Plastic pyrolysis is a thermal decomposition process that converts plastic waste into valuable products such as pyrolysis oil, carbon black, and syngas. The process yields varying proportions of these products depending on the type of plastic and the pyrolysis method used. Pyrolysis oil, the primary product, can be used as fuel or further refined into chemicals. Carbon black is a solid residue with applications in manufacturing, while syngas, a mixture of gases like hydrogen and methane, can be used for energy generation or as a feedstock for chemical production. Additionally, the process may produce wastewater if the plastic contains moisture. This method not only reduces plastic waste but also creates economically valuable resources.
Key Points Explained:
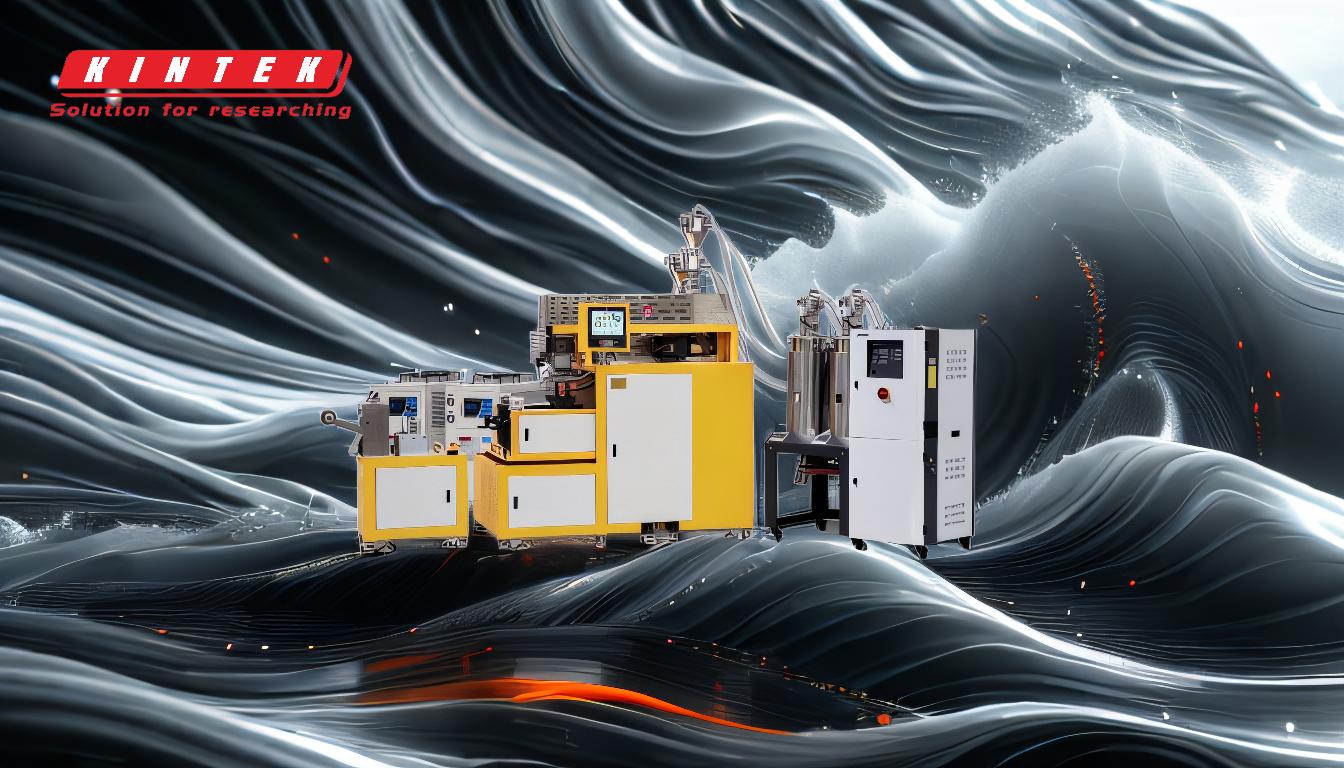
-
Primary Products of Plastic Pyrolysis:
- Pyrolysis Oil: The main product, accounting for 30-80% of the output, is a liquid fuel that can be used directly or refined into other chemicals. Its composition varies depending on the type of plastic processed.
- Carbon Black: A solid residue comprising 20-30% of the output, used in industries such as rubber manufacturing, ink production, and as a reinforcing agent in plastics.
- Syngas: A gaseous mixture (10-20% of the output) containing hydrogen, methane, and other hydrocarbons, which can be used for energy generation or as a chemical feedstock.
-
Secondary Products and Byproducts:
- Steel Wire: In cases like tire pyrolysis, steel wire (8-15% of the output) is recovered and recycled.
- Wastewater: Generated if the plastic waste contains moisture, requiring proper treatment to avoid environmental contamination.
-
Variability in Product Yields:
- The proportions of pyrolysis oil, carbon black, and syngas depend on the type of plastic or material being processed. For example, tire pyrolysis typically yields 35-45% oil, 30-35% carbon black, and 8-15% syngas, while other materials like rubber or oil sludge may have different outputs.
-
Cold Plasma Pyrolysis:
- This advanced method produces high-value products such as methane, hydrogen, ethylene, and hydrocarbons. Ethylene, a key building block for plastics, can be regenerated to create new materials, making this process particularly valuable for industrial applications.
-
Environmental and Economic Benefits:
- Plastic pyrolysis reduces plastic waste in landfills and oceans, mitigating environmental pollution.
- The process transforms waste into valuable resources, creating economic opportunities and reducing reliance on fossil fuels.
-
Applications of Pyrolysis Products:
- Pyrolysis Oil: Used as fuel in industrial boilers, furnaces, and power plants, or refined into diesel and gasoline.
- Carbon Black: Utilized in tire manufacturing, plastics, and pigments.
- Syngas: Employed for electricity generation, heating, or as a raw material for chemical synthesis.
-
Challenges and Considerations:
- The presence of moisture in plastic waste can lead to wastewater generation, requiring treatment systems.
- The variability in plastic composition affects the consistency and quality of pyrolysis products, necessitating careful feedstock selection and process optimization.
By converting plastic waste into valuable resources, plastic pyrolysis offers a sustainable solution to the global plastic pollution crisis while creating economic value. The process is versatile, with applications ranging from energy production to industrial manufacturing, making it a key technology in the transition to a circular economy.
Summary Table:
Product | Yield | Applications |
---|---|---|
Pyrolysis Oil | 30-80% | Fuel for boilers, furnaces, or refined into chemicals like diesel and gasoline. |
Carbon Black | 20-30% | Used in rubber manufacturing, plastics, and pigments. |
Syngas | 10-20% | Energy generation, heating, or chemical feedstock. |
Steel Wire | 8-15% | Recycled in tire pyrolysis. |
Wastewater | Variable | Requires treatment if moisture is present in plastic waste. |
Learn how plastic pyrolysis can benefit your business—contact us today!