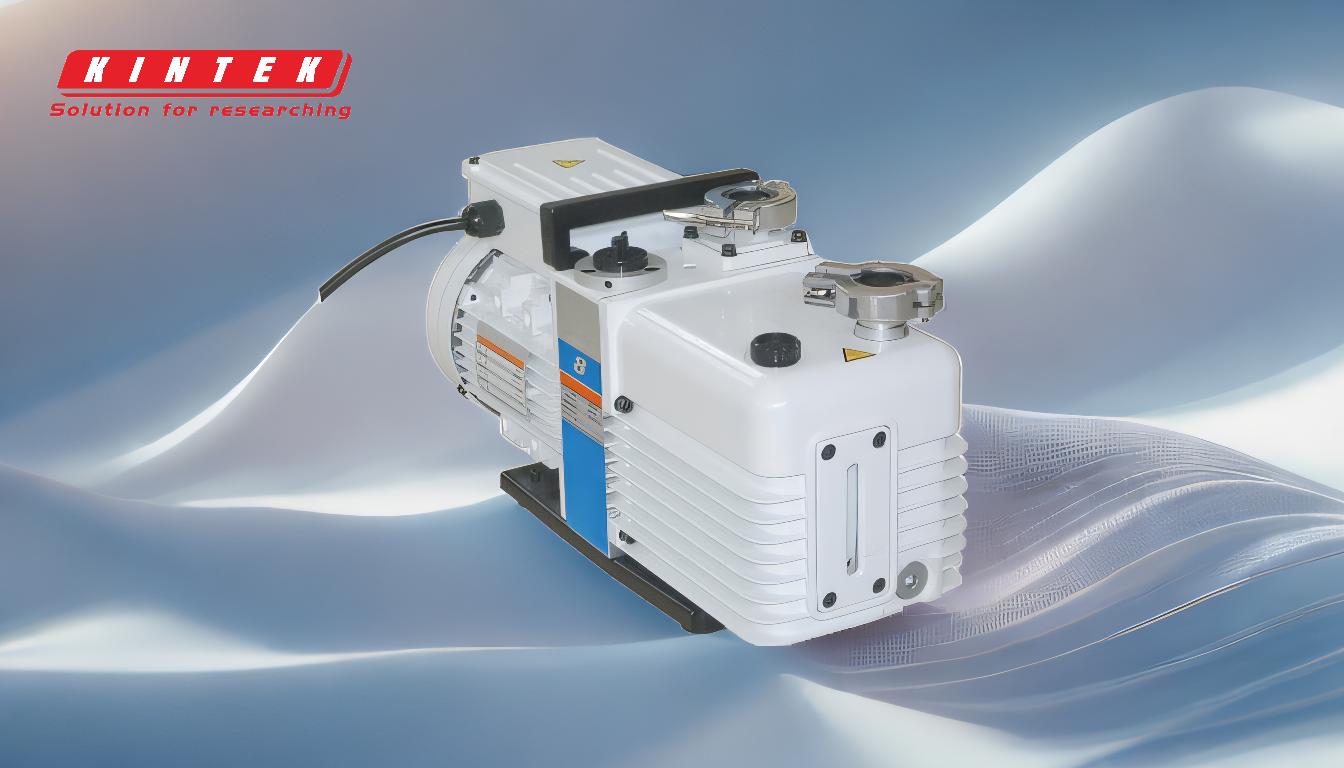
-
Vacuum Mud for Temporary Repairs:
- Vacuum mud is a quick solution for emergency repairs. It can temporarily seal small leaks, allowing the system to continue operating until a permanent fix is applied. This method is particularly useful in situations where immediate action is required to prevent system failure.
-
Helium Mass Spectrometer Leak Detector:
- This is one of the most sensitive and widely used methods for leak detection. Helium is introduced into the system, and a mass spectrometer detects any helium that escapes through leaks. This method is highly effective for pinpointing the exact location of leaks, even in complex systems.
-
Injecting Acetone or Ether:
- A medical needle can be used to inject acetone or ether into suspected leak points. The change in vacuum gauge readings indicates the presence of a leak. This method is useful for identifying leaks in specific areas but requires careful handling due to the flammable nature of the substances used.
-
Blind Plate with Holes for Vacuum Silicon Tubes:
- A blind plate with holes can be used to block sections of vacuum tubes, allowing for sectional testing. This method helps isolate the leak to a specific section of the system, making it easier to locate and repair.
-
Blowing Method:
- In this method, the furnace chamber is evacuated, and helium gas is applied to the outside. The presence of helium inside the chamber indicates a leak. This method is effective for detecting leaks in large systems like vacuum furnaces.
-
Suction Nozzle Method:
- When the test object cannot be evacuated, the suction nozzle method is used. The test object is filled with a leak detection gas, and a sensor checks for gas escaping from the outside. This method is particularly useful for non-evacuable systems.
-
Monitoring Changes in Vacuum or Pressure:
- A decrease in vacuum or pressure often indicates a leak. Introducing gas into the chamber and observing the pressure gauge can help locate the leak. This method is straightforward and can be used as an initial check before employing more sophisticated techniques.
-
Residual Gas Analysis:
- This sophisticated method involves analyzing the residual gases in the vacuum system to identify leaks. It provides detailed information about the composition of the gases, helping to pinpoint the source of the leak accurately.
-
Hydrogen Detectors:
- Ensuring the hydrogen level is above 3% and using a mobile hydrogen detector can help verify gas tightness in the leaking section. This method is particularly useful in systems where hydrogen is used as a process gas.
-
Preventive Maintenance:
- Tracking previous leak locations and replacing temporary sealing compounds are critical parts of a preventive maintenance program. Regular inspections and maintenance help prevent leaks before they become significant issues.
By employing these methods, operators can effectively detect and repair leaks in vacuum systems, ensuring optimal performance and longevity of the equipment.
Summary Table:
Method | Description |
---|---|
Vacuum Mud for Temporary Repairs | Temporary sealing of small leaks for emergency repairs. |
Helium Mass Spectrometer | Detects helium escaping through leaks for precise location identification. |
Injecting Acetone or Ether | Identifies leaks by observing vacuum gauge changes after injection. |
Blind Plate with Holes | Isolates leaks in specific sections using sectional testing. |
Blowing Method | Detects leaks in large systems by applying helium gas externally. |
Suction Nozzle Method | Checks for gas escaping in non-evacuable systems. |
Monitoring Vacuum/Pressure Changes | Observes pressure changes to identify leaks. |
Residual Gas Analysis | Analyzes residual gases to pinpoint leak sources accurately. |
Hydrogen Detectors | Ensures gas tightness in systems using hydrogen. |
Preventive Maintenance | Tracks and repairs leaks proactively to prevent system failures. |
Ensure your vacuum system's integrity—contact our experts today for advanced leak detection solutions!