Physical Vapor Deposition (PVD) coating is a versatile process used to create thin, durable, and high-performance coatings on various substrates. The chemicals used in PVD coating depend on the desired properties of the final product, such as hardness, corrosion resistance, or color. The process typically involves vaporizing a target material, often a metal or ceramic, and depositing it onto a substrate in a vacuum environment. Reactive gases like nitrogen, oxygen, or acetylene are commonly introduced to form compounds such as nitrides, oxides, or carbides, which enhance the coating's properties. The choice of chemicals and gases depends on the specific application and the desired characteristics of the coating.
Key Points Explained:
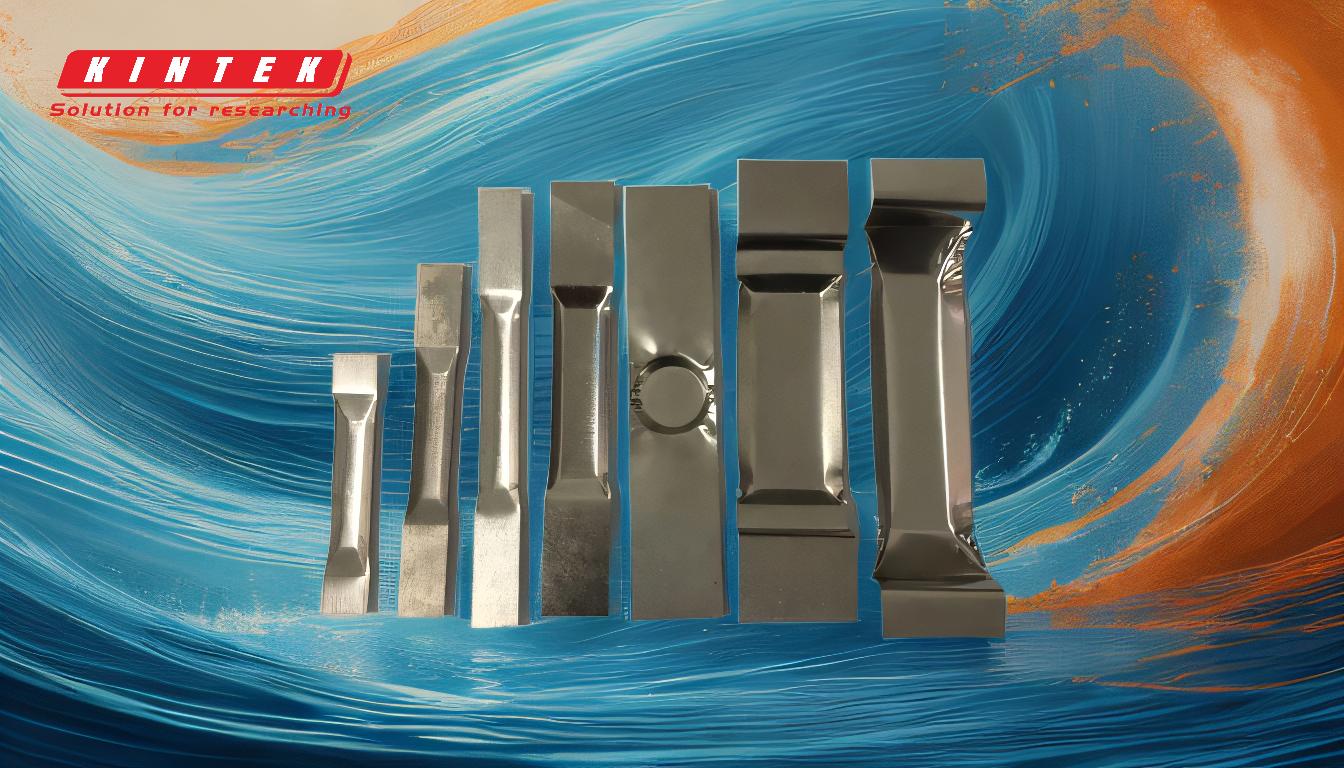
-
Target Materials in PVD Coating:
- PVD coatings often start with a target material, which is typically a metal or ceramic. Common metals include titanium, chromium, aluminum, and gold, while ceramics like silicon carbide or titanium nitride are also used.
- These materials are chosen based on the desired properties of the coating, such as hardness, wear resistance, or aesthetic appeal.
-
Reactive Gases Used in PVD:
- Reactive gases play a crucial role in PVD coating by combining with the vaporized target material to form compounds. Common gases include:
- Nitrogen (N₂): Used to create nitride coatings like titanium nitride (TiN), which are known for their hardness and gold-like appearance.
- Oxygen (O₂): Forms oxide coatings such as titanium dioxide (TiO₂), which are often used for optical or photocatalytic applications.
- Acetylene (C₂H₂): Used to create carbide coatings like titanium carbide (TiC), which are extremely hard and wear-resistant.
- Reactive gases play a crucial role in PVD coating by combining with the vaporized target material to form compounds. Common gases include:
-
Process Steps Involving Chemicals:
- Vaporization: The target material is vaporized using methods like sputtering or thermal evaporation. This step requires precise control of temperature and energy input.
- Reaction: The vaporized material reacts with the introduced gases to form compounds. For example, titanium reacts with nitrogen to form titanium nitride (TiN).
- Deposition: The reacted material is deposited onto the substrate in a controlled manner, forming a thin, uniform film.
-
Applications and Chemical Selection:
- The choice of chemicals depends on the application. For instance:
- Tool Coatings: Titanium nitride (TiN) is commonly used for cutting tools due to its hardness and wear resistance.
- Decorative Coatings: Gold or chromium-based coatings are used for aesthetic purposes.
- Optical Coatings: Oxides like titanium dioxide (TiO₂) are used for their reflective or anti-reflective properties.
- The choice of chemicals depends on the application. For instance:
-
Advantages of PVD Coating Chemicals:
- Purity: PVD coatings are highly pure due to the vacuum environment, which prevents contamination.
- Versatility: A wide range of materials and gases can be used, allowing for customization of coating properties.
- Durability: The resulting coatings are highly durable, resistant to wear, corrosion, and high temperatures.
-
Safety and Environmental Considerations:
- PVD coating is generally considered environmentally friendly compared to other coating methods like electroplating, as it produces fewer hazardous byproducts.
- However, proper handling of reactive gases and vacuum equipment is essential to ensure safety.
By carefully selecting the target materials and reactive gases, PVD coating can be tailored to meet specific performance requirements across various industries, from aerospace to consumer electronics.
Summary Table:
Category | Examples | Purpose |
---|---|---|
Target Materials | Titanium, Chromium, Aluminum, Gold | Provides hardness, wear resistance, or aesthetic appeal. |
Reactive Gases | Nitrogen (N₂), Oxygen (O₂), Acetylene (C₂H₂) | Forms nitrides, oxides, or carbides to enhance coating properties. |
Applications | Tool coatings, Decorative coatings, Optical coatings | Tailored for hardness, wear resistance, or reflective properties. |
Advantages | High purity, Versatility, Durability | Ensures contamination-free, customizable, and long-lasting coatings. |
Ready to enhance your materials with PVD coatings? Contact our experts today to get started!