Tungsten, while being a highly valuable material due to its exceptional properties like high melting point, density, and strength, presents several safety concerns, particularly in its pure form. The challenges associated with machining, handling, and processing tungsten stem from its physical and chemical properties. These concerns include difficulties in machining, brittleness at low temperatures, and the potential for material compaction during processing. Understanding these safety concerns is crucial for anyone working with tungsten, especially in industrial or laboratory settings.
Key Points Explained:
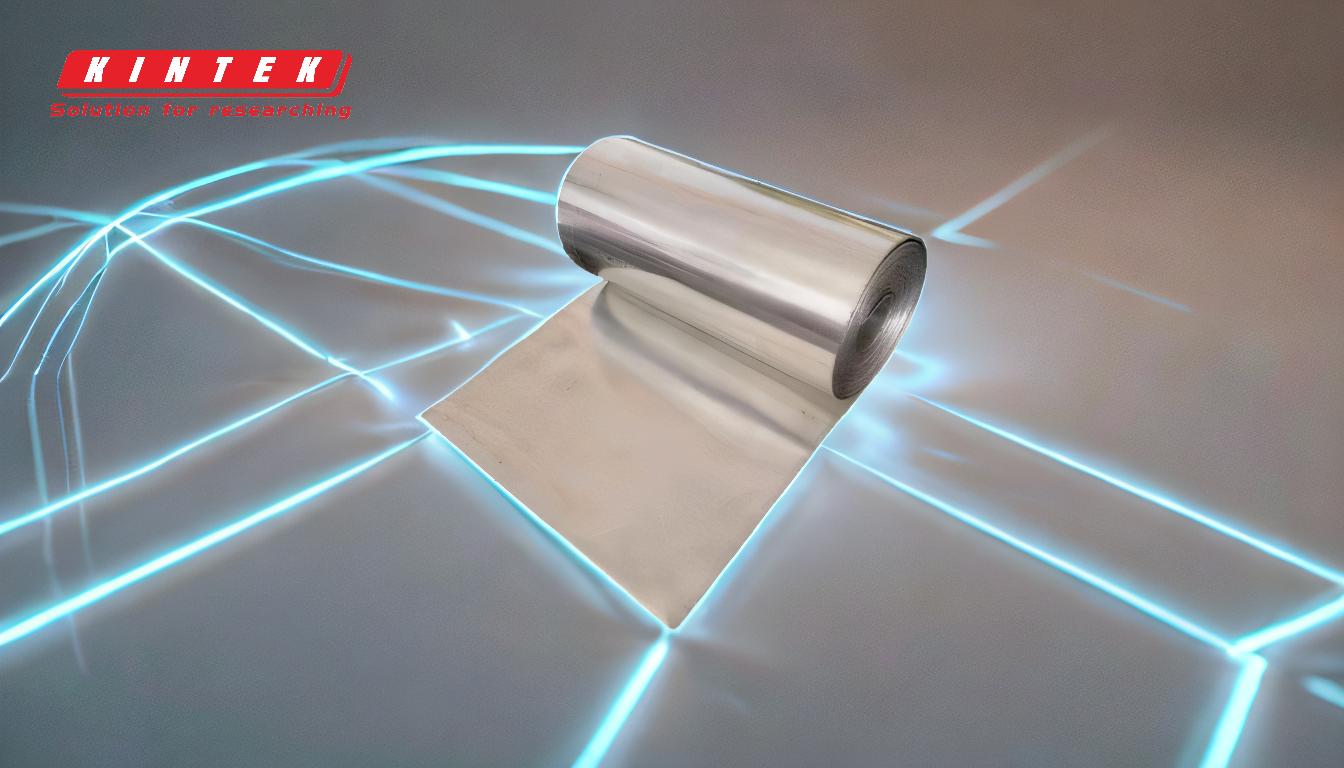
-
Machining Difficulties:
- Loading Issue: Pure tungsten is notoriously difficult to machine. Diamond tools, which are effective for machining tungsten carbide, are not suitable for pure tungsten. This is due to a phenomenon called "loading," where the tungsten material compacts into the spaces between the diamond particles on the tool. This not only reduces the efficiency of the machining process but also poses a risk of tool damage and potential injury due to unexpected tool behavior.
- Alternative Machining Methods: Given the challenges with diamond tools, alternative machining methods or tools made from different materials may be required. This adds complexity and cost to the machining process, necessitating careful planning and safety measures.
-
Brittleness at Low Temperatures:
- Ductile-to-Brittle Transition Temperature (DBTT): Tungsten exhibits a ductile-to-brittle transition temperature (DBTT), above which it is ductile and below which it becomes brittle. Typically, this transition temperature is higher than room temperature, meaning tungsten is brittle under normal conditions.
- Implications for Handling: The brittleness of tungsten at low temperatures means that it can fracture or shatter easily if not handled properly. This poses a significant safety risk, especially in environments where temperature fluctuations are common. Workers must be aware of this property and handle tungsten with care to avoid accidents.
-
Forming and Processing Challenges:
- Drawing and Extrusion Limitations: Pure tungsten cannot be drawn over a mandrel or extruded into a tube easily. This limitation complicates the manufacturing process and requires specialized equipment and techniques.
- Safety in Processing: The difficulties in forming and processing tungsten necessitate the use of specialized equipment, which may introduce additional safety hazards. Proper training and adherence to safety protocols are essential to mitigate these risks.
-
General Safety Precautions:
- Personal Protective Equipment (PPE): When working with tungsten, especially in machining or processing, the use of appropriate PPE such as gloves, safety glasses, and protective clothing is crucial to protect against potential injuries from sharp edges or flying debris.
- Environmental Controls: Ensuring proper ventilation and dust control is important, particularly during machining, to prevent inhalation of fine tungsten particles, which can be harmful to health.
In summary, while tungsten is a material with remarkable properties, its handling and processing come with significant safety concerns. These include challenges in machining due to loading, brittleness at low temperatures, and difficulties in forming and processing. Proper safety measures, including the use of appropriate PPE and environmental controls, are essential to mitigate these risks and ensure safe handling of tungsten in various applications.
Summary Table:
Safety Concern | Key Details |
---|---|
Machining Difficulties | - Loading issue with diamond tools, risk of tool damage and injury. |
- Requires alternative machining methods, increasing complexity and cost. | |
Brittleness at Low Temperatures | - High ductile-to-brittle transition temperature (DBTT). |
- Risk of fracturing or shattering if not handled carefully. | |
Forming and Processing Challenges | - Difficult to draw or extrude pure tungsten. |
- Requires specialized equipment, introducing additional safety hazards. | |
General Safety Precautions | - Use PPE (gloves, safety glasses, protective clothing). |
- Ensure proper ventilation and dust control during machining. |
Ensure safe handling of tungsten in your operations—contact our experts today for tailored solutions and advice!