Coatings on carbide tools play a crucial role in enhancing their performance, durability, and efficiency in various machining applications. These coatings are applied to the surface of carbide tools to improve their resistance to wear, heat, and chemical reactions, thereby extending their lifespan and maintaining cutting precision. By reducing friction and preventing material buildup, coatings also contribute to smoother operations and better surface finishes on the workpiece. Additionally, they enable higher cutting speeds and feed rates, which can significantly boost productivity in industrial settings. Overall, coatings are essential for optimizing the functionality of carbide tools in demanding environments.
Key Points Explained:
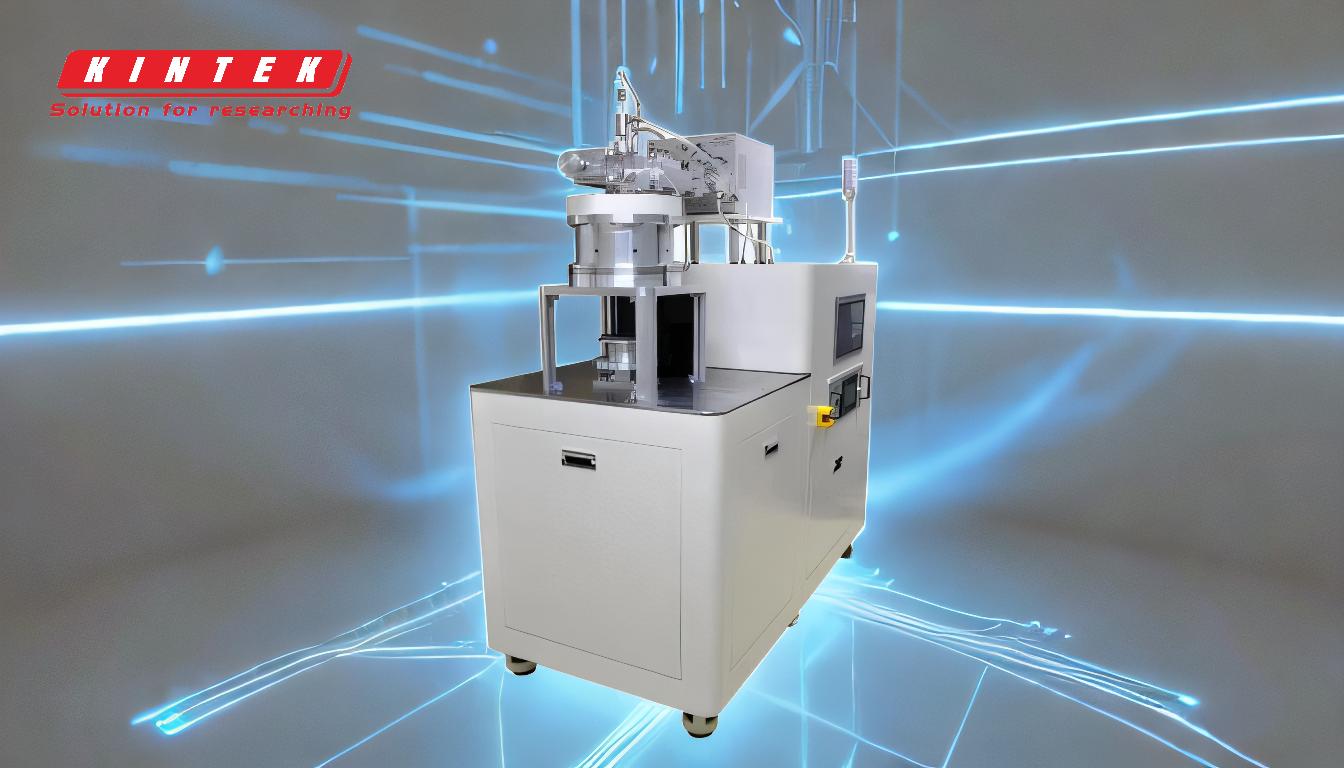
-
Enhanced Wear Resistance:
- Coatings on carbide tools significantly improve their resistance to wear, which is critical in high-stress machining operations.
