Injection molds are complex assemblies composed of multiple parts, each serving a specific function in the molding process. The primary components include the mold base, core, inserts, nozzle and sprue bushing, runner system, ejector pins, and mold interlocks. The mold base provides structural support, while the core and cavities define the shape of the molded part. Inserts allow for customization, and the nozzle and sprue bushing facilitate the flow of material into the mold. The runner system channels the material, and ejector pins help remove the finished product. Mold interlocks ensure proper alignment during the process. Understanding these parts is essential for optimizing mold design and production efficiency.
Key Points Explained:
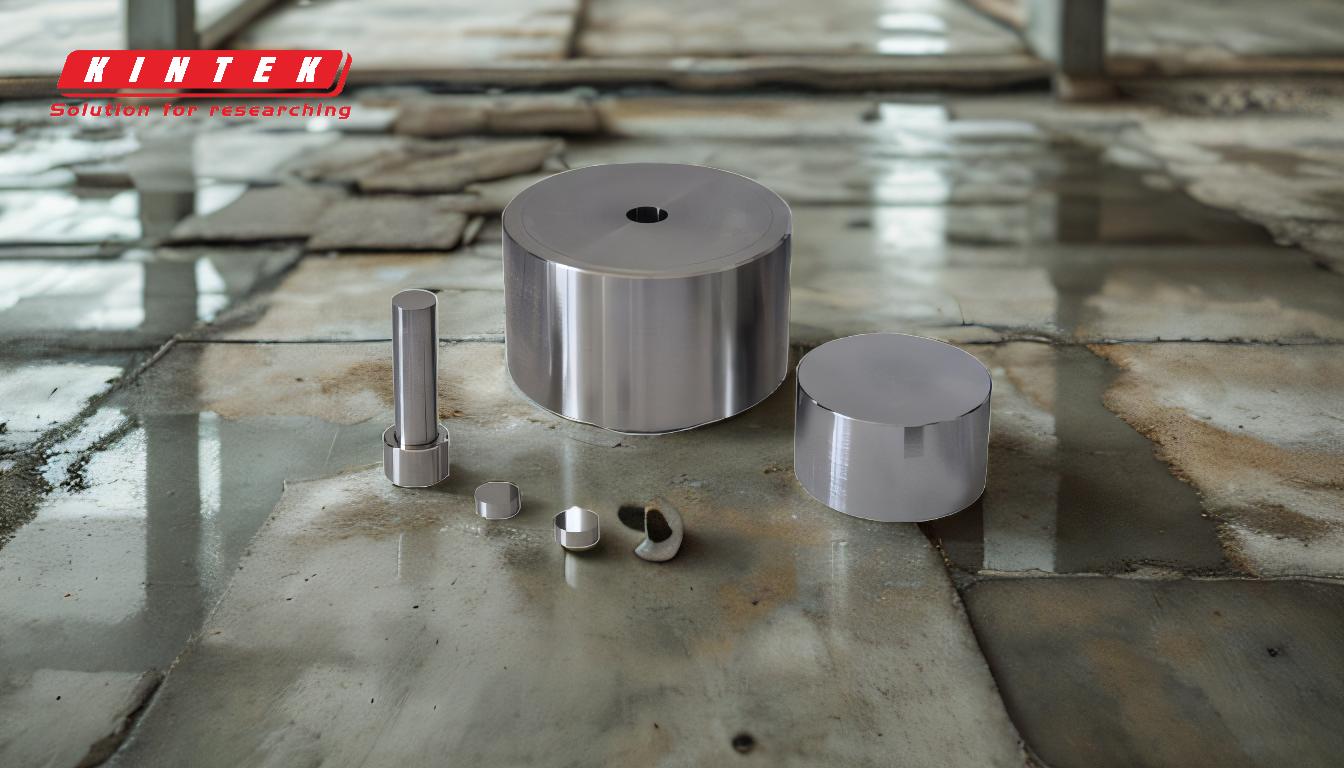
-
Mold Base
- The mold base is the foundational structure of the mold, providing stability and support for all other components.
- It typically consists of two plates: the "A" plate (cavity side) and the "B" plate (core side).
- The mold base ensures proper alignment and rigidity during the injection molding process, which is critical for producing consistent and high-quality parts.
-
Core
- The core is the male component of the mold that shapes the internal features of the molded part.
- It works in conjunction with the cavity (female component) to define the part's geometry.
- The core is often mounted on the "B" plate and must be precisely machined to match the cavity for accurate part formation.
-
Inserts
- Inserts are additional components that can be added to the mold to create specific features or details in the molded part.
- They are often used for complex geometries or to reduce wear on the main mold components.
- Inserts can be replaced or modified without altering the entire mold, making them cost-effective for customization.
-
Nozzle & Sprue Bushing
- The nozzle is the point where molten material enters the mold from the injection molding machine.
- The sprue bushing connects the nozzle to the runner system, ensuring a smooth flow of material.
- These components are critical for controlling the material flow and preventing leaks or blockages during the injection process.
-
Runner System
- The runner system consists of channels that guide the molten material from the sprue to the cavities.
- It includes the sprue, runners, and gates, which regulate the flow and pressure of the material.
- Proper design of the runner system is essential for minimizing waste and ensuring even filling of the cavities.
-
Ejector Pins
- Ejector pins are used to push the finished part out of the mold once it has solidified.
- They are strategically placed to avoid damaging the part while ensuring complete ejection.
- Ejector pins are typically activated by an ejector plate, which moves them forward to release the part.
-
Mold Interlocks
- Mold interlocks are mechanisms that ensure the two halves of the mold remain securely aligned during the injection process.
- They prevent misalignment, which could lead to defects in the molded part.
- Interlocks are especially important for molds with complex geometries or high production volumes.
-
Cavities
- Cavities are the hollow spaces in the mold that define the outer shape of the molded part.
- They are typically located on the "A" plate and work in tandem with the core to form the part.
- The number of cavities in a mold determines how many parts can be produced in a single cycle.
-
Cooling System
- Although not explicitly mentioned in the references, a cooling system is often integrated into the mold to regulate temperature.
- Cooling channels are strategically placed to ensure uniform cooling of the molded part, reducing cycle times and preventing warping or defects.
-
Venting
- Venting is another critical aspect of mold design, allowing air to escape as the molten material fills the cavities.
- Proper venting prevents air traps, which can cause voids or surface defects in the finished part.
By understanding these components and their functions, equipment and consumable purchasers can make informed decisions about mold design, maintenance, and optimization. Each part plays a vital role in ensuring the efficiency, quality, and longevity of the injection molding process.
Summary Table:
Component | Function |
---|---|
Mold Base | Provides structural support and alignment for the mold. |
Core | Shapes the internal features of the molded part. |
Inserts | Adds customization and reduces wear on mold components. |
Nozzle & Sprue Bushing | Facilitates material flow into the mold. |
Runner System | Channels molten material to the cavities, minimizing waste. |
Ejector Pins | Pushes the finished part out of the mold. |
Mold Interlocks | Ensures proper alignment of mold halves during the process. |
Cavities | Defines the outer shape of the molded part. |
Cooling System | Regulates temperature for uniform cooling and reduced cycle times. |
Venting | Allows air to escape, preventing defects in the finished part. |
Ready to optimize your injection mold design? Contact our experts today for tailored solutions!