Ball mills are widely used in various industries for grinding and mixing materials, but they come with several inherent problems. These include high energy consumption, significant wear and tear, noise and vibration, potential material contamination, and limitations in handling certain types of materials. Understanding these issues is crucial for equipment and consumable purchasers to make informed decisions and implement solutions that mitigate these drawbacks.
Key Points Explained:
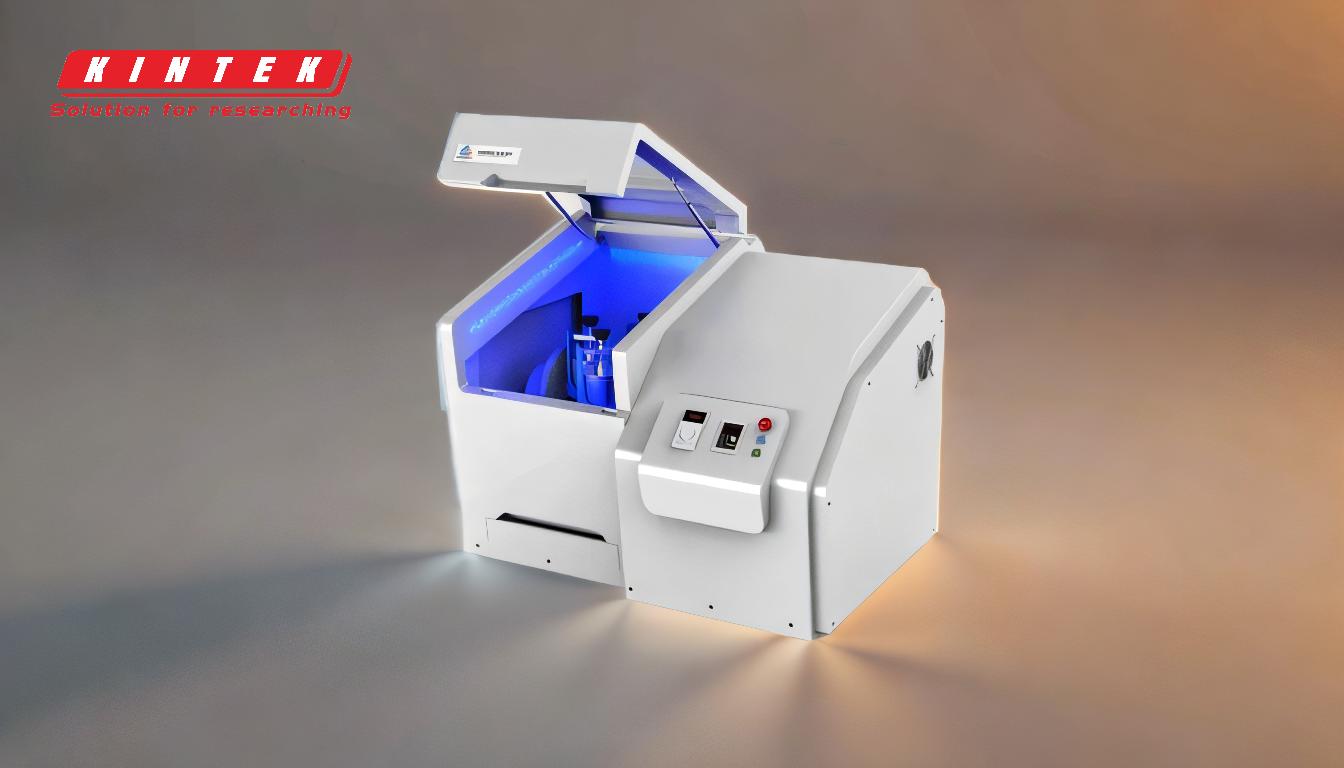
-
High Energy Consumption
- Ball mills are known for their high specific energy consumption, primarily due to:
- Wear of Balls and Wall Armor: The constant friction between the grinding media (balls) and the mill's interior lining leads to wear, requiring frequent replacements and increasing energy use.
