RF sputtering is a versatile deposition technique used for both conductive and non-conductive materials, particularly suited for dielectric targets. It operates using a high-frequency AC power source (13.56 MHz) with specific parameters such as RF peak-to-peak voltage (1000 V), electron densities (10^9 to 10^11 Cm^-3), and chamber pressure (0.5 to 10 mTorr). The process involves alternating cycles where the target material alternates between positive and negative charges, enabling the sputtering of insulating materials by preventing charge buildup. Key factors influencing the process include incident ion energy, ion and target atom mass, angle of incidence, and sputtering yield. RF sputtering is characterized by lower deposition rates and higher costs, making it ideal for smaller substrates and specialized applications.
Key Points Explained:
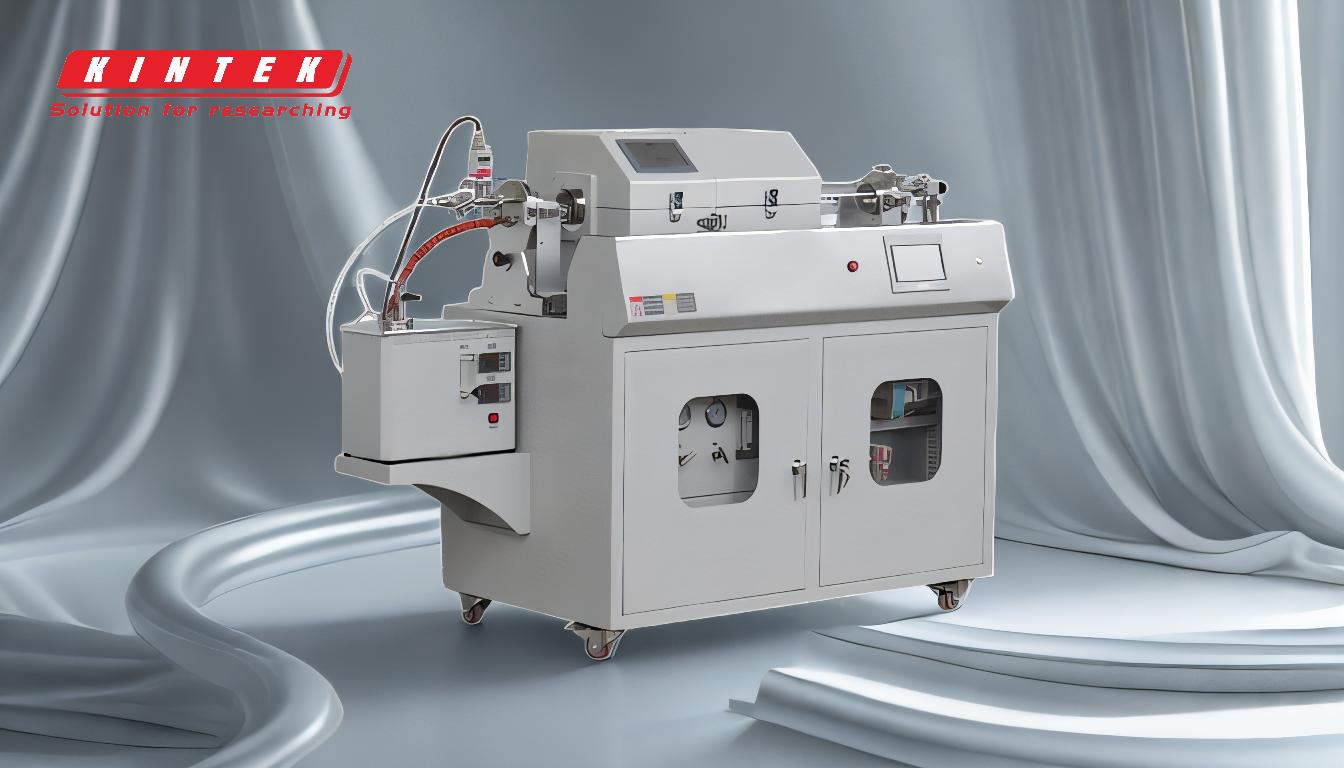
-
RF Power Source and Frequency:
- RF sputtering uses an AC power source operating at a fixed frequency of 13.56 MHz.
- This frequency is chosen to avoid interference with communication frequencies and to efficiently transfer energy to the plasma.
-
RF Peak-to-Peak Voltage:
- The RF peak-to-peak voltage is typically 1000 V, which is sufficient to sustain the plasma and ensure effective sputtering of target materials.
-
Electron Density:
- Electron densities in RF sputtering range from 10^9 to 10^11 Cm^-3. This range ensures a stable plasma environment, which is critical for consistent sputtering.
-
Chamber Pressure:
- The chamber pressure is maintained between 0.5 to 10 mTorr. This low-pressure environment is essential for minimizing collisions between gas molecules and ensuring that sputtered particles reach the substrate without significant scattering.
-
Material Compatibility:
- RF sputtering is suitable for both conductive and non-conductive materials, but it is particularly advantageous for dielectric (insulating) materials. The alternating charge cycles prevent charge buildup on insulating targets, which can otherwise inhibit sputtering.
-
Deposition Rate:
- The deposition rate in RF sputtering is generally lower compared to DC sputtering. This is due to the alternating nature of the RF process, which reduces the overall ion bombardment efficiency.
-
Substrate Size and Cost:
- RF sputtering is typically used for smaller substrate sizes due to higher operational costs. The complexity of the RF power supply and matching network contributes to these costs.
-
Cyclic Process:
- The RF sputtering process involves two cycles:
- Positive Cycle: The target material acts as an anode, attracting electrons and creating a negative bias.
- Negative Cycle: The target becomes positively charged, enabling ion bombardment and the ejection of target atoms toward the substrate.
- The RF sputtering process involves two cycles:
-
Sputtering Yield:
- The sputtering yield, defined as the number of target atoms ejected per incident ion, depends on factors such as incident ion energy, ion and target atom mass, and the angle of incidence. These factors vary with different target materials and sputtering conditions.
-
Prevention of Charge Buildup:
- In RF sputtering, the alternating charge cycles prevent charge buildup on insulating targets. This is crucial for maintaining a consistent sputtering process and avoiding disruptions caused by excessive surface charging.
-
Kinetic Energy and Surface Mobility:
- The kinetic energy of emitted particles influences their direction and deposition on the substrate. Higher kinetic energy can improve surface mobility, leading to better film quality and coverage.
-
Chamber Pressure and Coverage:
- Chamber pressure plays a significant role in determining the coverage and uniformity of the deposited film. Optimal pressure settings help achieve desired film properties by controlling the mean free path of sputtered particles.
By understanding these parameters, equipment and consumable purchasers can make informed decisions about the suitability of RF sputtering for their specific applications, balancing factors such as material compatibility, deposition rate, and cost.
Summary Table:
Parameter | Details |
---|---|
RF Power Source | AC power source at 13.56 MHz |
RF Peak-to-Peak Voltage | 1000 V |
Electron Density | 10^9 to 10^11 Cm^-3 |
Chamber Pressure | 0.5 to 10 mTorr |
Material Compatibility | Conductive and non-conductive (ideal for dielectric materials) |
Deposition Rate | Lower than DC sputtering |
Substrate Size | Smaller substrates |
Cyclic Process | Alternating positive and negative charge cycles |
Sputtering Yield | Depends on ion energy, mass, and angle of incidence |
Prevention of Charge Buildup | Alternating cycles prevent charge buildup on insulating targets |
Discover how RF sputtering can enhance your material deposition process—contact our experts today!