The white spots on zirconia after sintering are typically caused by contamination or impurities that interfere with the proper densification and crystallization of the material during the sintering process. These spots can arise from various sources, such as improper handling, contamination from tools or materials, or residues from the pre-sintering stage. The presence of these spots can affect the structural integrity and aesthetic quality of the zirconia, making it crucial to identify and address the root causes to ensure optimal performance and appearance.
Key Points Explained:
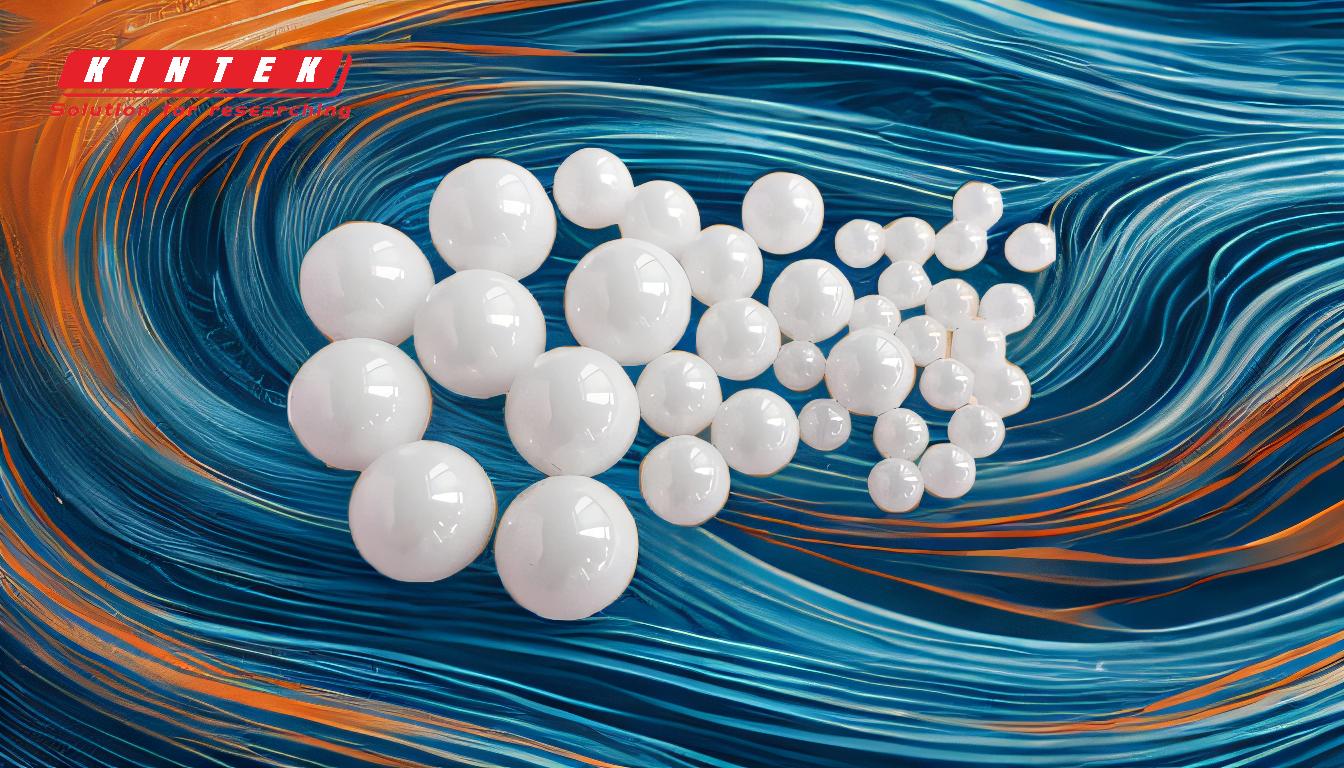
-
Causes of White Spots on Zirconia After Sintering:
- Contamination: Foreign particles or residues on the surface of the zirconia before sintering can lead to uneven densification, resulting in white spots. Contaminants may come from improper handling, unclean tools, or environmental factors.
- Improper Cleaning: Inadequate cleaning of the zirconia before sintering can leave behind residues from milling, polishing, or other pre-sintering processes, which can cause localized discoloration.
- Sintering Conditions: Incorrect sintering parameters, such as temperature, time, or atmosphere, can lead to incomplete densification or crystallization, resulting in white spots.
- Material Defects: Inherent flaws in the zirconia material, such as inconsistent composition or impurities, can also contribute to the formation of white spots.
-
Impact of White Spots:
- Structural Integrity: White spots can indicate areas of incomplete densification, which may weaken the material and reduce its mechanical properties, such as strength and fracture resistance.
- Aesthetic Quality: The presence of white spots can detract from the visual appeal of the zirconia, particularly in applications where aesthetics are critical, such as dental restorations.
- Performance: In functional applications, such as dental implants or industrial components, white spots may compromise the performance and longevity of the zirconia.
-
Prevention and Mitigation Strategies:
- Proper Handling and Cleaning: Ensure that the zirconia is handled with clean gloves and tools, and thoroughly cleaned before sintering to remove any residues or contaminants.
- Optimized Sintering Parameters: Use appropriate sintering conditions, including temperature, time, and atmosphere, to ensure complete densification and crystallization of the material.
- Quality Control: Implement rigorous quality control measures to detect and address any material defects or inconsistencies before sintering.
- Environmental Control: Maintain a clean and controlled environment during the handling and processing of zirconia to minimize the risk of contamination.
-
Troubleshooting and Correction:
- Inspection: After sintering, carefully inspect the zirconia for any signs of white spots or other defects. Use magnification or other inspection tools if necessary.
- Re-sintering: In some cases, re-sintering the zirconia under optimized conditions may help to reduce or eliminate white spots.
- Surface Treatment: If white spots are superficial, they may be removed through polishing or other surface treatments, though this may not address underlying structural issues.
By understanding the causes and implications of white spots on zirconia after sintering, and implementing appropriate prevention and mitigation strategies, it is possible to produce high-quality zirconia components with optimal structural and aesthetic properties.
Summary Table:
Aspect | Details |
---|---|
Causes | Contamination, improper cleaning, incorrect sintering conditions, material defects |
Impact | Reduced structural integrity, compromised aesthetics, and performance issues |
Prevention Strategies | Proper handling, optimized sintering, quality control, and environmental control |
Troubleshooting | Inspection, re-sintering, and surface treatment |
Need help resolving zirconia sintering issues? Contact our experts today for tailored solutions!