- Materials like titanium nitride (TiN), titanium carbonitride (TiCN), and aluminum titanium nitride (AlTiN) are commonly used for their hardness and durability.
- These coatings form a protective layer that reduces direct contact between the tool and the workpiece, minimizing abrasive wear and extending the tool's life.
-
Improved Heat Resistance:
- Carbide tools often operate under high temperatures, which can lead to thermal degradation and reduced performance.
- Coatings such as AlTiN and titanium aluminum nitride (TiAlN) provide excellent thermal stability, allowing the tools to withstand extreme heat without losing their structural integrity.
- This heat resistance helps maintain the tool's cutting edge sharpness and prevents premature failure.
-
Reduced Friction and Material Buildup:
- Coatings like diamond-like carbon (DLC) and molybdenum disulfide (MoS2) are designed to lower the coefficient of friction between the tool and the workpiece.
- Reduced friction leads to smoother cutting operations, less energy consumption, and lower heat generation.
- Additionally, these coatings prevent material from sticking to the tool surface, reducing the risk of built-up edge (BUE) and ensuring consistent cutting performance.
-
Chemical Stability:
- Certain coatings provide chemical inertness, protecting the tool from reactions with the workpiece material or cutting fluids.
- For example, chromium nitride (CrN) coatings are highly resistant to corrosion and oxidation, making them suitable for machining corrosive materials like stainless steel or titanium.
- This chemical stability ensures that the tool maintains its performance even in harsh environments.
-
Increased Cutting Speeds and Feed Rates:
- The combination of wear resistance, heat resistance, and reduced friction allows coated carbide tools to operate at higher speeds and feed rates.
- This capability translates to faster machining times and improved productivity, which is particularly beneficial in high-volume manufacturing settings.
- Higher cutting speeds also reduce the time the tool spends in contact with the workpiece, further minimizing wear and heat buildup.
-
Better Surface Finish:
- Coatings contribute to achieving superior surface finishes on the workpiece by ensuring consistent and precise cutting.
- The reduced friction and material buildup prevent imperfections such as burrs or rough edges, resulting in smoother and more accurate machined parts.
- This is especially important in industries where surface quality is critical, such as aerospace or medical device manufacturing.
-
Cost Efficiency:
- Although coated carbide tools may have a higher initial cost compared to uncoated tools, their extended lifespan and improved performance often lead to long-term cost savings.
- Reduced tool replacement frequency, lower energy consumption, and increased productivity contribute to a higher return on investment.
- Additionally, the ability to handle tougher materials and more demanding applications can open up new opportunities for manufacturers.
In summary, coatings on carbide tools are essential for enhancing their performance and durability in various machining applications. By improving wear resistance, heat resistance, and chemical stability, while reducing friction and material buildup, these coatings enable higher cutting speeds, better surface finishes, and overall cost efficiency. This makes coated carbide tools a valuable asset in modern manufacturing and industrial processes.
Summary Table:
Benefit | Description |
---|---|
Enhanced Wear Resistance | Coatings like TiN, TiCN, and AlTiN reduce abrasive wear, extending tool life. |
Improved Heat Resistance | AlTiN and TiAlN coatings provide thermal stability for high-temperature use. |
Reduced Friction | DLC and MoS2 coatings lower friction, ensuring smoother operations. |
Chemical Stability | CrN coatings resist corrosion, ideal for machining corrosive materials. |
Higher Cutting Speeds | Enables faster machining, boosting productivity in industrial settings. |
Better Surface Finish | Prevents imperfections, ensuring smoother and more accurate machined parts. |
Cost Efficiency | Longer tool lifespan and improved performance lead to long-term cost savings. |
Optimize your machining process with coated carbide tools—contact us today to learn more!