- Friction and Material Heating: The grinding process generates heat, which not only consumes energy but can also cause thermal damage to sensitive materials.
- Implications for Purchasers: Energy management systems and energy-efficient grinding media should be considered to reduce operational costs and environmental impact.
- Ball mills are known for their high specific energy consumption, primarily due to:
-
Wear and Tear
- The grinding process involves significant friction between the material and the grinding medium, leading to:
- Wear of Components: Balls, wall armor, and other internal parts wear out over time, necessitating regular maintenance and replacement.
- Potential Contamination: Wear inside the cylinders can lead to material contamination, which is problematic in industries requiring high purity, such as pharmaceuticals or food processing.
- Implications for Purchasers: Purchasing high-quality, wear-resistant materials and implementing regular maintenance schedules can mitigate these issues.
- The grinding process involves significant friction between the material and the grinding medium, leading to:
-
Noise and Vibration
- Ball mills produce loud noise and strong vibrations during operation, which can:
- Impact Worker Safety: Prolonged exposure to noise can lead to hearing damage, and vibrations can cause discomfort or injuries.
- Affect Equipment Longevity: Vibrations can lead to mechanical stress, reducing the lifespan of the mill.
- Implications for Purchasers: Noise-dampening solutions, such as rubber linings or soundproof enclosures, and vibration-dampening mounts can improve working conditions and equipment durability.
- Ball mills produce loud noise and strong vibrations during operation, which can:
-
Material Handling Limitations
- Ball mills are not suitable for all types of materials, particularly:
- Soft, Tacky, and Fibrous Materials: These materials can clog the mill or fail to grind effectively.
- Large Quantities: Ball mills have limited capacity for handling large volumes, which can be a bottleneck in high-throughput operations.
- Implications for Purchasers: Alternative grinding technologies or pre-processing steps may be necessary for materials that are not well-suited to ball milling.
- Ball mills are not suitable for all types of materials, particularly:
-
Thermal Damage to Materials
- The heat generated during the grinding process can:
- Affect Material Properties: Sensitive materials, such as certain chemicals or biological samples, may undergo undesirable changes due to thermal exposure.
- Reduce Product Quality: Thermal damage can lead to inconsistencies in the final product, affecting its usability or market value.
- Implications for Purchasers: Cooling systems or low-temperature grinding methods should be considered for heat-sensitive materials.
- The heat generated during the grinding process can:
-
Maintenance and Servicing
- While ball mills are generally reliable and easy to service, they require:
- Periodic Ball Additions: To compensate for wear, balls must be added regularly, which can increase operational costs.
- Regular Inspections: Ensuring the mill operates efficiently and safely requires frequent checks and maintenance.
- Implications for Purchasers: Implementing a proactive maintenance schedule and using durable grinding media can reduce downtime and maintenance costs.
- While ball mills are generally reliable and easy to service, they require:
By addressing these key issues, purchasers can optimize the performance of ball mills, reduce operational costs, and ensure the quality of the final product. Solutions such as energy-efficient components, wear-resistant materials, noise and vibration dampening, and alternative grinding methods should be carefully considered based on the specific needs of the application.
Summary Table:
Problem | Causes | Solutions |
---|---|---|
High Energy Consumption | Wear of balls and wall armor, friction, and material heating | Use energy-efficient grinding media and energy management systems |
Wear and Tear | Friction between material and grinding medium | Invest in wear-resistant materials and implement regular maintenance |
Noise and Vibration | Loud noise and strong vibrations during operation | Install noise-dampening solutions and vibration-dampening mounts |
Material Handling Limits | Unsuitable for soft, tacky, fibrous, or large quantities of materials | Consider alternative grinding technologies or pre-processing steps |
Thermal Damage | Heat generated during grinding affects sensitive materials | Use cooling systems or low-temperature grinding methods |
Maintenance and Servicing | Frequent ball additions and regular inspections required | Adopt proactive maintenance schedules and durable grinding media |
Optimize your ball mill operations and reduce costs—contact our experts today for tailored solutions!