Chemical vapor deposition (CVD) and physical vapor deposition (PVD) are two distinct thin-film deposition techniques used in various industrial applications. While both methods aim to deposit thin films onto substrates, they differ significantly in their processes, materials, and outcomes. CVD relies on chemical reactions between gaseous precursors and the substrate to form thin films, often requiring high temperatures and producing dense, uniform coatings. PVD, on the other hand, involves physically vaporizing a solid material and depositing it onto the substrate, typically at lower temperatures. PVD offers faster deposition rates and a broader range of materials but may result in less dense and uniform coatings compared to CVD. The choice between CVD and PVD depends on factors such as the desired material properties, substrate compatibility, and specific application requirements.
Key Points Explained:
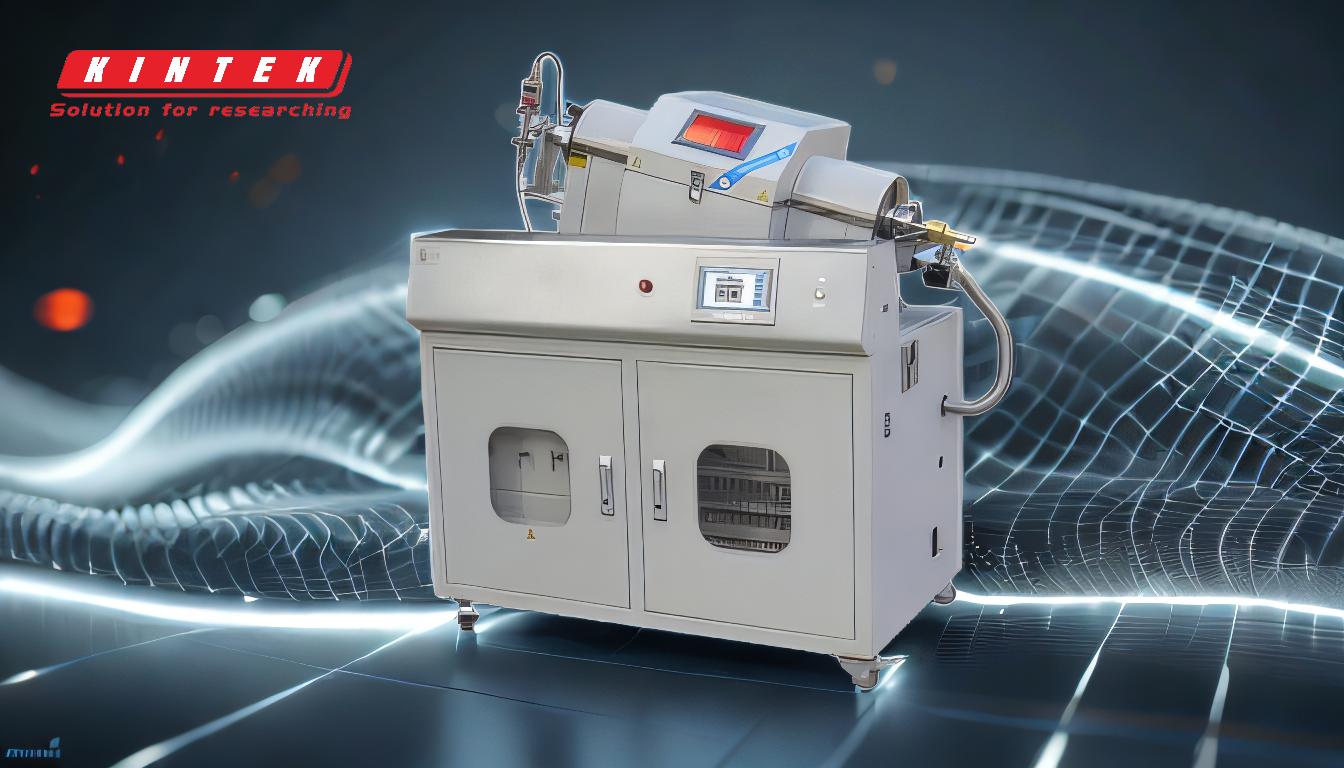
-
Process Mechanism:
- CVD: Involves chemical reactions between gaseous precursors and the substrate surface. The gaseous molecules react or decompose on the substrate to form a solid film. This process often requires high temperatures to activate the chemical reactions.
- PVD: Involves physical processes such as evaporation, sputtering, or ion plating to vaporize a solid material, which then condenses onto the substrate. No chemical reactions occur between the material and the substrate.
-
Material Range:
- CVD: Primarily used for depositing ceramics and polymers. The process is limited to materials that can be introduced as gaseous precursors.
- PVD: Can deposit a wider range of materials, including metals, alloys, and ceramics. This versatility makes PVD suitable for applications requiring diverse material properties.
-
Temperature Requirements:
- CVD: Typically requires higher temperatures to facilitate chemical reactions, which can limit its use with temperature-sensitive substrates.
- PVD: Operates at lower temperatures, making it more suitable for substrates that cannot withstand high heat.
-
Coating Properties:
- CVD: Produces dense, uniform, and high-purity coatings due to the chemical reaction process. However, the process may leave impurities or produce corrosive byproducts.
- PVD: Coatings are generally less dense and uniform but can be applied more quickly. PVD coatings are free from chemical byproducts, making them cleaner in some applications.
-
Deposition Rate:
- CVD: Generally slower due to the need for chemical reactions to occur at the substrate surface.
- PVD: Offers faster deposition rates, especially in techniques like electron beam physical vapor deposition (EBPVD), which can achieve rates of 0.1 to 100 μm/min.
-
Safety and Environmental Considerations:
- CVD: Uses volatile chemicals that can produce harmful gases, requiring stringent safety measures and ventilation systems.
- PVD: Safer to operate as it does not involve hazardous chemicals or produce harmful byproducts.
-
Application Suitability:
- CVD: Preferred for applications requiring high-quality, uniform coatings, such as semiconductor manufacturing and advanced ceramics.
- PVD: More suitable for industrial applications like cutting tool coatings, where lower temperatures and faster deposition rates are advantageous.
-
Line of Sight and Coating Uniformity:
- CVD: Does not require a direct line of sight between the precursor source and the substrate, allowing for uniform coating of complex geometries and multiple parts simultaneously.
- PVD: Requires a line of sight, which can limit its ability to coat complex shapes uniformly.
In summary, the choice between CVD and PVD depends on the specific requirements of the application, including the desired material properties, substrate compatibility, and operational constraints. While CVD offers superior coating quality and uniformity, PVD provides greater material versatility and faster deposition rates, making each method uniquely suited to different industrial needs.
Summary Table:
Aspect | CVD | PVD |
---|---|---|
Process Mechanism | Chemical reactions between gaseous precursors and substrate | Physical vaporization of solid material, no chemical reactions |
Material Range | Primarily ceramics and polymers | Metals, alloys, ceramics, and more |
Temperature | High temperatures required | Lower temperatures, suitable for heat-sensitive substrates |
Coating Properties | Dense, uniform, high-purity coatings | Less dense, faster deposition, cleaner coatings |
Deposition Rate | Slower due to chemical reactions | Faster, especially with techniques like EBPVD |
Safety | Uses volatile chemicals, requires safety measures | Safer, no hazardous chemicals or byproducts |
Application Suitability | High-quality coatings for semiconductors, advanced ceramics | Industrial applications like cutting tool coatings |
Line of Sight | No line of sight required, uniform coating of complex geometries | Requires line of sight, limited for complex shapes |
Need help choosing between CVD and PVD for your application? Contact our experts today for tailored advice!